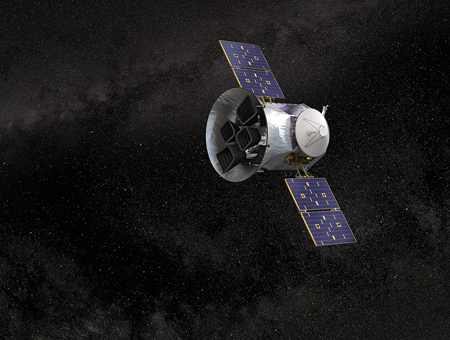
Artist concept of TESS Spacecraft. Image courtesy of NASA's Goddard Space Flight Center.
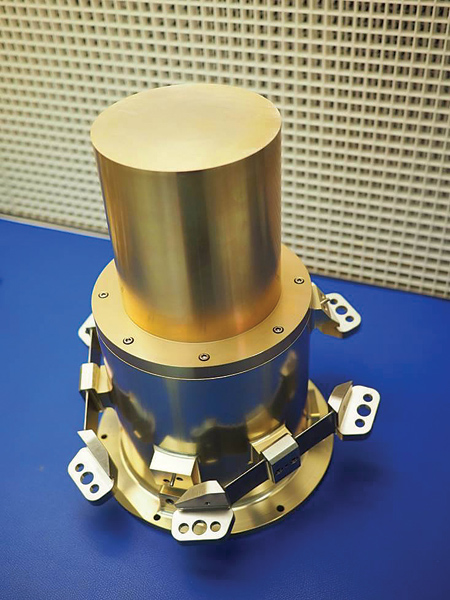
Mounting brackets on a camera-mount holder mock-up
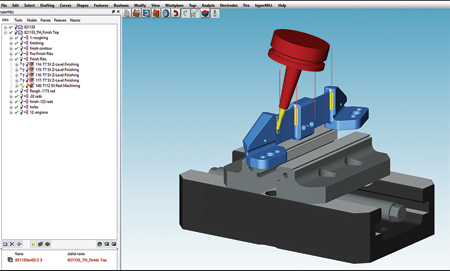
hyperMill generated 5-axis profile finish toolpath for camera-mount brackets
OPEN MIND Technologies, a developer of CAD/CAM software solutions, has announced that Ramco Machine (Rowley, MA) is helping to impact the future of space exploration by using hyperMILL CAM software and 5-axis machining to make parts for an advanced NASA satellite mission.
The mission, called Transiting Exoplanet Survey Satellite (TESS), is credited with discovering its first circumbinary planet-a world orbiting two stars. NASA's TESS goal is to explore and survey nearby bright stars in order to analyze planets, both smaller and larger than earth, as the planets circle their host stars and the earth orbits the sun. Read more at nasa.gov/feature/goddard/2020/nasa-s-tess-mission-uncovers-its-1st-world-with-two-stars.
Ramco was contracted by MIT Lincoln Laboratory in 2017 to fabricate the critical camera mount brackets for a NASA TESS satellite mission. In 2018, a solar powered in-space satellite equipped with four ultrasensitive cameras was launched aboard a two-stage SpaceX Falcon 9 rocket on its way beyond earth's solar system to outer space. The four-camera system developed at the MIT Lincoln Laboratory monitors the brightness of more than 200,000 stars and searches for minute drops in brightness as the planets transit in front of each star.
Making the mounting brackets required the machining of Invar, a nickel-iron alloy with a low thermal expansion coefficient, so it could meet the rigors of launch and enable it to compensate for the extreme temperature swings of outer space. The mounting bracket has very tight tolerances. The central rib's thickness is .050" +/- .001", perpendicularity between surfaces is held to .001" and the bracket's two opposing surfaces must be in-line with each other to within .001".
In order to cut Invar and achieve the required tolerances, Ramco used a hyperMILL-generated 5-axis profile finish toolpath. By doing this, an accurate finish across each part was achieved, keeping them within these very tight tolerances.
To read more about how Ramco is using hyperMILL CAM software for efficient 5-axis machining, visit openmind-tech.com/en-us/industries/models-prototypes/ramco.html.
For more information contact:
OPEN MIND Technologies USA, Inc.
1492 Highland Ave., Unit 3
Needham, MA 02492
888-516-1232
info.americas@openmind-tech.com
www.openmind-tech.com