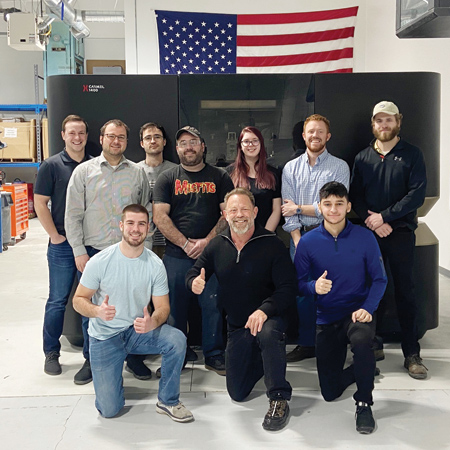
The Azoth team with the new XJet Carmel 1400M AM System.
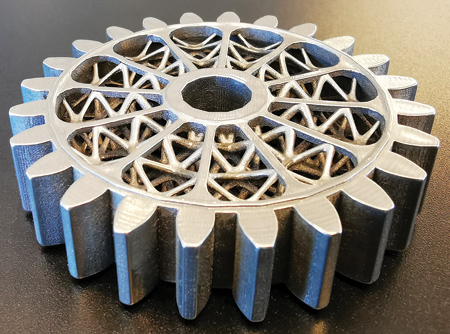
XJet is designed to make stainless steel parts with fine features, high resolution and smooth surface finish right off the printer.
Additive manufacturing (AM) specialist Azoth has received XJet's first Carmel 1400M metal AM System, a metal and ceramic material jetting system.
"We have a huge wealth of experience in metal manufacturing with both additive and subtractive processes. XJet's metal system delivers capabilities that are in high demand in the market but are not achievable with other technologies," said Scott Burk, Azoth CEO, "Parts with fine features, high resolution, good surface finish right off the printer are possible. The ease of use and safety working with the XJet system, which does not involve handling powders, is another important factor for us."
Burk and Cody Cochran, Azoth General Manager and co-founder, were looking for a solution to serve market demand for small, complex, high-definition parts that they could not do with existing powder-bed fusion or binder jetting systems.
"What we really liked were the small holes, very sharp corners, very refined surface finish without needing any post-processing," said Cochran. "We are also impressed with the science behind XJet's NanoParticle Jetting technology. It prints with very small particles, smaller than other technologies. These characteristics allow for process advantages, smaller layer heights and smaller features."
Hanan Gothait, XJet CEO, said, "We have developed the only metal AM technology available today based on the concept of direct material jetting. After success with the XJet ceramic systems, we are now ready for the bigger dream, bringing to the market our metal solution. It gives me great pleasure to know that our first user of the metal AM system is Azoth, with so much experience in metal manufacturing and in metal AM."
In addition to quality of parts, Azoth expects to see operational advantages with the XJet Carmel system. "One of the main advantages of Azoth's approach is going from prototype to production with the same process, which XJet technology is perfectly suited to support," said Cochran. "We will be able to take parts from a multitude of industries, such as automotive, medical, tooling, etc. and prototype them, refine them into end-use components and bring them to production with the same machine. No expensive additional tooling or lengthy lead times. Making end-user parts requires precision, accuracy and repeatability from part to part. By almost automating the entire workflow, as XJet does, we think we can achieve true repeatability."
For more information contact:
Azoth
1099 Highland Drive
Ann Arbor, MI 48108
734-669-3797
info@azoth3d.com
www.azoth3d.com
XJet
info@xjet3d.com
www.xjet3d.com