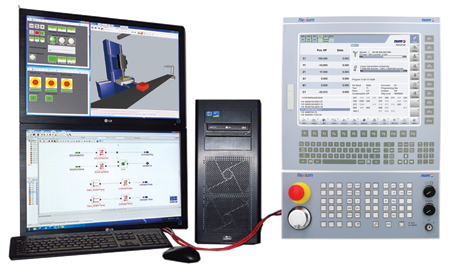
NUM's digital twin technology is designed to enable machine tool manufacturers to reduce their time to market.
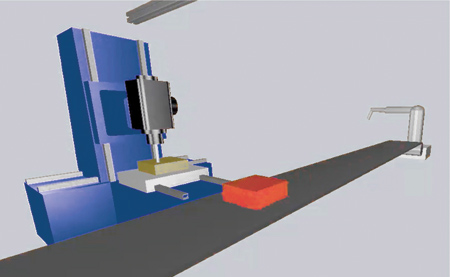
3D simulation realistically illustrates the dynamic operation of the machine.
CNC specialist NUM has launched digital twin technology that enables machine tool manufacturers to reduce their time to market by using Industry 4.0 simulation techniques.
"Originally known as pairing technology, and first used by NASA in the early days of space exploration, digital twin technology is now rapidly gaining industry acceptance as one of the most cost-effective means of accelerating the development of products, processes and services," said a company spokesperson.
For automation products such as machine tools, a digital twin is a virtual model that uses simulation, real-time data acquisition/analysis and machine learning techniques to allow full evaluation of a machine's dynamic performance before constructing a physical prototype. The same technology can also be employed for customer presentations, virtual commissioning and operator training purposes-and all well before the actual machine itself has even been built.
NUM offers two versions of digital twin technology to suit customers' needs. Both versions are designed for use with NUM's open-architecture Flexium+ CNC platform. One version uses a naked Flexium+ controller and resident virtualization software running on the system's industrial PC to simulate the twinned machine automation. The other version uses the actual Flexium+ controller that will eventually be incorporated into the machine, linked via EtherCAT to a standalone PC running specialist high-speed hardware simulation software to represent the mechatronics of the twinned machine.
The virtual controller version includes a software development kit for creating the software model of the machine. The model is a standalone PLC program that uses predefined components to simulate individual machine elements, such as sensors, spindles, pneumatic cylinders, etc. It is loaded into the integrated PLC of the Flexium+ controller.
The Flexium NCK in the controller executes the NC programs and simulates the changing position values of the machine's axes. To help users visualize the process, NUM's package includes the CODESYS Depictor software tool produced by CODESYS GmbH, which is used to produce 3D visualizations from the IEC 61131-3 code created by the simulation.
The other version of NUM's digital twin technology package accommodates real-time data acquisition and analysis. It is based on the ISG-Virtuous hardware simulation software produced by Industrielle Steuerungstechnik GmbH (ISG). The Flexium+ controller intended to be used in the physical machine is connected via an EtherCAT network to a standard PC and interacts with the simulation software in real time. The PC acts as the twinned virtual machine-with all simulated, virtual components behaving like real components in terms of their interfaces, parameters and operating modes-to accurately replicate the structure and dynamic performance of the real machine. The movements of the machine are displayed realistically on the PC, using the supplied 3D simulation software.
"NUM's new digital twin technology provides machine tool manufacturers with a very powerful and cost-effective means of reducing their development costs and accelerating their time to market," said the spokesperson. "The virtual controller version is especially useful for the early development stage of a project, before the CNC system has been finalized, while the real-time hardware simulation version has the advantage that all sequencing (PLC) and motion control (CNC) programs that are created during development can simply be transferred to the real machine as soon as it becomes available."
For more information contact:
Steve Schilling
NUM Corporation
603 East Diehl Road, Suite 115
Naperville, IL 60563
630-505-7722
sales.us@num.com
www.num.com