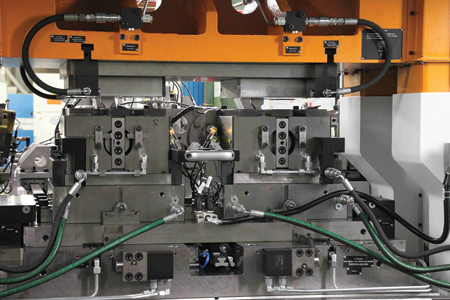
"Unlike most other ball cage punching machines, in which multiple components need to be taken apart in order to retool, on the Karl Klink machine the cutting punch and its holder can be exchanged with the punch tool in place. Furthermore, no unreliable adjustment spindles and clamps are needed," said a spokesperson.
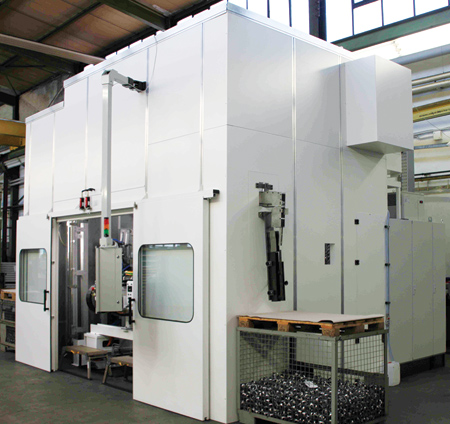
In order to shorten retooling times and boost output, Karl Klink GmbH developed the RT-HLKK1000 high-performance automatic ball cage punching machine.
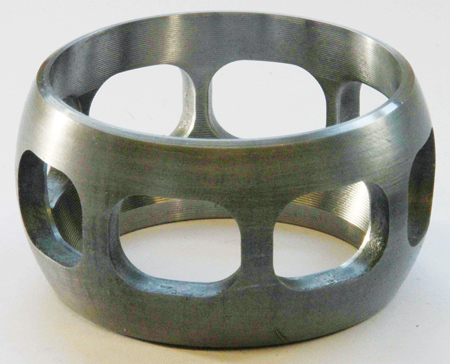
In addition to versions with six windows, ball cages with four, eight or ten windows are also used in CV joints.
Between four and eight ball cages are installed in every vehicle-meaning that the automotive industry needs at least half a billion of these components every year.
"Up to now, most automatic ball cage punching machines work by flywheel drive," said a Karl Klink GmbH spokesperson. "Consequently, the cutting speed and surface quality in the cut area are comparatively low, as is output. The need to manufacture different types of cages also means regular tool changes, resulting in extensive retooling and thus down times. Karl Klink GmbH has come up with a solution: the RT-HLKK1000 punching machine is designed with a servo drive, which reduces the cycle time to 7.3 sec. per piece. At the same time, the better cut quality minimizes finishing costs and time. Its innovative design slashes tool changing time from several hours to 30 minutes per tool change, greatly increasing the machine availability."
"Ball cages are made in over 80 different versions. Automobile manufacturers often outsource variants with low unit quantities and lot sizes to suppliers," said Robert Keller, Director Stamping Technology at Karl Klink GmbH. "That presents a great challenge to these companies. For one thing, these suppliers have to do tool changes, significantly lowering machine availability and raising costs. For another, the flywheel drive used so far by most punching machines results in fixed slide kinematics, yielding relatively low cut quality and output."
The problem was brought to the attention of Karl Klink GmbH by discussions with an automotive supplier at the Blechexpo fair in Stuttgart a few years ago. Based on this feedback, the company developed a high-performance automatic ball cage punching machine that meets users' advanced requirements for high cut quality and shorter retooling times. The RT-HLKK1000 automatic punching machine is based on the prototype presented in 2015, but with new improvements. "The power source sets the Klink machine apart. Instead of a flywheel, it uses a servo drive, which improves both the cutting speed and the cut quality. Thus, it has been possible to combine higher quality with higher productivity," said the spokesperson.
The machine has two die stations. Workpieces are fed from both sides and can be finished in different variants simultaneously, independently of each other. The ball cages can also be fed from either side, punched at the first station and then trimmed at the second, with feeding as chosen by the operator. The parameters for each station can be separately set via the control panel. The 100% part inspection measures and adjusts the position of the cages in the feeding and discharge unit. The parts are verified in the process: incorrect and out of spec parts are automatically rejected, leading to higher efficiency. For ball cages with six windows, including punching and trimming, cycle times of 7.3 sec are possible (for eight-window cages with two-side feed without trimming it is as low as 8.2 sec per two pieces, 4.1 sec per piece). "This is in contrast to the 10+ sec for the same punching operation on comparable presses of conventional design. In three-shift work without retooling, this means an increased volume of 11,835 parts per day or 2,840,547 per year, versus the 8,388 per day or 2,013,203 per year achievable with conventional machines. This can boost output by 827,344 workpieces per year, which represents a productivity increase of more than 40%," said Keller.
Another goal was to design the punching machine so that ball cage manufacturers can react as flexibly as possible to all different order scenarios. This flexibility allows production of ball cages with outside dimensions from 45 mm to 120 mm. The number of windows and position correction per window are likewise freely programmable, making it possible to produce many geometries. To speed up retooling time, Karl Klink moved the retooling process out of the narrow confines of the machine to an external retooling point. The tool transfer is accomplished with a tool changing cart. Once there, almost all the necessary parameters can be changed with ease. Hydraulic functions are available too, for example to adjust the cutting gap. "The die for the next order can be set up during ongoing production. Thus, retooling is done in auxiliary process time," reported Keller. "The cutting punch and its holder can be replaced with the punch tool installed, further shortening the process. The improved access makes tool changes go even faster."
For more information contact:
Karl Klink GmbH
info@karl-klink.de
www.karl-klink.de