
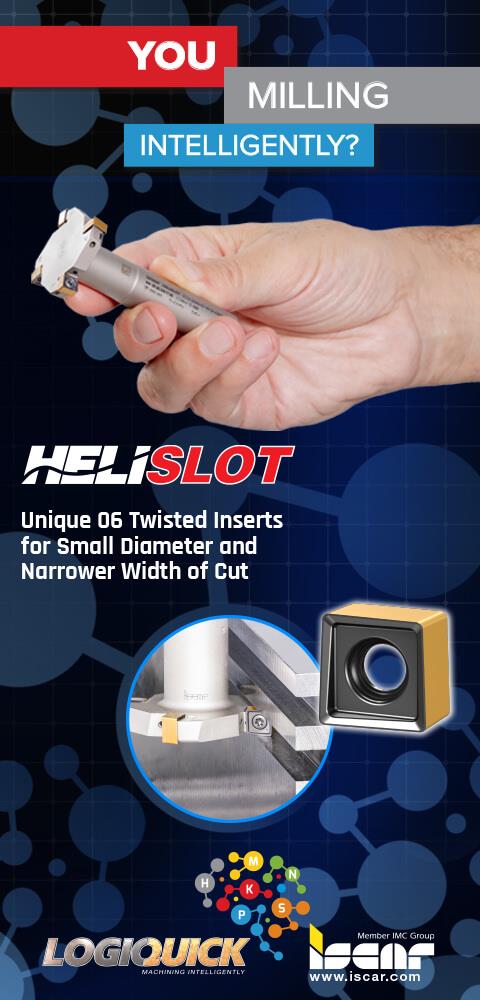
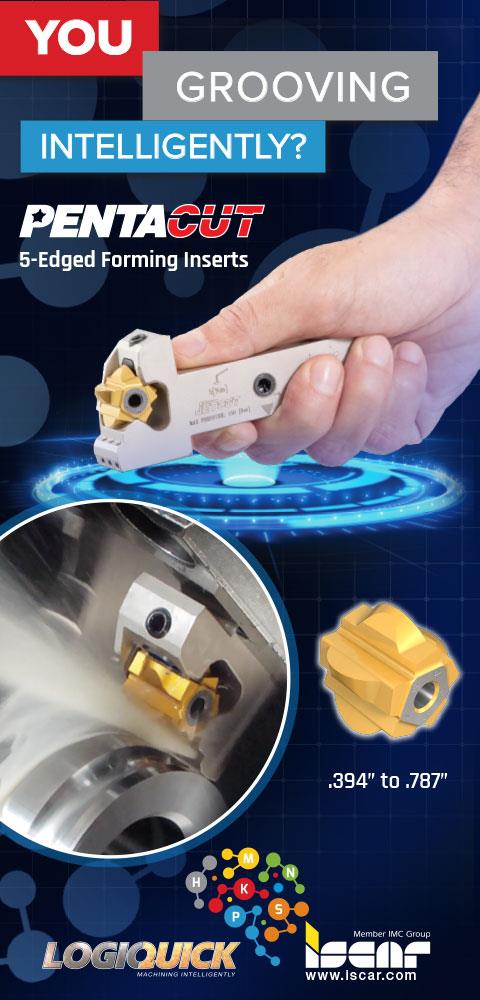
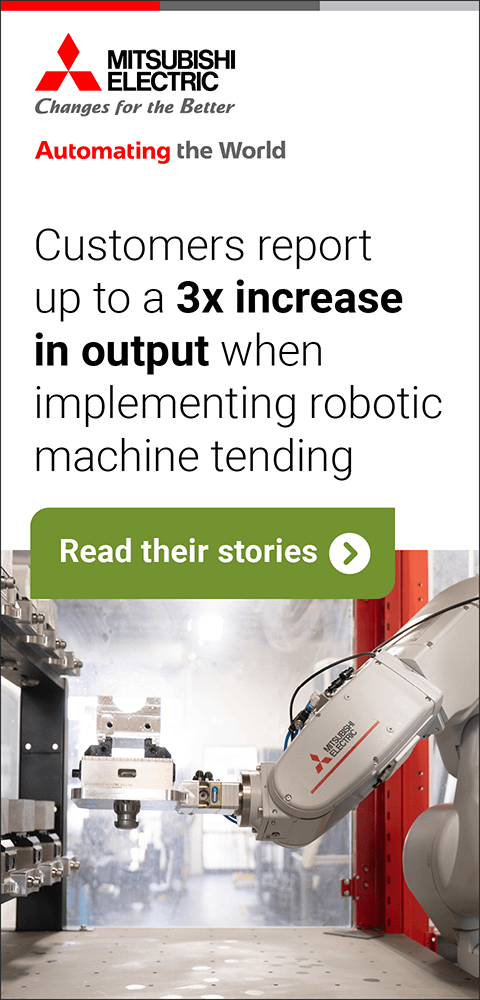
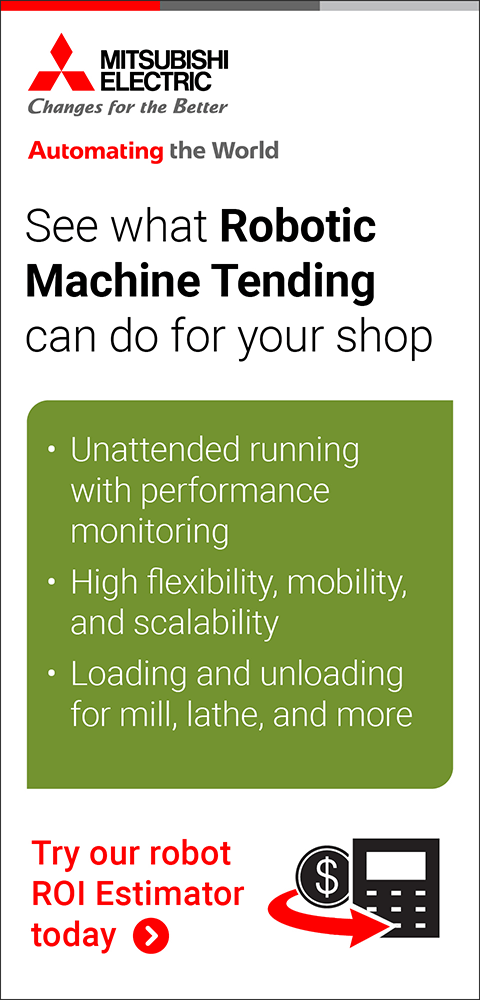
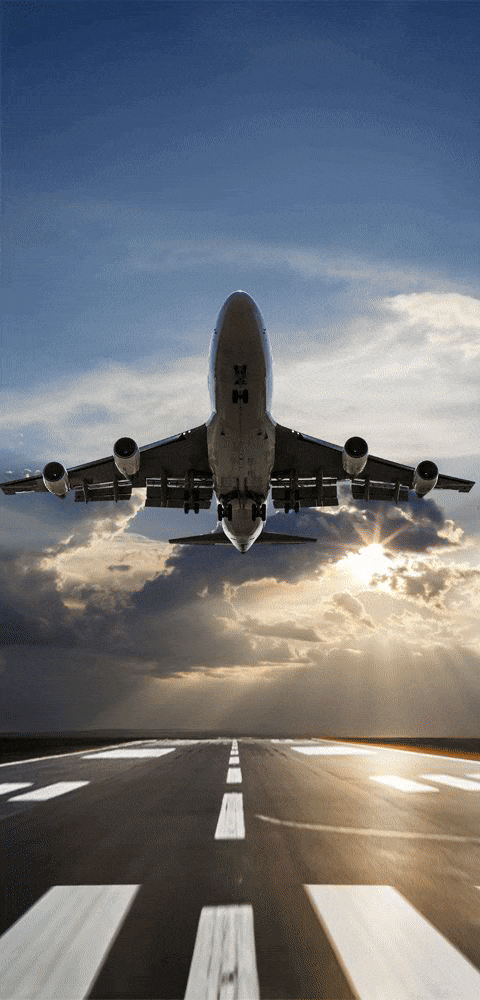
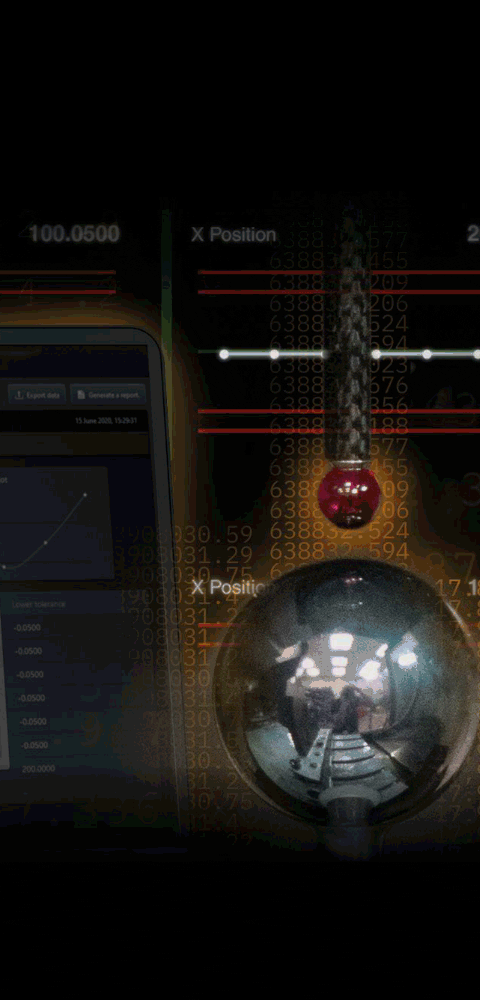
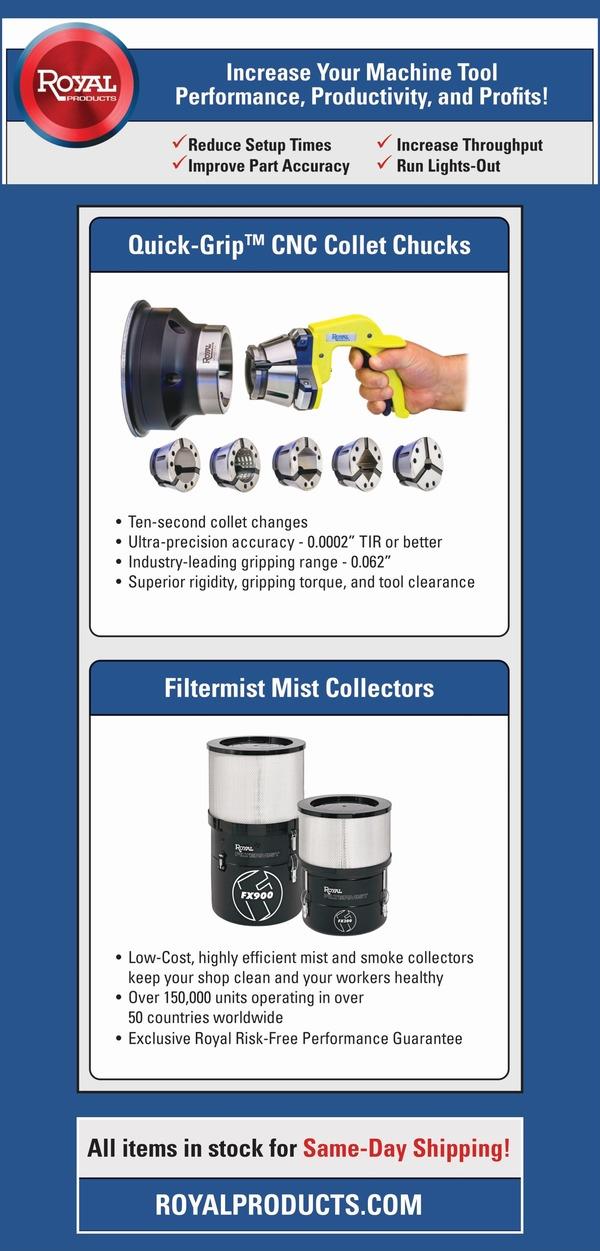
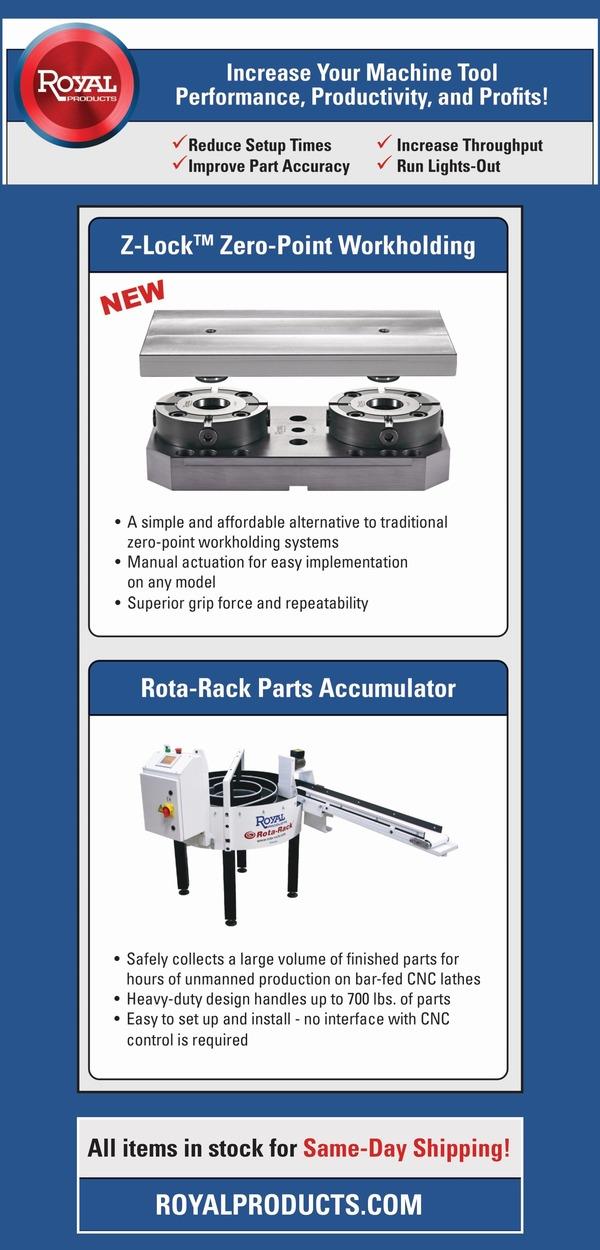

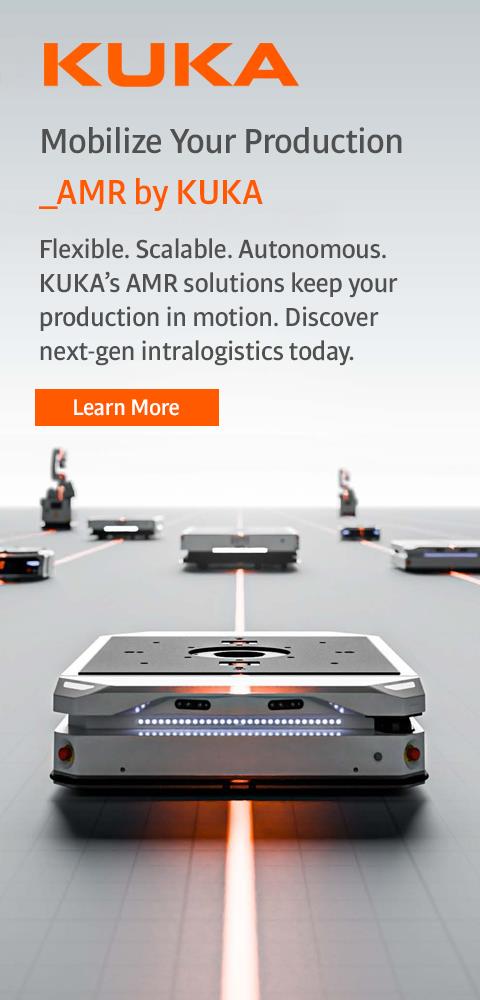
Solid Carbide Endmills for Titanium Alloys
June 1, 2020
In today's machining environment, titanium alloys have become a common material due to their strength to weight ratio and resistance to chemicals. "Ti alloys are now used in aerospace, medical, defense, firearms and automotive industry segments, and the needs for advanced cutting tools to machine these materials effectively have grown exponentially. Iscar has introduced a line of solid carbide endmills under the name Ti-Turbo to compete in this environment," said a company spokesperson.
Ti-Turbo is part of Iscar's high performance line of Chatter Free end mills. "The 4-flute endmill has the ability to perform 2xD full slotting and peripheral profiling and is also designed to excel in the environment of HEM/HSM," said the spokesperson. The tools come with a variety of corner radii and shank styles to fit most end user needs.
"Ti alloys have machining characteristics that impart heavy loads onto the cutting edge, and the ECKI end mills are specifically designed to take that abuse," said the spokesperson. With a low Young's modulus (Young's modulus is a mechanical property that measures the stiffness of a solid material), Ti alloys are always trying to evade/push away from the cutting edge and then snap back when it reaches its stretching point. "This movement can create chatter as well as introduce a work hardening effect on the material," said the spokesperson. "Usually with soft materials, a sharp and high positive cutting geometry is needed. This, however, creates a weak cutting edge. To combat these forces, the ECKI end mills have a very specific geometry designed to successfully overcome this situation."
According to Iscar, ECKI end mill features include:
- Variable pitch and variable helix help combat chatter by continually changing the cut frequency.
- Eccentric ground lands with unique chamfered cutting edges give the required edge strength to handle the snap back of the material into the cutting edge.
- Submicron grade with a PVD coating provides high thermal and chemical stability along with the necessary wear resistance.
"The unique cutting edge geometry described above has contributed to higher efficiencies and throughput for many shops," said the spokesperson. "Test results have shown a 33% average savings for the customers."
Due to requests for special built configurations in the U.S., Iscar's Texas-based manufacturing facility now has the capacity to grind up to 1.25" dia. ECKI specials, allowing the company to provide engineered solutions to meet most needs.
For more information contact:
ISCAR Metals, Inc.
300 Westway Place
Arlington, TX 76018
817-258-3200
info@iscarmetals.com
www.iscarmetals.com
< back