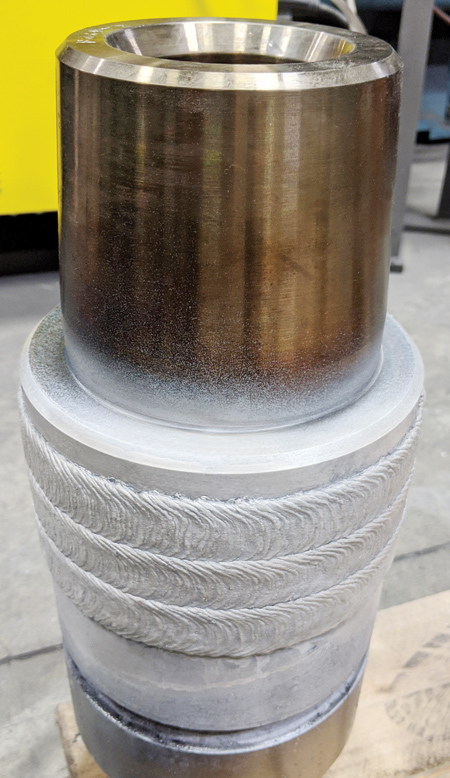
Stoody HB-64 cored wire, shown here passing a die-pentetrant test, has been awarded Fearnley Procter NS-1 Level 2 certification for drill pipe application and reapplication.
Stoody, an ESAB brand, announced that Stoody HB-64 cored wire has been awarded Fearnley Procter NS-1 Level 2 certification for oil field hardbanding application and reapplication.
Stoody HB-64 (60 to 64 Rockwell C hardness) is a tool steel alloy enhanced with niobium carbide for improved performance and crack-free hardbanding. Its specially formulated wear resistant alloy composition produces a uniform distribution of small primary metal carbides in a martensitic matrix. Stoody HB-64 provides a weld deposit with a low coefficient of friction to reduce tool joint and casing wear. According to the company, it shows excellent abrasion resistance under the hardbanding conditions. Stoody HB-64 is approved under NS-1 for new hardbanding applications as well as for reapplication onto itself.
"The Stoody HB-64 has already been tested extensively in multiple oil fields," said Guy Chouinard, R&D Engineering Manager, ESAB. "It offers better hardbanding performance, allowing operators to drill more holes before the pipe tool joint needs resurfacing."
Stoody HB-64 cored wire is sold in a 33 lb. (15 kg) wire basket or a 50 lb. (22.7 kg) moisture protected Poly Pak, both in 1/16" (1.6 mm) diameter.
The Fearnley Procter NS-1 accreditation program provides oilfield equipment and service companies with an industry-recognized approval program that supplements the requirements of American Petroleum Institute (API) standards and demonstrates high quality management and performance to offshore and onshore operators.
"NS-1 certification also ensures that the welding process and specifications given to the welders in the field allow the product to be applied consistently and effectively, ensuring sufficient service life while preserving the well casing," said Chouinard.
Oil and gas drilling involves numerous lengths of threaded pipe adding to one another to form the drill string as the well is being completed. Hardbanding is a protective weld overlay applied on each drill pipe end, or connection, aiming at protecting the tool joint from wear against the rock face or the well casing. The tool joint hardbanding allows the drill string to last for the completion of the well without also causing premature wear of the casing. Losing the tool to abrasion would involve very costly downtime and piercing the casing would imply severe environmental consequences.
Stoody HB-56 cored wire previously achieved NS-1 Level 2 certification. Stoody HB-56 is casing friendly and approved for new applications or reapplication over itself. Stoody HB-56 produces a crack-free martensitic steel deposit with enhanced wear resistance and weldability.
For more information contact:
ESAB Welding & Cutting Products
800-ESAB-123
www.esabna.com