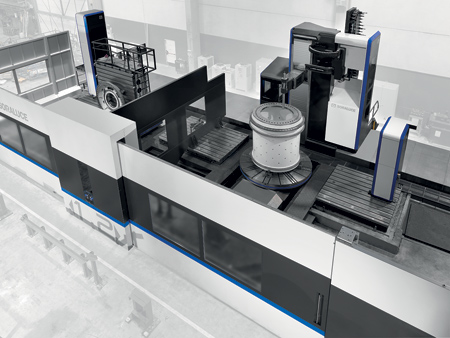
SORALUCE FS 16000 multitasking machine for milling and turning large workpieces
Multitasking solutions from Soraluce offer a wide range of machining operations, such as milling, turning, grinding and gear cutting, all integrated into a single machine, making it possible to reduce cycle times, reduce costs and increase the efficiency of machining processes.
"The SORALUCE FS 16000 multitasking machine is a modular and versatile solution engineered for large, complex workpieces that require the highest precision," said a company spokesperson. "A wide range of options and accessories are available to choose from, offering a high degree of flexibility oriented towards optimal productivity and maximizing profitability."
The FS 16000 offers a generous work capacity, with longitudinal travel of 630", vertical travel of 142" and cross travel of 159", making it suitable for machining large, complex workpieces in a single set-up.
The machine incorporates two independent workstations, each including a Soraluce designed and manufactured table-one for milling operations with a traveling rotary table of 118" x 98" plus 78" W-axis, the second for milling and turning operations with a traveling rotary turning table of O118" plus 78" W-axis. Both tables offer load capacity of up to 88,180 lbs. each.
The traveling column design of the Soraluce floor type series allows for pendulum machining, where parts can be unloaded and loaded in one workstation while the spindle remains engaged in the other workstation, enabling non-stop machining.
Equipped with a high torque Soraluce designed and manufactured universal multitasking head capable of 50 HP (37 kW), the stepless head design provides indexing at 0.001° x 0.001° and spindle speeds up to 5,000 RPM. The multitasking head integrates a rotational locking system that includes a clutch to clamp the spindle at any angle during turning operations. This clamping system prevents bearing damage due to an internal retractable support ring. With this design, it is possible to define head and spindle orientation at any angle, thus avoiding interferences with the workpiece and optimizing machining capability. Milling and turning tools are directly loaded into the spindle using the ATC without the need for any intermediate elements.
The FS 16000 also includes a fixed horizontal Soraluce H62 head of O8" and 19" length along with a Soraluce TH02 head for internal turning operations for long boring bars from O4" to O10" and up to 100" in length. All milling, multitasking and turning heads incorporate the Soraluce head changing system, which allows accurate changing of heads through adapter flanges. The automatic tool changer system has storage capacity for 80 tools and can change tools in both the vertical or horizontal position.
The multitasking solution incorporates specific cycles developed by Soraluce to ease turning functionalities, such as the possibility to manage both milling and turning cycles at the same time, switching from milling to turning mode automatically or easily programmable turning cycles.
"High productivity and precision are achieved in the machining of large components due to the stability and rigidity of the FS 16000 design," said the spokesperson. "The machine, with optimal power and speed, provides superior machining results due to its dynamic transmission system combined with its heavy duty guides and dampening system."
The FS 16000 includes full guarding with automatic doors at each workstation that offers complete accessibility to the working area from the front and from above, and also contains chips and coolant during the machining process. In order to provide the operator with improved visibility, the guarding has large windows that offer ease of operation, safety and cleaning.
"What has been described above is just one configuration of a Soraluce FS 16000, which can be completely customized for unique applications," said the spokesperson. Configuration options include shorter or longer X-axis travel, shorter or taller vertical travel, smaller or larger rotary milling or turning tables, addition of fixed floor plates, higher spindle RPM, additional heads (including some with 5-axis capability), larger ATC capacity, etc.
For more information contact:
Doug Schulte
Business Development Manager
Select Machining Technologies
910 Day Hill Road
Windsor, CT 06095
860-687-3475
dschulte@selectmachiningtech.com
www.selectmachiningtech.com
SOUTHWEST
AR
Keith Wilson
Morris South
kwilson@morrissouth.com
OK, TX, LA
Scott Wyatt
Hartwig, Inc.
scott.wyatt@hartwiginc.com
SOUTHEAST
VA, NC, SC, GA, TN, AL, MS
Keith Wilson
Morris South
kwilson@morrissouth.com
FL
Randy Ditch
Gosiger East Coast Region
randy.ditch@gosiger.com
NORTHEAST
ME, CT, NH, VT, MA, RI, E. NY, N. NJ
Todd Campbell
Robert E. Morris Co.
tcampbell@robertemorris.com
W. NY, W. PA, WV
Greg Giglio
Morris Great Lakes
ggiglio@morrisgreatlakes.com
E. PA, S. NJ, MD, DE
Randy Ditch
Gosiger East Coast Region
randy.ditch@gosiger.com
MIDWEST
N. IL, WI, MN, ND, SD
Corey Johnson
Morris Mid-West
cbjohnson@morrismidwest.com
MO, S. IL, IA, NE, KS
Scott Wyatt
Hartwig, Inc.
scott.wyatt@hartwiginc.com
OH, KY, IN
Jeff Murray
Gosiger Mid-West Region
jeff.murray@gosiger.com
MI, N. OH
Todd Turk
Gosiger Great Lakes Region
todd.turk@gosiger.com
WEST
CA, NV, OR, WA
Brad Gecowets
Gosiger West Coast Region
brad.gecowets@gosiger.com
AZ, NV (Clark City)
Greg Whelan
Arizona CNC
gwhelan@arizonacnc.com