

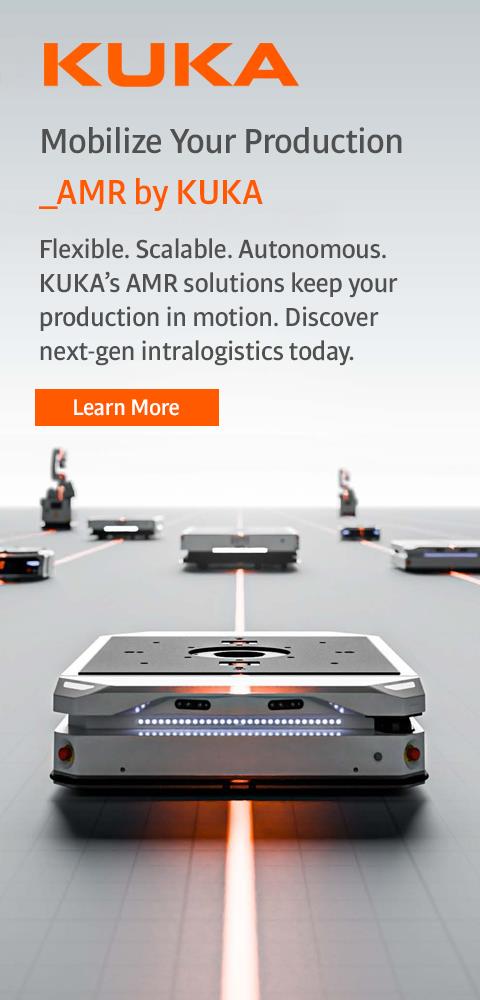
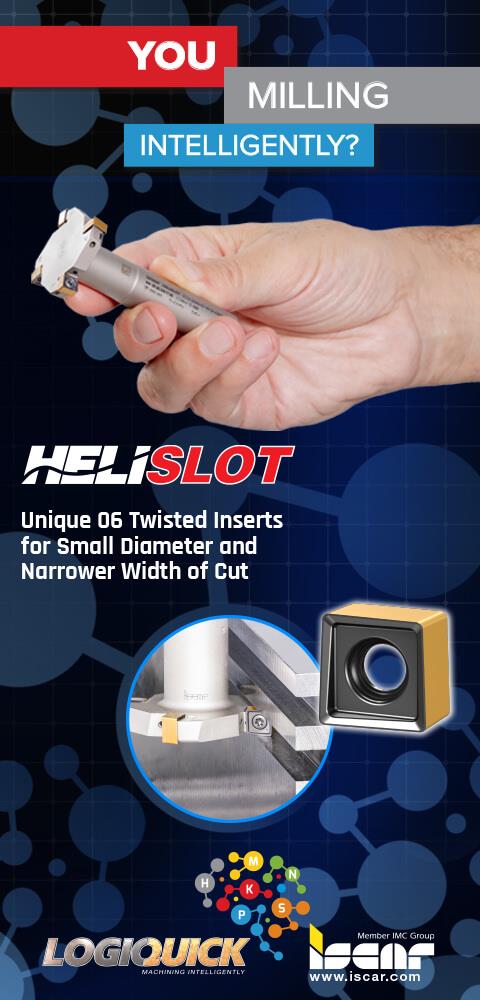
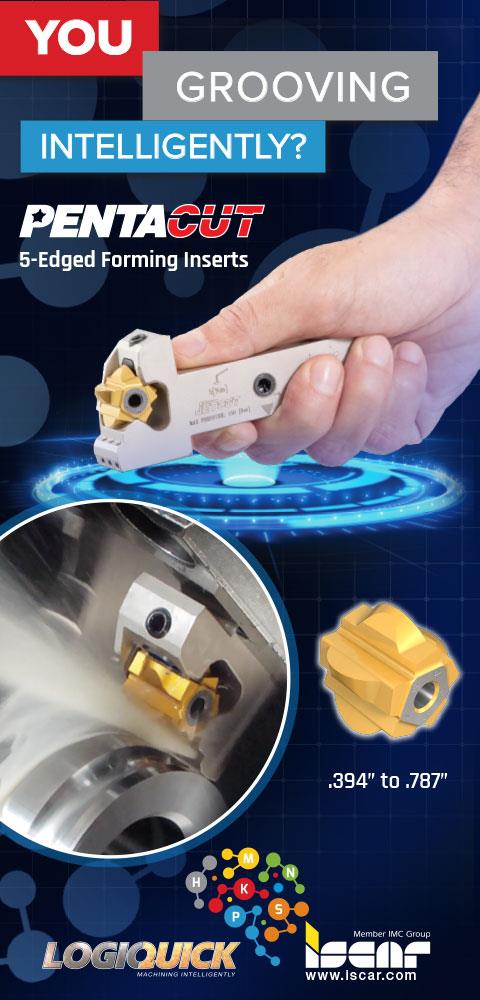
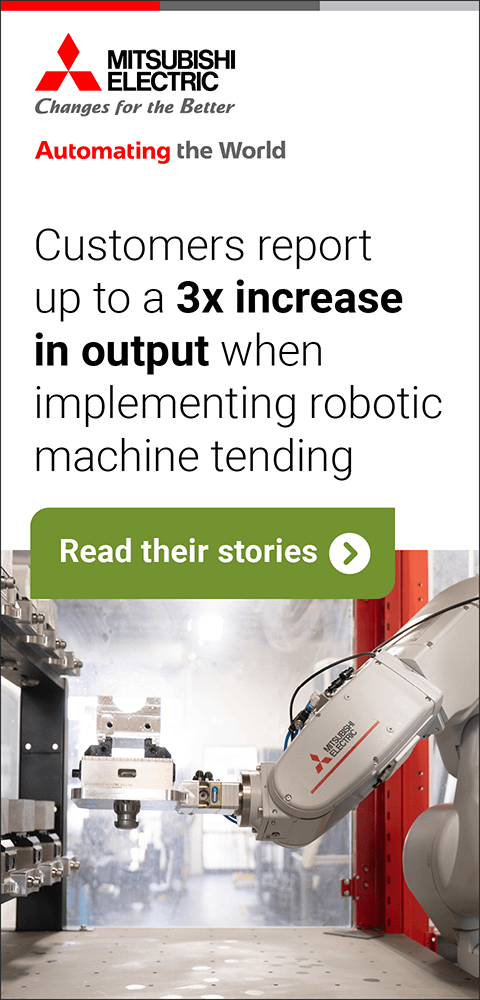
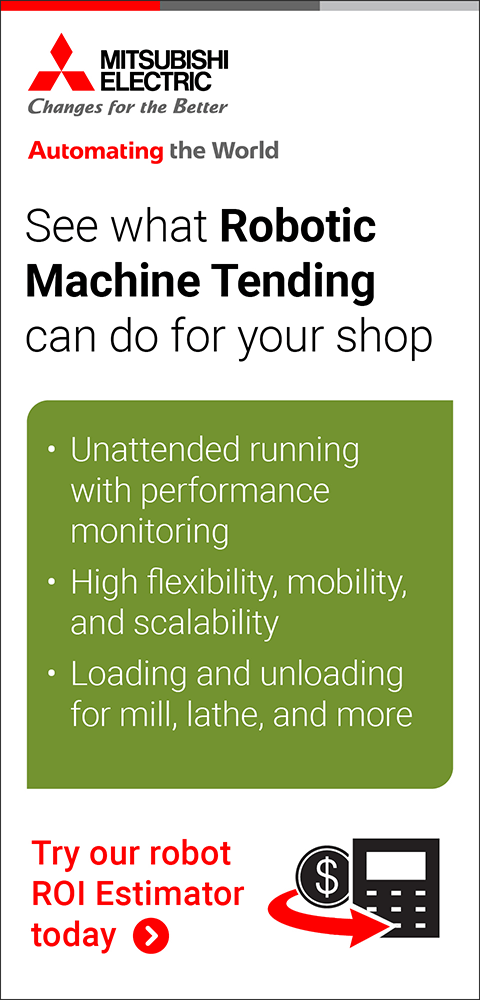
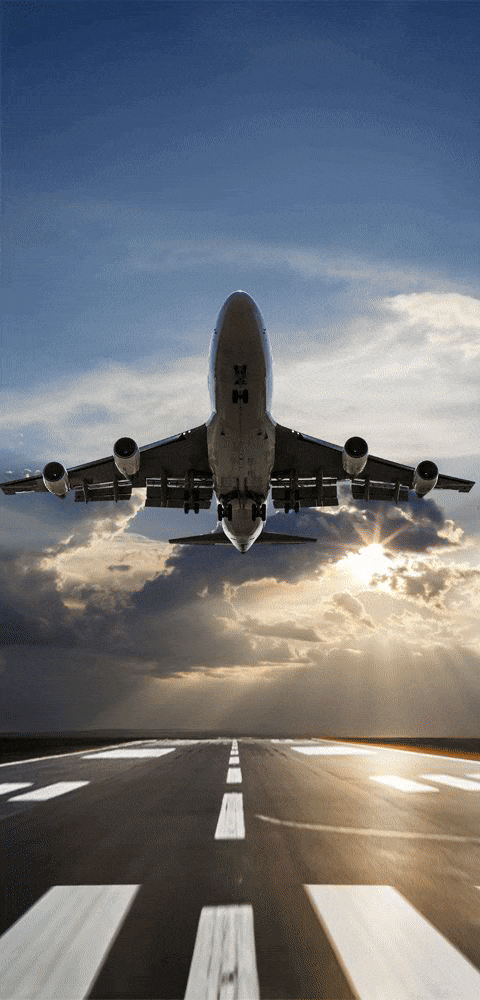
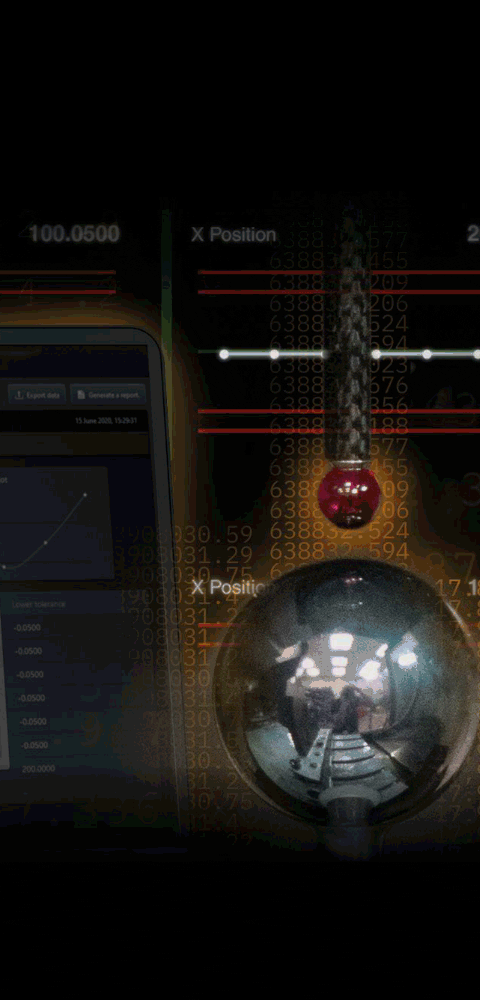
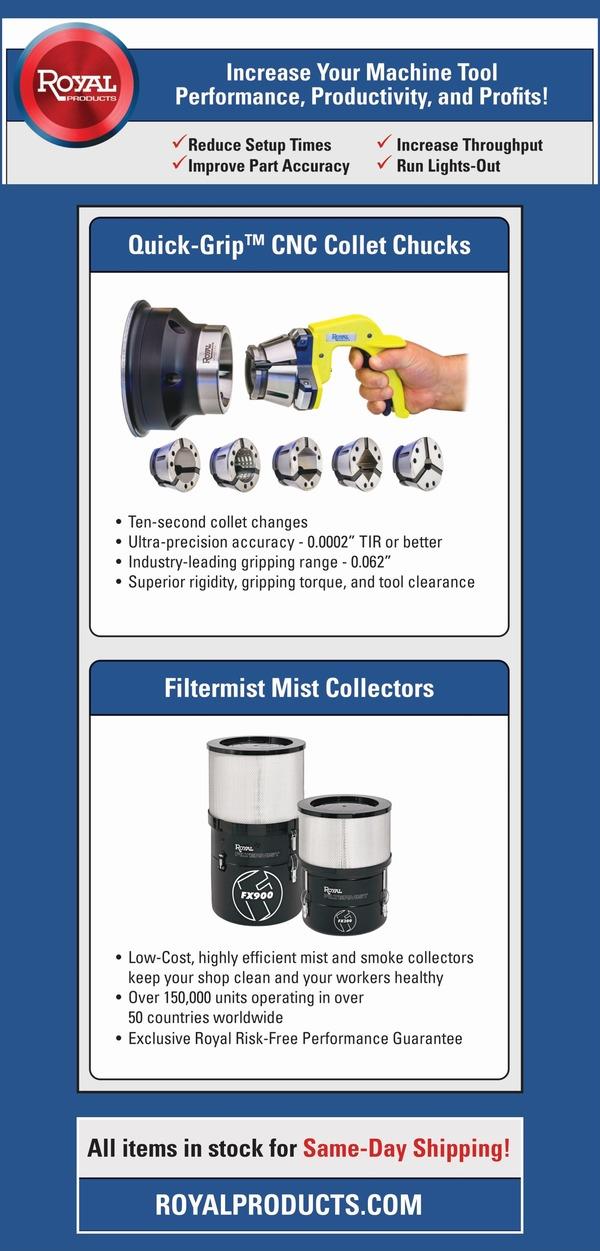
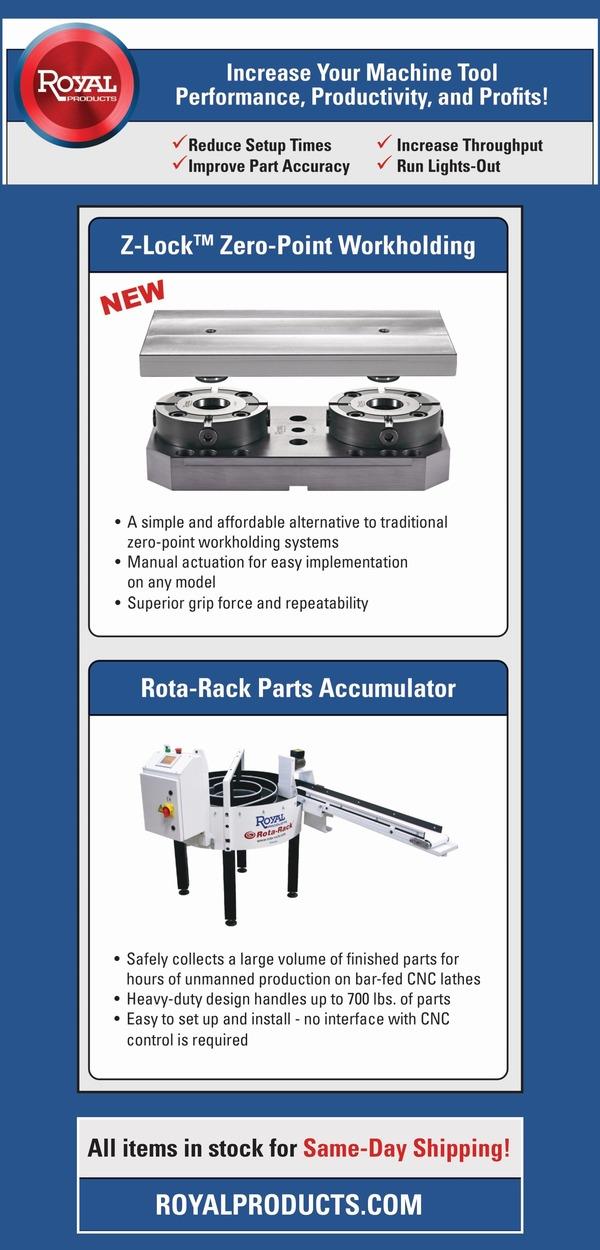
Automated Robotic Deburring Machine
November 1, 2020
Deburring is the process of removing small raised edges or pieces of metal (burrs) from the surface of a part typically seen in machined metal parts. "Traditionally, hand deburring and/or batch deburring are used to remove burrs," said a Bel Air spokesperson. "However, these options come with potential drawbacks. Hand deburring can be time consuming and filled with human error, driving up labor costs. Tumblers and centrifugal disk finishers can be excellent ways to deburr batches of parts. However, part on part collision can cause defects when two or more free flowing parts collide and scrape/chip each other's surfaces. In order to avoid this, finishing machines are available that secure parts while also providing deburring and polishing in an automated process."
Bel Air has developed The AutoHone, a reverse drag finisher. "Unlike traditional drag finishers, the reverse drag finisher rotates media instead of parts," said the spokesperson. "It then dips parts into the flowing media held within a rotating bin. The AutoHone combines this with robotic automation, enabling a turn-key solution to deburring, polishing, cleaning and drying. The unique robot arm enables five dimensional motions, meaning parts can be inserted into finishing media at unique angles tailored to specific finishing specifications. Following the finishing process, the robotic arm cleans the part within the optional ultrasonic cleaning station and can also dry the part in the optional drying station before placing the part back into the tray. The AutoHone is capable of processing parts in as little as 5 seconds. It can also extend the life of cutting tools by up to 300%. This applies to both coated and uncoated parts."
Tool honing with the AutoHone reduces the friction of cutting tools by removing microscopic burrs and sharp edges, increasing cutting speed and providing a surface to which coatings can better adhere. When pre-coated pieces are honed, the AutoHone removes microscopic irregularities on the surface of the tool. These irregularities happen when parts are coated and the coating is unevenly distributed across the part's surface. The removal of these irregularities reduces the friction of cutting tools on surfaces and increases the cutting speed.
AutoHone is designed to process medical, automotive, aerospace, fire arms, machined parts and 3D printed parts. It is available with options to better adapt to a variety of manufacturing environments.
For more information contact:
Bel Air Finishing Supply, Inc.
101 Circuit Drive
North Kingston, RI 02852
401-667-7902
info@belairfinishing.com
www.belairfinishing.com
< back