

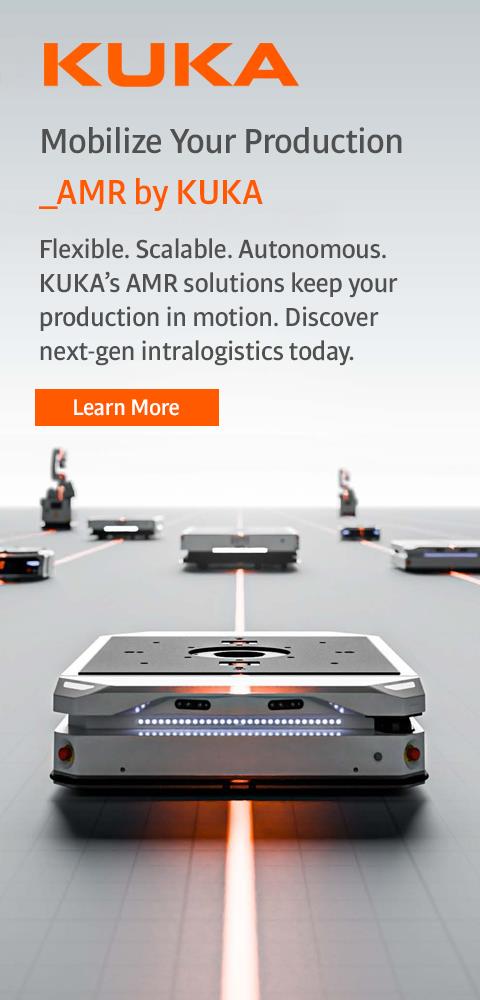
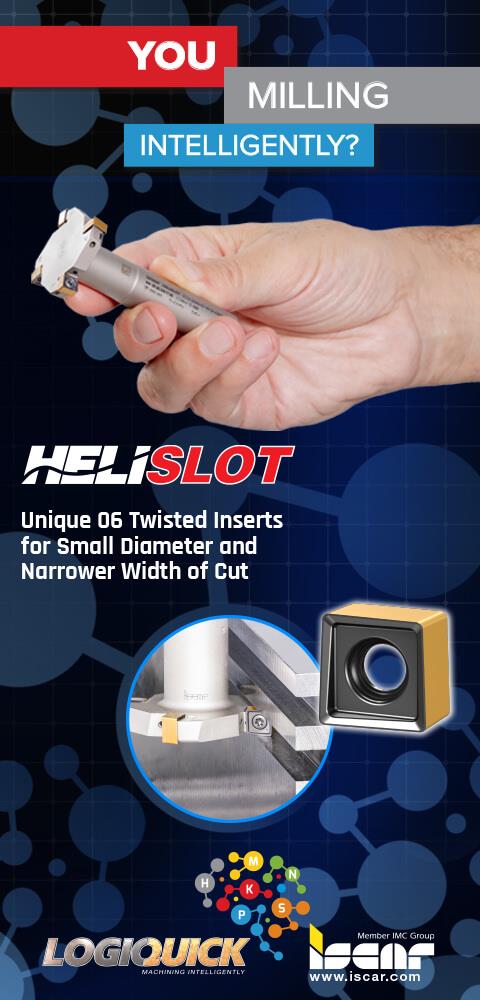
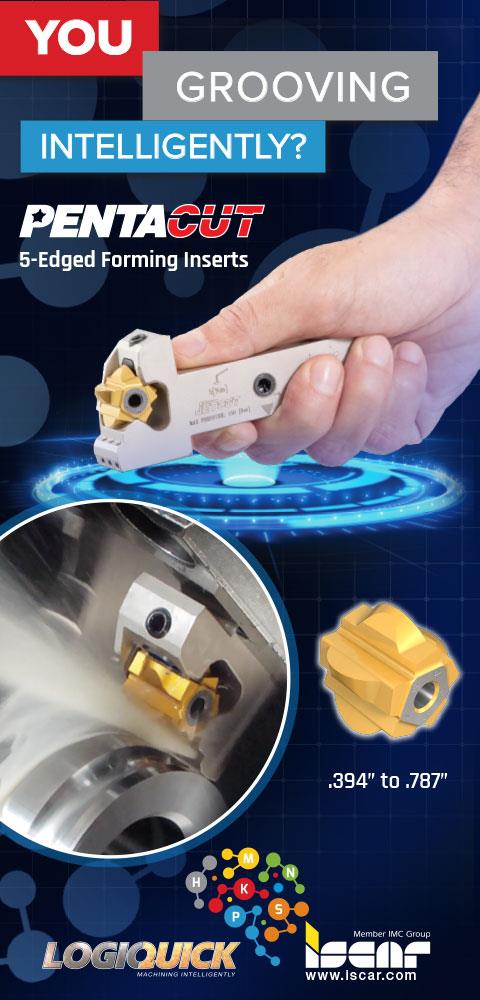
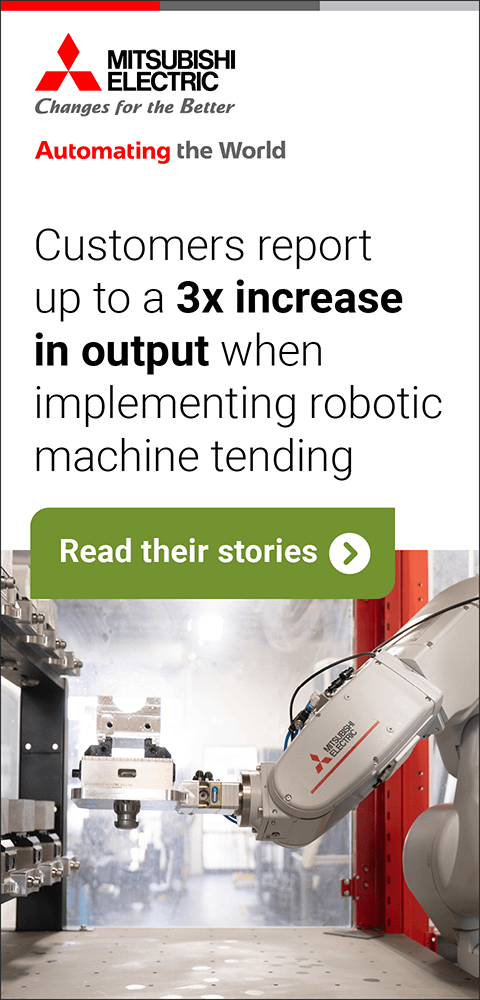
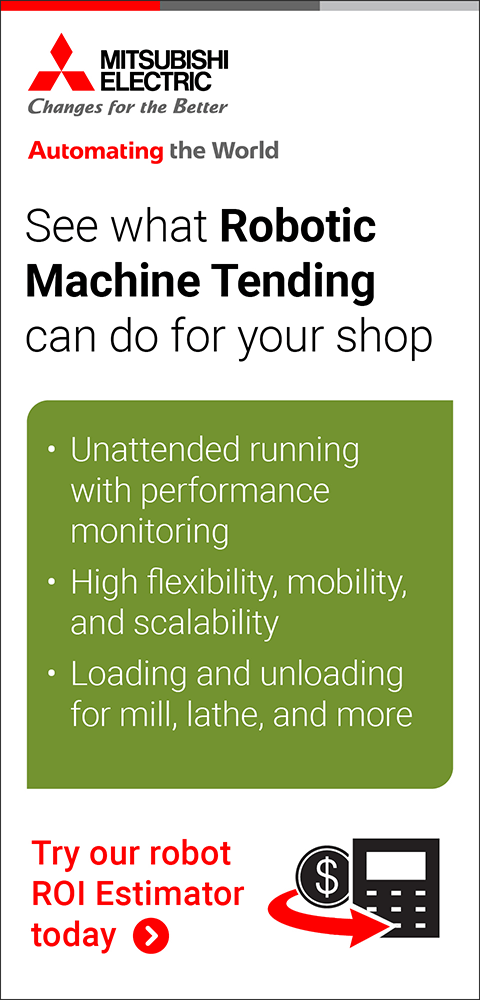
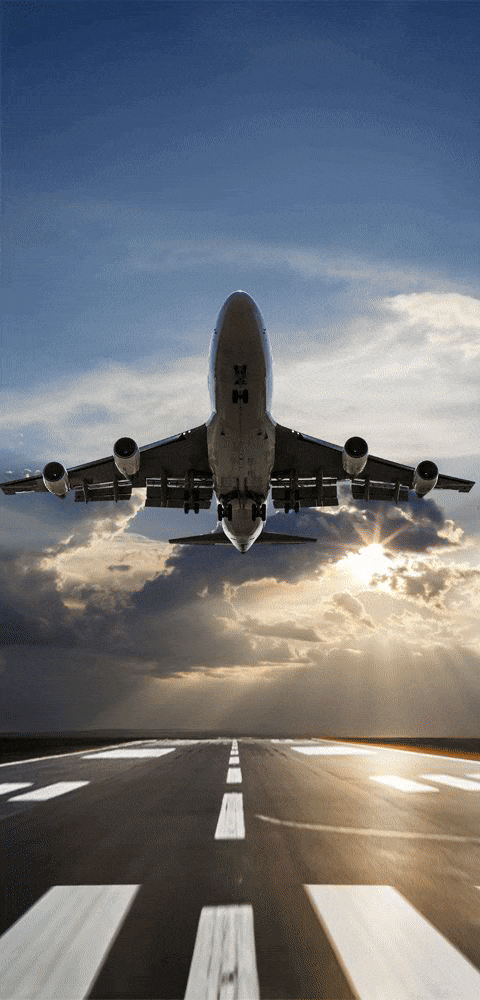
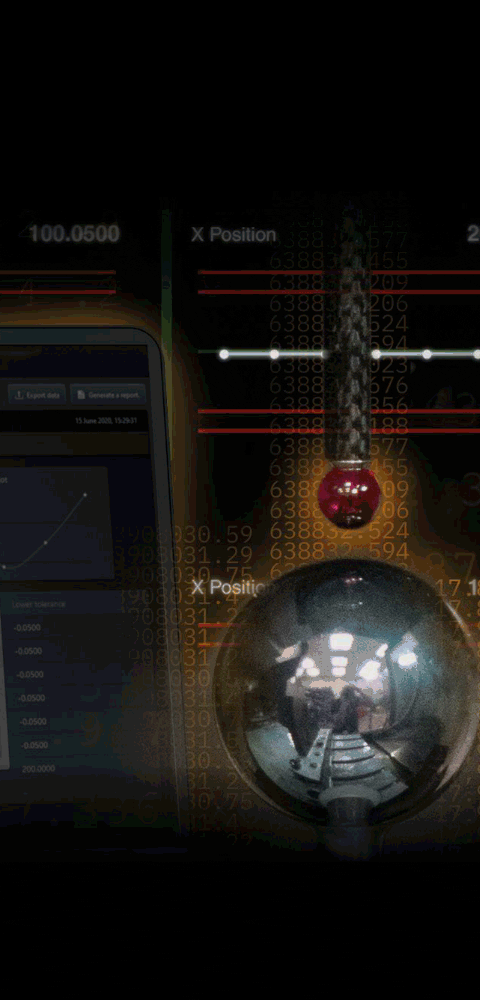
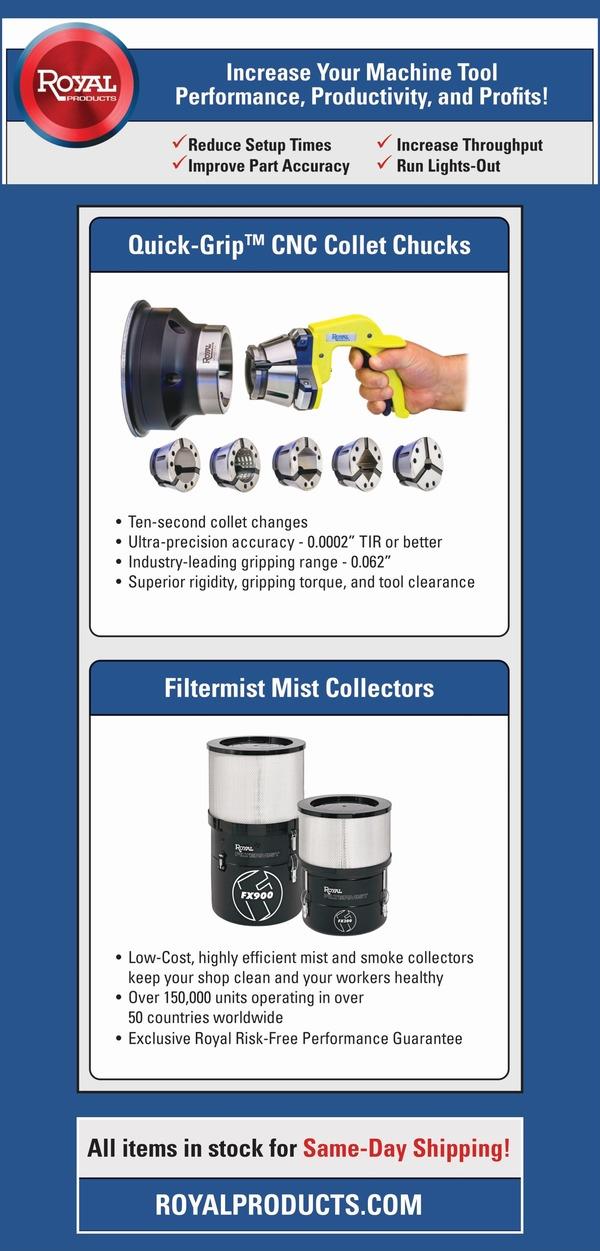
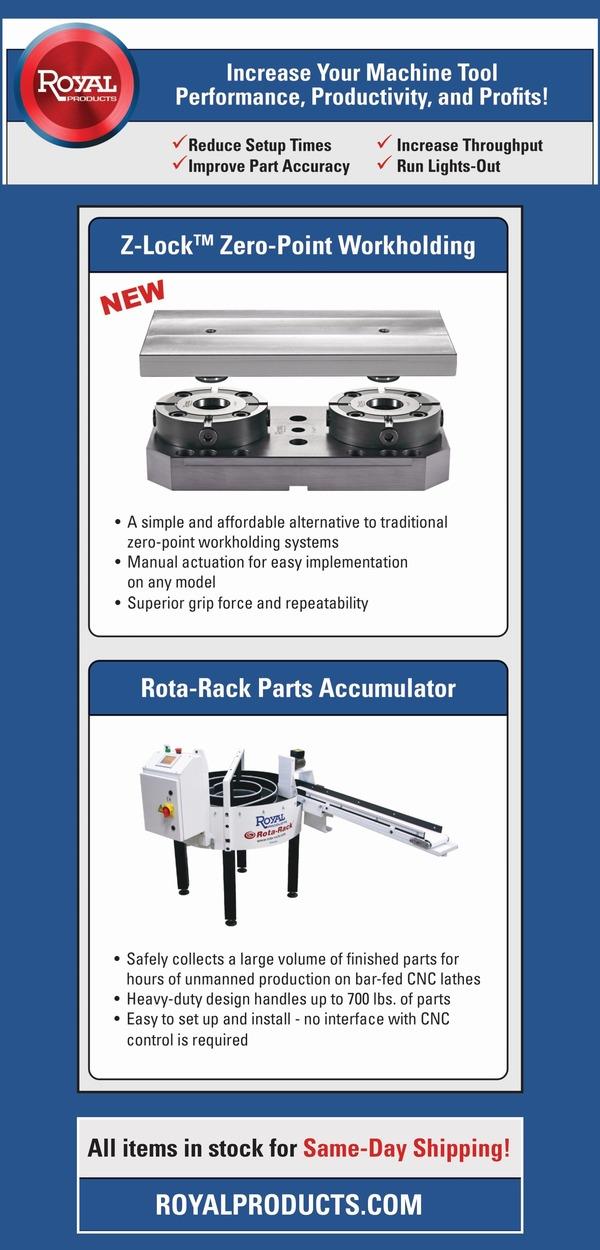
Lower Cost of Ownership with Standard Control Options
June 1, 2020
Mitsubishi Electric Automation has announced that it offers a variety of common options as standard on its M7 and M8 series controls in order to enhance machine tool performance and lower the total cost of ownership for customers.
According to Mitsubishi, some of the most common options that come standard on its controls include:
- High speed, high accuracy mode allows users to run complex, highly precise 3D mold work without experiencing a slowdown in machine performance or reduction in control processing.
- Tool Center Point Control, G43.4, profiles the workpiece surface and then adjusts the axes to keep smooth, constant contact with the surface by utilizing the control point and not the pivot point. This helps prevent gouges on the part, extends tool life and saves material.
- Super Smooth Surface control reduces machine vibration during high-speed cutting and optimizes acceleration/deceleration times for each axis. This allows for shorter cutting times with a high degree of accuracy.
- Inclined Surface Machining, G68.2, facilitates temporary coordinate system, allowing the operator to see G-code positions that are relative to a given point on the model without the need of creating a new work offset. This reduces the programming burden of turning 3-axis code into 5-axis code.
To help ease programming, Mitsubishi Electric Automation offers a couple of different types of conversational programming. Conventional Navi-Mill/Navi Lathe allows creation of complete machining programs from start to finish right from the operation panel. In addition, the new Interactive Cycle Insertion (ICI) is an icon-based programming method that lets the user choose from a variety of machining cycles and add them into a G-code program. Background editing allows operators to edit a program while another program runs. All of the changes made during background edit will not affect the running program or its subprograms, allowing users to prepare for future machining and saving on time.
As machine programs become more advanced they require more memory. Mitsubishi Electric Automation addresses this issue with two expansion slots for 32 GB SD cards, allowing for a total of 64 GB of additional memory. The additional memory allows operators to read, write, run and transfer programs via the SD card to the control without machine lag. Subprogram calls from the SD cards are available as well.
For more information contact:
Mitsubishi Electric Automation Inc.
500 Corporate Woods Pkwy.
Vernon Hills, IL 60061
847-478-2500
us.mitsubishielectric.com/fa/en
< back