
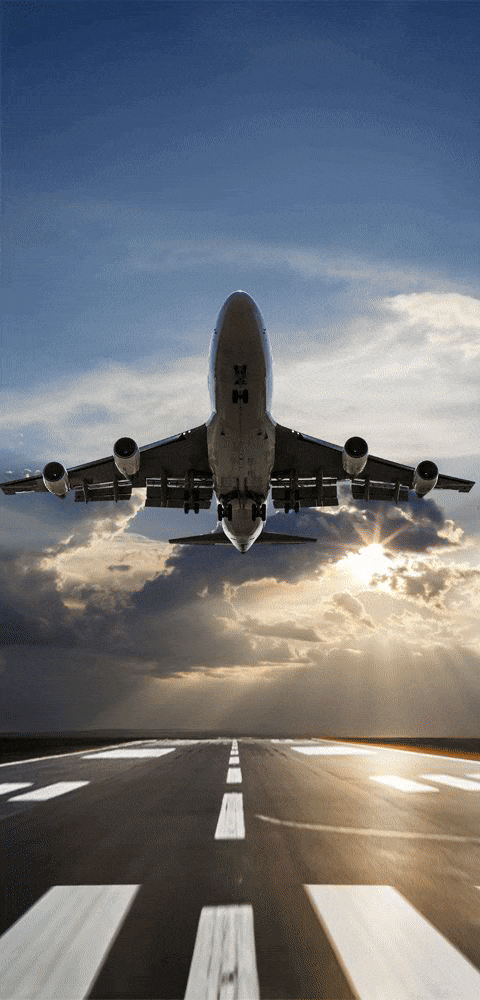
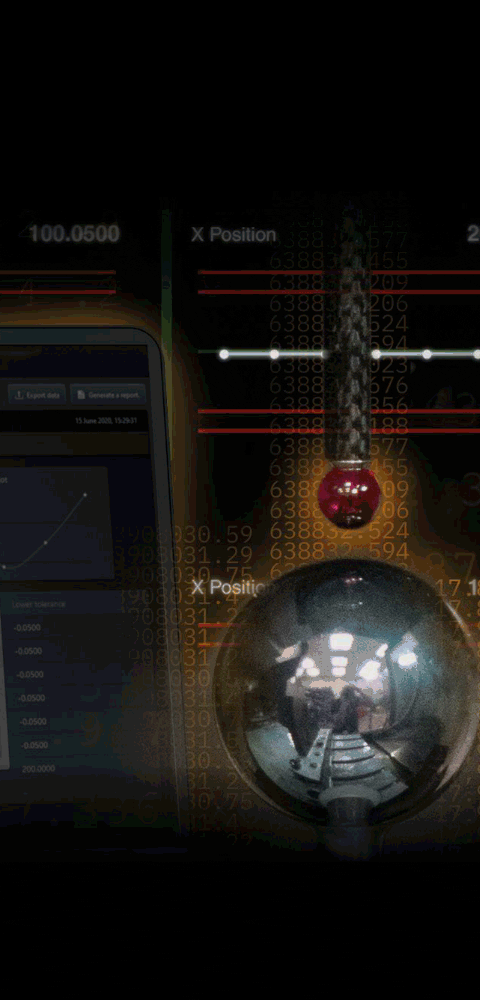
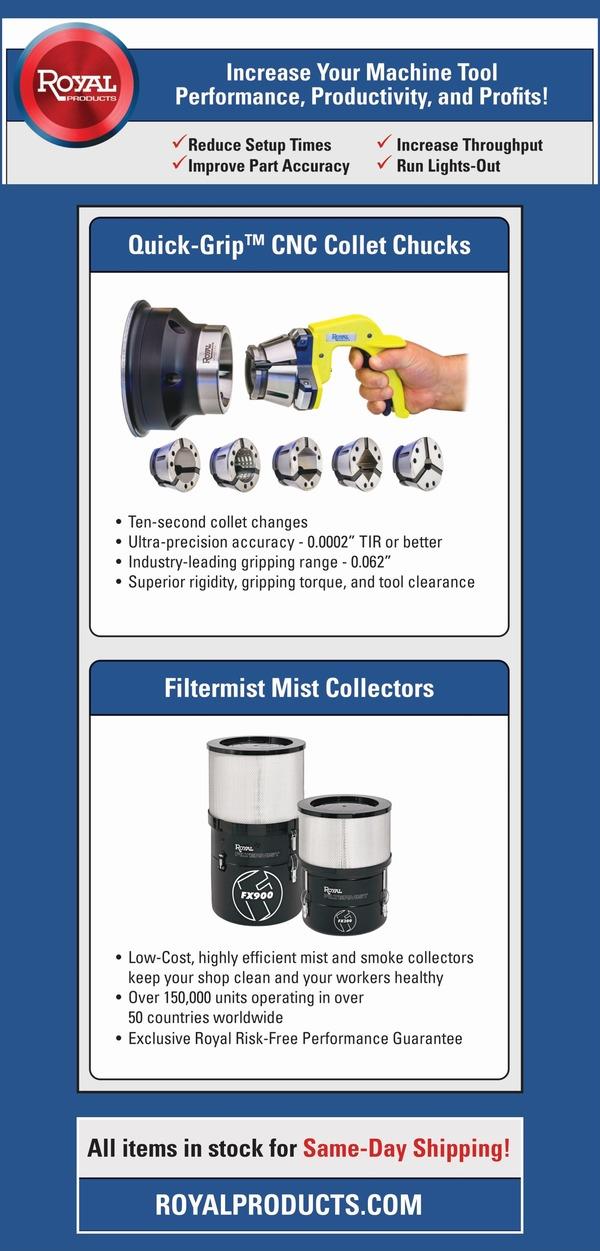
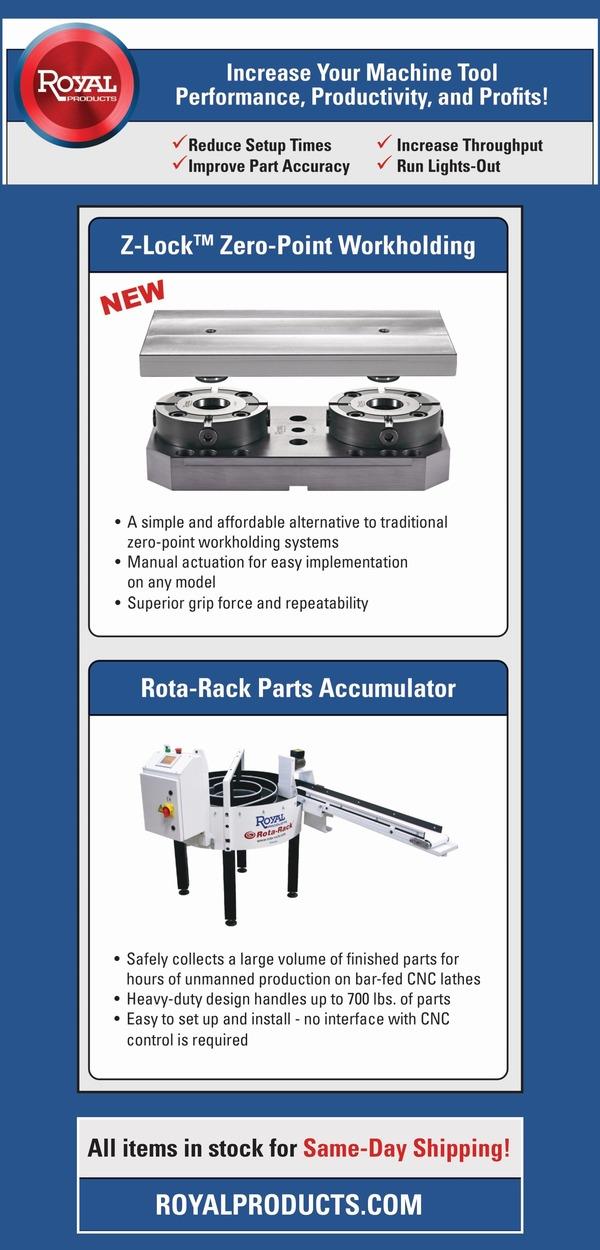

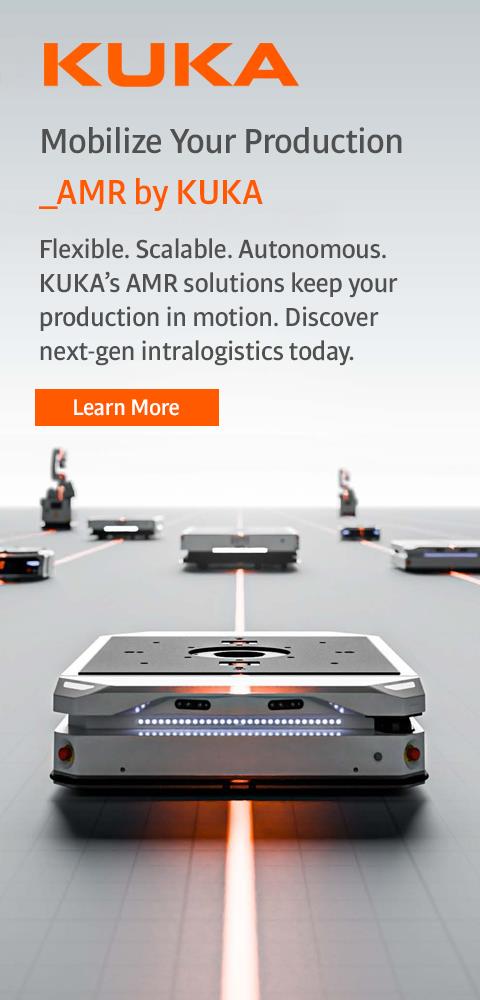
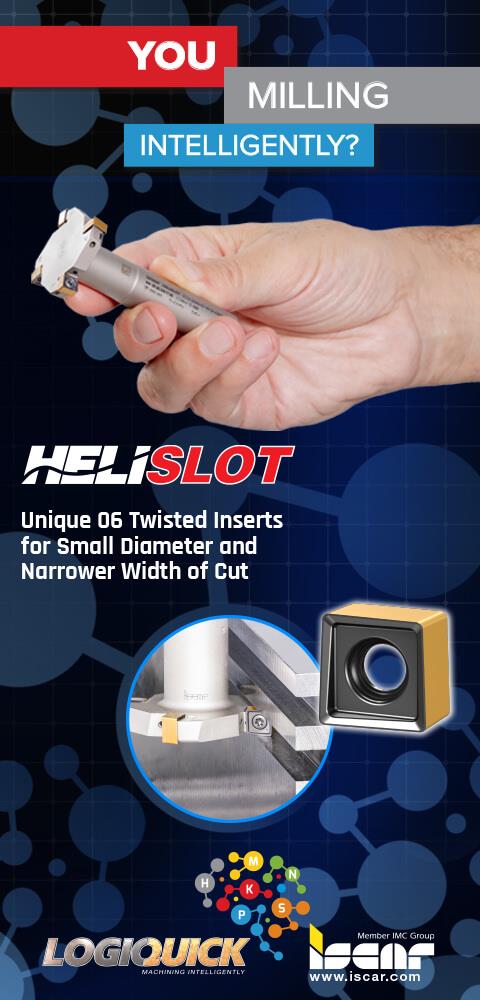
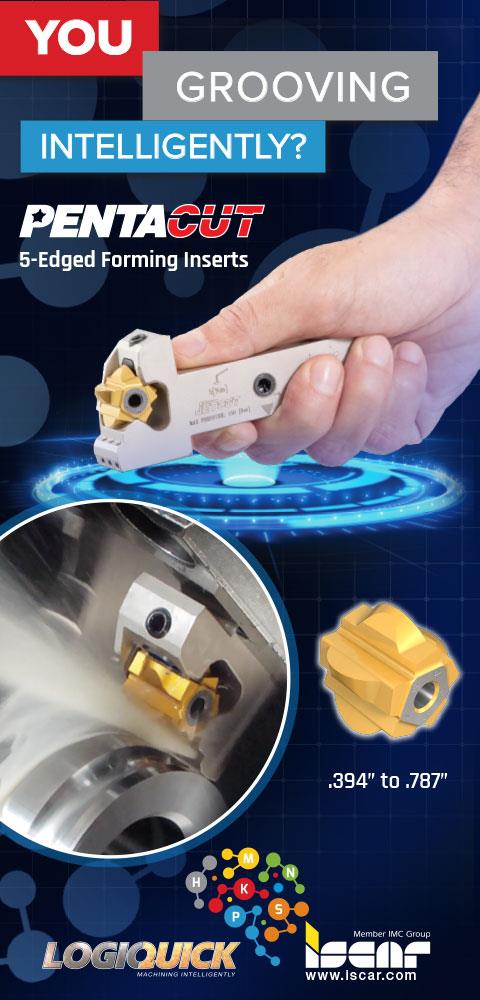
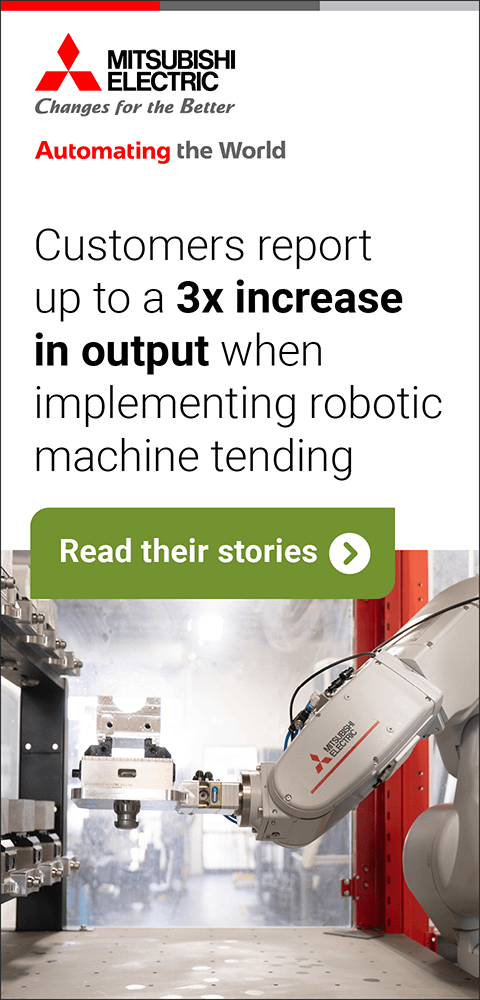
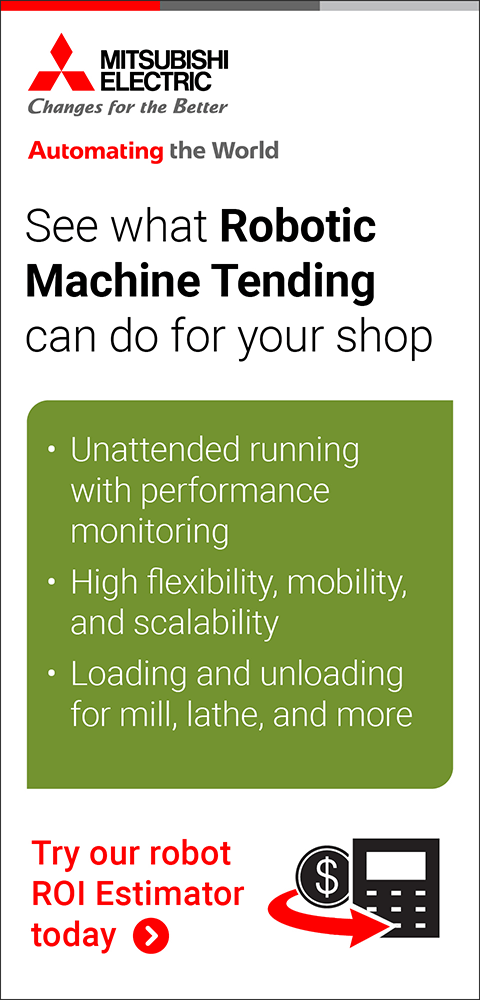
Tramp Oil Removal System Utilizes Stainless Steel Tanks
June 1, 2020
Keller Products, a Division of Plastic Design, Inc., has introduced an expanded offering of dedicated tramp oil removal systems utilizing a stainless steel tank design as an alternative to the traditional molded plastic tanks. "The new designs are priced vey competitively compared to other metal tank designs currently being offered," said a company spokesperson. "In addition, the new SST design can be magnetically mounted to the side of the machine tool, conserving valuable floor space around the machine tool."
There are three different models for maintaining metalworking fluids. Specifying a unit will depend primarily on the volume of the machine sump. All the units will employ a 1/2" air diaphragm pump as the primary fluid conveying component. The SST units will also use the patented Keller oil separation technology. The compact design of the SST units makes the systems capable of being shipped via UPS.
A version of the stainless systems will also be available for removing free oil from aqueous cleaning systems. "A frequent problem encountered in parts wash lines is the buildup of an oil layer on the surface of the rinse tank," said the spokesperson. "When the rinsed parts are raised out of the tank, the oil layer re-contaminates the parts. The problem can be solved by continuously removing the oil layer from the surface of the rinse tank. In principle, removing oil from the surface of the rinse tank is similar to separating tramp oil from the surface of coolant in machine tool sumps, an application for which Keller Products has supplied several thousand units."
A self-priming air-operated diaphragm pump on the Keller units pulls the oily layer from the surface of the tank through an inlet device and then through a filter to remove any floating solids. The filtered oil/water mixture is then pumped through the patented Keller separator element immersed in the separator tank. The oil-free water returns continuously back to the reservoir tank at a high flow rate, up to 180 gallons per hour.
The free oil layer that is removed collects on the top of the Keller separator tank and is occasionally drained into a waste oil container by opening the oil drain valve. No other operator attention is required.
For more information contact:
Jonathan Strauss, Sales Manager
Keller Products
A Division of Plastic Design, Inc.
180 Middlesex Street
N. Chelmsford, MA 01863
800-352-8422 / 978-264-1911
info@kellerfilters.com
www.kellerfilters.com
< back