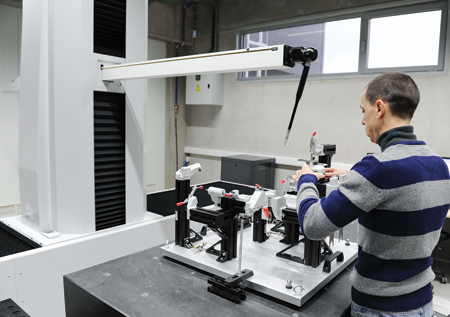
A modular fixture with additively manufactured locators being inspected on the LK CMM

Inspection programs are generated offline using LK's CAMIO8 software
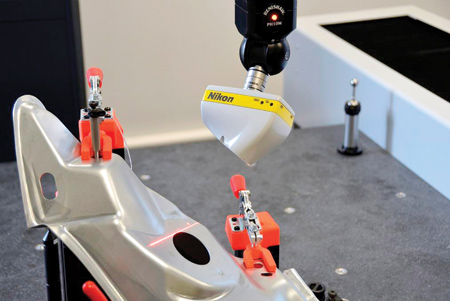
The Nikon Metrology laser scanning head deployed on the LK CM at RapidFit
Materialise Group spin-off RapidFit has deployed a horizontal-arm coordinate measuring machine (CMM) manufactured by LK Metrology to check the accuracy of custom gauging and holding fixtures produced for the automotive industry.
RapidFit has reduced costs and lead times by making use of additive manufacturing (AM) to produce workpiece locators that are added to standard fixture components. The technology enables vehicle production to be streamlined, as innovative fixtures can be constructed with enhanced functionality and better repeatability.
"Often, this is achieved by incorporating complex clamping elements with freeform contours that are traditionally produced by conventional machining, which can be expensive, time consuming and creates a lot of waste material," said a spokesperson. "Integration of intelligent quick-release mechanisms that do not damage the component being retained is another possibility. Even moving elements like hinges can be printed, as well as features such as clips, pins and holes."
High-wear plastics are used to manufacture the components, sometimes with steel inserts or bushings. Alternatively, parts can be produced from aluminum-filled nylon powder, allowing robust elements to be printed that may be subsequently milled and drilled to an accuracy of ± 0.05 mm.
Users of the fixtures are mainly manufacturers of plastic and composite components for vehicles, from relatively simple, light housings or small sheet metal parts to full body panels, dashboards and bumpers for sports cars. Customers include automotive OEMs such as Audi, Bentley, Lamborghini and Volvo as well as leading players in their supply chains, for example Mecaplast and Valeo.
"Shorter lead-time from receipt of order to delivery of the fixture, especially when complex geometries are involved, is a result of not having to program a milling machine to remove typically 90% of material from an aluminum billet, or expending time and expense having a casting made and then machining it," said the spokesperson. "Users are given more time and flexibility to fine-tune their product designs and still meet deadlines. An added advantage is that the locators and contours are typically half the weight of their conventionally machined equivalents and therefore the fixture is lighter and less tiring for operators to use."
A high degree of modularity is provided using standard holding elements, such as the Aluquick range from Horst Witte, to support the custom 3D printed locators. The system allows easy modification by simply replacing them, so fixtures can be reconfigured inexpensively to accommodate design changes.
Accuracy is Critical for RapidFit Customers
The patented, customized products supplied by RapidFit are of two types. Gauge fixtures are for inspecting automotive components after manufacture to verify their accuracy, while holding fixtures support components as they are built into a vehicle and measured using CMMs or other metrology equipment. Both types provide comprehensive management of dimensional accuracy, which is vital to the overall quality of the final vehicle.
This in turn means that quality control of the fixtures is crucial. There was a need at the Leuven facility for higher accuracy when checking fixture calibration. To achieve this, an LK HC90 40.16.16 premium performance horizontal arm CMM was purchased, together with the manufacturer's CAMIO8 multi-sensor programming and analysis software. The machine provides almost unrestricted access to its 4 m x 1.6 m x 1.6 m measuring envelope and features ceramic guideways and air bearings for stability at high velocity and acceleration.
A Renishaw PH10-MQ motorized indexing head with in-quill head mount and auto-joint probe mount together with a TP200 touch trigger probe and various extension bars formed part of the package. The HC90 is housed in a climate-controlled metrology room and is currently operated over a single shift.
Stefan Roeding, Marketing Manager at RapidFit, commented, "Customers will only accept measurement results if they trust the equipment that generates them. The accuracy and repeatability of the LK CMM is very high for its large size. It can measure two of our fixtures at a time, resulting in high productivity in the inspection department. Installation of the machine has been a big step forward in assuring the quality of our products before delivery and avoiding costly reworking. It is fulfilling all of our customers' requirements."
Filip Dehing, RapidFit's CEO, added, "With a worldwide sales and support network, our company is in an ideal position to grow by becoming a preferred partner for large automotive companies on a global scale and by fully exploiting new opportunities. Underpinning all of this is our commitment to high quality. Our inspection department with the LK Metrology CMM breathes accuracy, making it an important marketing tool when customers and prospects visit us."
Offline Programming Maximizes Use of the CMM
A typical project at RapidFit starts with the customer sending a CAD drawing of the component to be fixtured and instructions on how it should be clamped for the required application. The fixture is virtually constructed in CATIA by one of RapidFit's nine design engineers, and the 3D locator elements are output as STL files so that they can be produced in one of the company's powder laser-sintering AM machines.
After 3D printing, the locators are assembled with standard holding elements and a measuring program is created in CAMIO8, in this case offline in RapidFit's Kiev subsidiary, which allows maximum use to be made of the CMM for inspection. Since each fixture is different, ease of programming based on the original CAD file is a critical advantage.
The program is transferred to the LK HC90 and the inspection cycle is run to verify that all fixture dimensions are in tolerance. If changes are needed, engineers modify the fixture and run the cycle again. Measuring program changes can be made quickly in teach mode if necessary.
Turn-around for a fixture of average complexity is three to four weeks, although a very complex fixture can take up to six weeks. The customer is invited to the RapidFit measurement room for acceptance and sign-off.
More recently, for checking contours faster, the manufacturer has added laser scanning capability to the CMM by purchasing an LC15Dx from Nikon Metrology. It is interchangeable with the touch probes and both are supported by LK's CAMIO8 software. "The technology offers twice the resolution of camera-based optical systems, so is suitable for quality control of RapidFit's automotive fixtures. It is therefore replacing relatively slow touch probing routines in parts of the cycle that involve collection of freeform data," said the spokesperson.
For more information contact:
LK Metrology, Inc.
29550 W.K. Smith Drive, Unit B
New Hudson, MI 48165
810-263-6100
sales.us@lkmetrology.com
www.lkmetrology.com