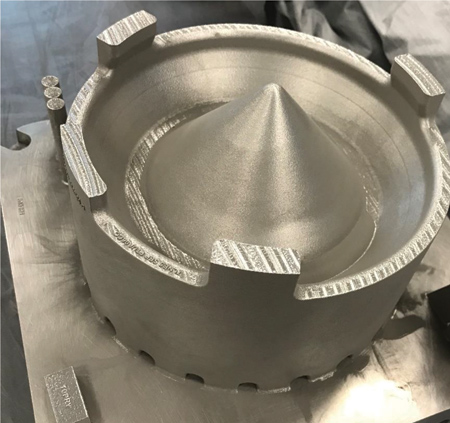
An additively manufactured cobalt-chrome sump cover for an F110 engine. It was produced on a GE Additive Concept Laser M2 machine at the GE Additive Technology Center in Cincinnati as part of collaboration with the US Air Force's Rapid Sustainment Office (RSO).
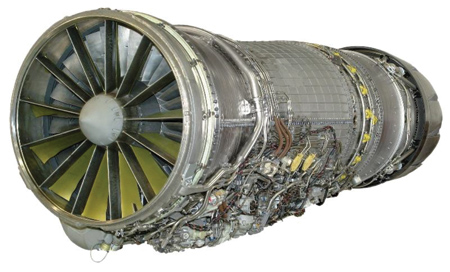
GE Aviation F110 engine
GE Aviation has received Engineering Change Proposal (ECP) approval from the US Air Force (USAF) for an F110 additively manufactured sump cover. The latest milestone in the USAF and GE's pathfinder Pacer Edge program, this F110 component is the first engine component designed for and produced by metal additive manufacturing (AM) to be qualified by any US Department of Defense entity.
"The Pacer Edge program is an important initiative for reducing risk and showcasing the application of AM in aerospace. The ability to AM an aircraft engine part and gain military airworthiness is a significant step forward in growing the adoption of AM in the Air Force," said Nathan Parker, Deputy Program Executive Officer for the USAF RSO.
"The entire Pacer Edge process is built around our `accelerate change' philosophy, and the speed of the F110 sump cover development and airworthiness approval is evidence of that. The capability that Pacer Edge is demonstrating and proving will be a game changer to engine production and sustainment and will resolve many future Air Force readiness challenges," said John Sneden, Director of the USAF's Directorate of Propulsion.
Close collaboration and knowledge sharing have enhanced USAF's spiral development approach of continuously identifying, reverse engineering and developing technical data packages (TDPs) for increasingly complex and larger parts suitable for metal AM.
"USAF's strong vision for additive as part of its wider sustainment and readiness strategy has allowed our combined team to progress at speed. We continue to share our learnings and have developed an efficient, structured way of working-especially for developing qualification processes and expediting design iterations. This lean, operational efficiency is already driving results and now sets us up for the next phases of the program, including looking at complex and large format load-carrying structures," said Matt Szolwinski, Chief Engineer and leader of GE's Large Military Engineering team.
Phase 1b is already underway and focuses on an out-of-production sump cover housing on the TF34 engine, which has been in service more than 40 years.
"We started with a relatively easy part, but the spiral development model is coming into its own. It provides focus for the team and our experts help navigate and problem solve along the way," said Lisa Coroa-Bockley, General Manager for GE's Advanced Materials Solutions.
A digital thread also runs through the pathfinder. GE experts focused on digital twinning, maintenance-based predictive analytics and part lifecycle management expertise that complement the USAF's digital engineering strategy and in-house knowledge.
"Additive is a powerful digital technology that spans the entire process, from design and modeling to in-situ monitoring through to inspection and final level assurances," said Coroa-Bockley. "Adding digital twinning and predictive analytics brings new horizons into view, such as systems management, diagnostics and repair of in-field systems."
"Subsequent phases of the Pacer Edge program involve the establishment of a metal AM supply chain at Tinker Air Force Base in Oklahoma that will be capable of producing airworthy components in support of the DoD's sustainment needs," said Lauren Tubesing, Director-Military Accounts at GE Additive.
For more information contact:
GE Additive
www.ge.com