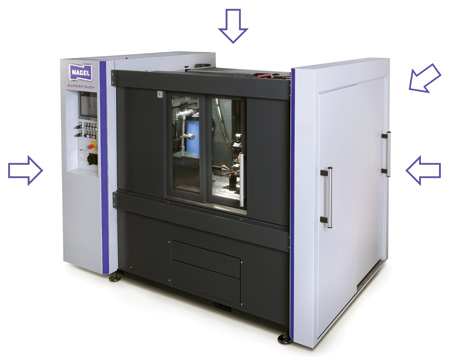
The NaShaft Eco-Superfinish centers from Nagel can be automated in different ways. Due to several sliding doors and openings, loading is possible from almost all sides and also from above (arrows).
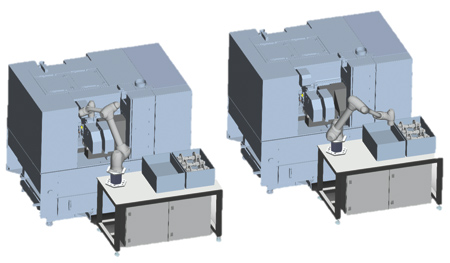
For flexible manufacturing applications, cobots can be implemented with the NaShaft Eco-Superfinish centers.
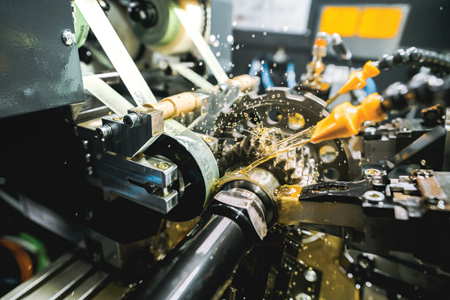
Hybrid processes, i.e. stone and tape processing, can be carried out on the NaShaft Eco-Superfinish centers. Combination processes such as brushing and polishing are also available.
"With the increasing spread of electric vehicles, the issue of smooth running is gaining in importance. This also increases the demand for superfinishing technology," said a Nagel Maschinen- und Werkzeugfabrik spokesperson.
"We are noticing that demand for our Superfinish technology is by no means slowing down with the trend toward eMobility," said Christian Feuchter, Technical Sales at Nagel. "On the contrary, the typical workpieces for combustion engines are becoming fewer, but those for eDrives are increasing, especially transmission and rotor shafts. At the same time, machining requirements are increasing. Other components are also on the rise regardless of the type of drive, including steering racks and nuts, for example."
The automotive supplier ZF uses Nagel's NaShaft series superfinishing centers for eTransmission shafts. "Finishing is an increasingly required manufacturing process in the area of eMobility," said the spokesperson. "The aim is to increase the load-bearing capacity of the workpieces and to reduce short wave lengths."
The spokesperson continued, "eDrives, unlike combustion engines, generate operating noise at a very low level. The surrounding bearing points become audible with a whirring noise. This is caused by the waviness of the bearing journals, which is inevitably left behind by the pre-processes of turning and grinding. Where components make themselves heard in this way, friction and losses are also higher-another undesirable side effect. As a consequence, drive manufacturers are raising their quality requirements for dimensional accuracy and surface finish. After all, the vehicles are supposed to roll along the streets as quietly as a whisper. Against this background, superfinishing is becoming a key technology in the production chains of eDrive components since only this type of superfinishing is capable of eliminating the ripples."
When it became apparent at ZF that the need for superfinishing capacity was increasing, the company decided to purchase a new superfinishing center, the NaShaft Eco 612 machine from Nagel.
"This machine proved to be the best system for our application," said the ZF process planner. "It is loaded by a gantry loader through the roof hatch and will be fully integrated into a belt linking system at a later stage."
ZF uses the NaShaft Eco 612 for various transmission shafts with overall lengths from 150 to 380 with bearing journals in the range D = 30 mm to 60 mm. Tension is applied between centers. After grinding, the values for cylinder shape and surface finish are around 8 µm and Rz 2.5 µm. The targets for superfinishing are <5 µm and Rz <0.7 µm. Nagel developed a hybrid process for this task.
"There is a stone process and a tape process," said Feuchter. "The stone process ensures an improvement of the waviness on the bearing journals and therefore optimizes the cylinder shape or the shape accuracy. The subsequent tape process improves the surface quality."
The NaShaft Eco finishing center is equipped with four finishing modules. The shafts to be machined have two bearing locations. Consequently, both bearing journals can be machined simultaneously, first in the stone process and then in the tape process. Machining time for one shaft is 15 seconds.
"Our Superfinish center meets all the user's quality and productivity specifications," said Feuchter. "The application example is proof that flexibility and a modular design are important criteria. In order to meet high quality requirements, it is not always necessary to have high specifications."
The NaShaft series features a modular design but uses standard components, allowing short delivery times. The machines can be adapted to changing market conditions. According to Nagel, the energy consumption of the systems is comparatively low.
Key features of the NaShaft Eco superfinishing centers:
- Small footprint due to compact machine design
- Workpiece lengths: Center width up to 650 mm (greater than 1,000 mm is possible depending on the application)
- All common workpiece fixtures adaptable
- Swing diameter: 250 mm (larger diameters are also possible depending on the application)
- Several finish modules designed for hybrid processing (stone, tape)
- Combination processes, e.g. brushing and polishing, are possible
- Several NC-axis adjustments or high degree of automation by NC-axes
- Control: Siemens S7 with 15" touchscreen
- Loading options: From the sides or from above (robot, cobot, gantry loader)
- Integrated rinsing agent preparation, 200 l (no separate tank necessary)
- Movable and vibration decoupled central module
- Tool cabinet with organizer wall and compartments
- Push-to-open drawers with interchangeable parts.
For more information contact:
Nagel Precision, Inc.
288 Dino Drive
Ann Arbor, MI 48103
734-426-5650
info@nagelusa.com
www.nagelusa.com