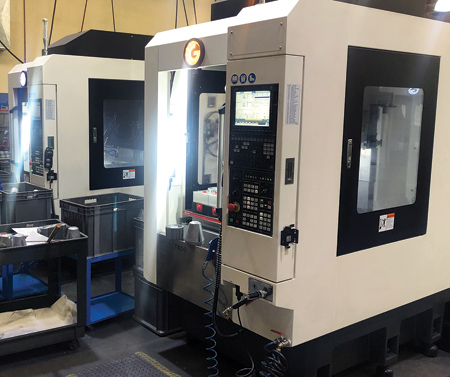
This GenMill milling center at Vista Professional Outdoor Lighting, used for machining the company's mid-sized commercial bullet/up-light, allows for increased precision of mating surfaces, threaded holes and wireways.
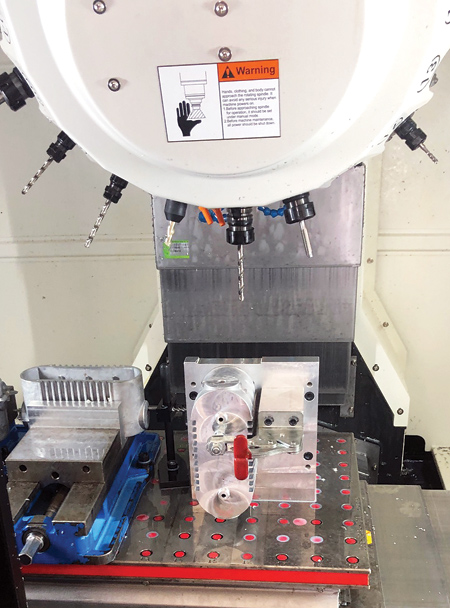
The GenMill milling center provides increased precision of mating surfaces, threaded holes and wireways. The precision milled mating surfaces allow for considerable thermal transfer, allowing Vista's fixtures to be run aggressively and providing a higher quality assembly process. In-house made workholding allows Vista to get its parts into the machine quickly and securely.
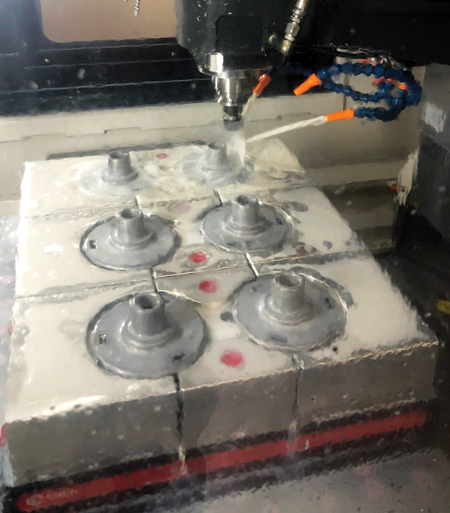
The GenMill milling center provides Vista with increased precision, even in higher volume applications.
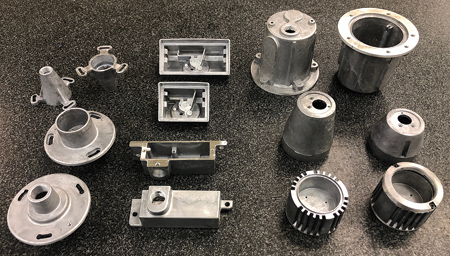
Examples of products that previously required single operation set-ups and now utilize multiple tool, multiple pass operations on the GenMill milling stations.
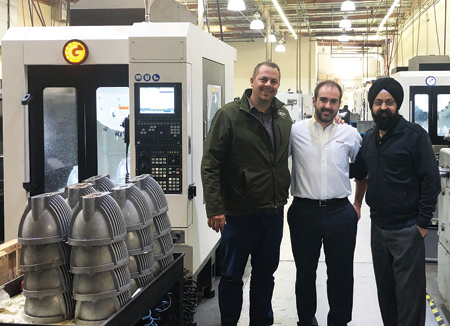
(l-r) Michael Anger, Sales Manager, Protek CNC; Nicholas Giacomino, Technical Account Manager, Mitsubishi Electric Automation Inc.; and Ravjeet Singh, General Manager, Expand Machinery
Vista Professional Outdoor Lighting, a supplier and innovator in the architectural and landscape lighting industry, manufactures its products at the company's headquarters in Simi Valley, CA, using a vertically-integrated manufacturing process. Recently it faced the need to reduce labor on manually intensive secondary operations (after die casting), including trim dies, drilling, tapping, light machining and sanding. A solution was needed to eliminate these operations and reduce labor at its California headquarters, where labor rates are increasing annually.
Options considered included:
- Relatively few large table CNC machines versus small machines (more spindles) with quick change tooling.
- Modern alternatives to sanding and grinding
- Outsourcing production to Mexico or overseas.
Vista ultimately selected a number of small footprint, small table machines with multiple quick-change vises in the form of GenMill drill and tap centers and Chick tooling. The GenMill machines were sold, serviced and tooled by Protek CNC, the local distributor for Expand Machinery's line of GenMill CNC machine tools.
"The solution is meeting our expectations," said Vista owner Dan Cunado. "Labor has been significantly reduced, overtime has been eliminated, part to part changeover is very fast, and part quality and surface finish have improved. Errors from drilling, tapping and over sanding have been eliminated, and the secondary operations bottle neck has been eliminated. Another major advantage is that the solution prevented outsourcing to China and kept manufacturing in USA."
Products are die cast aluminum for the outdoor landscape lighting industry. Machines are GenMill T500s and T700s. "Because chip production was going to be minimal, we went with no through spindle coolant and no chip conveyors," said Cunado. Chick workholding systems are being used on all machines to make part changeover time as short as possible.
Previously, the manufacturing process required die casting, manual trimming (hand and grinder or sander), drilling, tapping, light machining/clean up, finish sanding and tumbling. Each process required light jigging and/or short set-up since the operations were manual. Processing time was highly variable, especially in manual sanding operations.
Most notable in the new process has been the elimination of idle time between batches at each operation, which included travel plus queue times. Chick tooling maintains low set-up time and fast changeover. Because multiple machines (spindles) were purchased, maximum agility was gained across many parts with varying demand, from low to high volume.
Parts now come direct from die casting and are held without trimming. After trim, drill, tap, light machining and cleanup, parts go straight to tumbling before paint. Finished parts are now much cleaner and more consistent dimensionally, and all rejects from secondary operations have been eliminated.
In business and expanding its operations since 1984, Vista designs, manufactures and supplies a wide range of distinctive lighting fixtures, transformers, HID ballasts and accessories for the lighting professional. Vista manufactures products for both the low voltage and line voltage lighting markets.
Vista custom-builds and ships each fixture in less than 24 hours from the receipt of the distributor's order. Company capabilities include die casting, secondary operations, spinning, turning, CNC, toolmaking and maintenance, powder coat, light assembly and sheet metal fabrication.
For more information contact:
Vista Professional Outdoor Lighting
1625 Surveyor Ave.
Simi Valley, CA 93063
800-766-8478
email@vistapro.com
Expand Machinery
20869 Plummer St.
Chatsworth, CA 91311
888-542-6374 / 818-349-9166
info@ganeshmachinery.com
www.ganeshmachinery.com
WEST Only
S. CA
Protek CNC Sales Corp.
25 W Easy St., Unit 306
Simi Valley, CA 93065
805-579-9995
protekm@protekcnc.com
www.protekcnc.com