
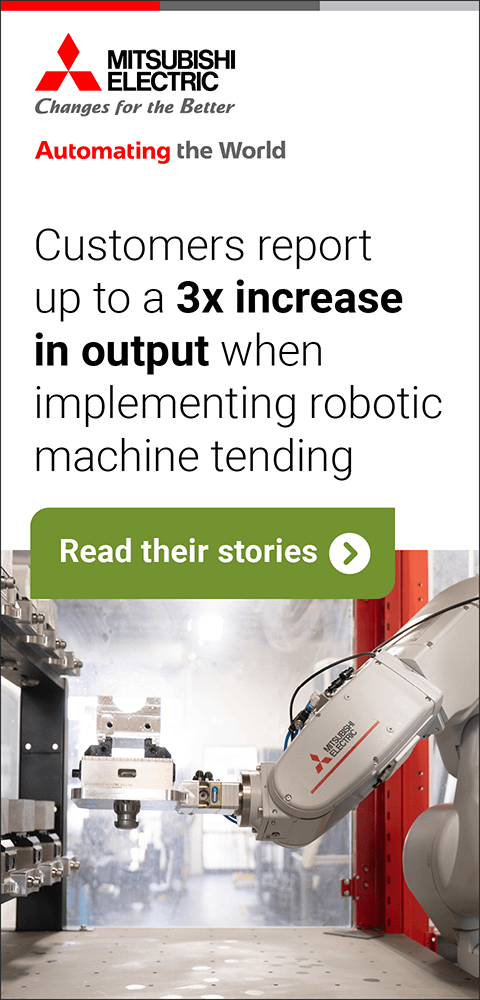
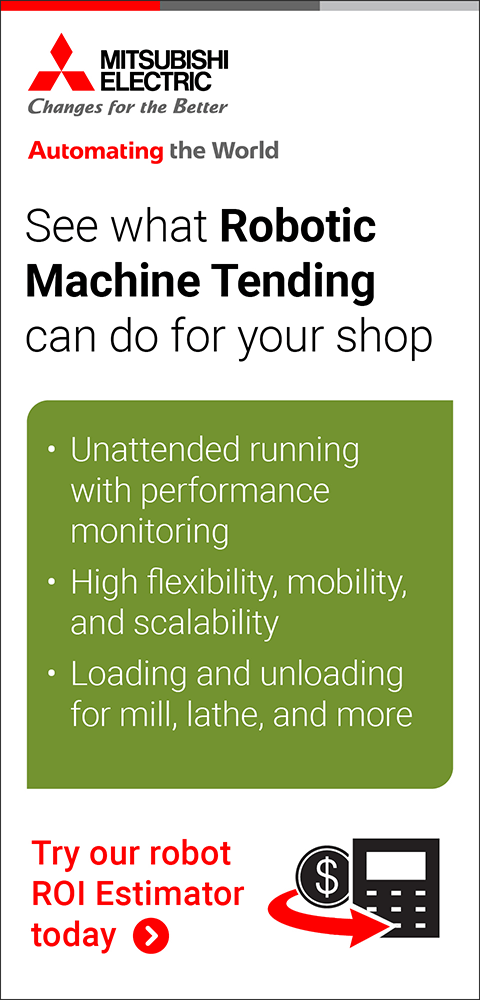
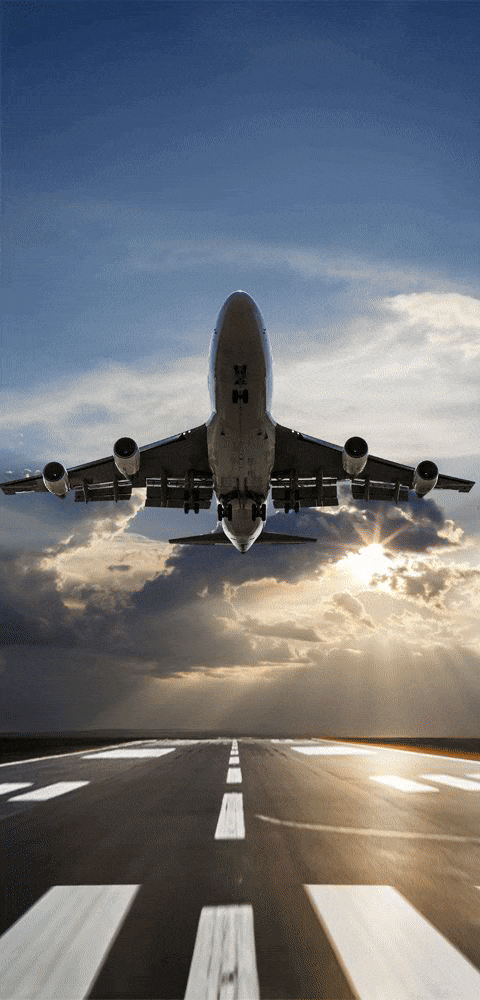
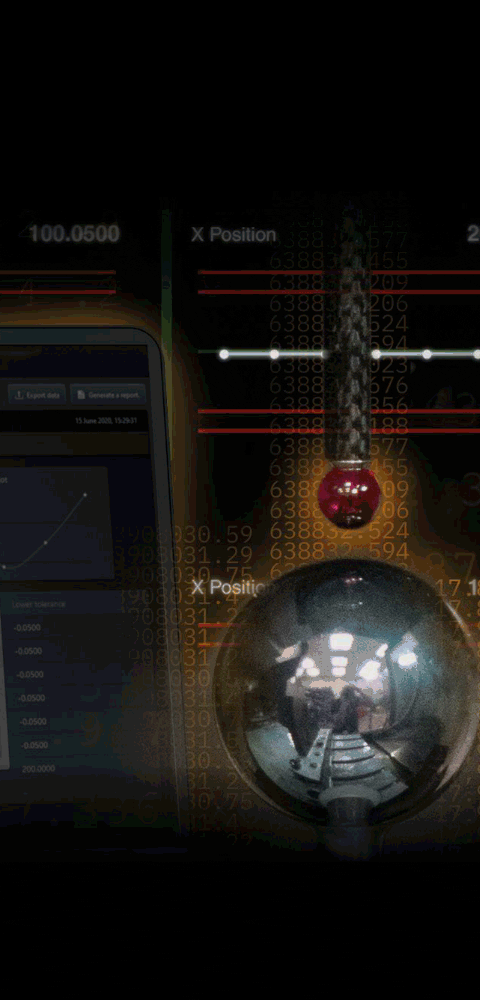
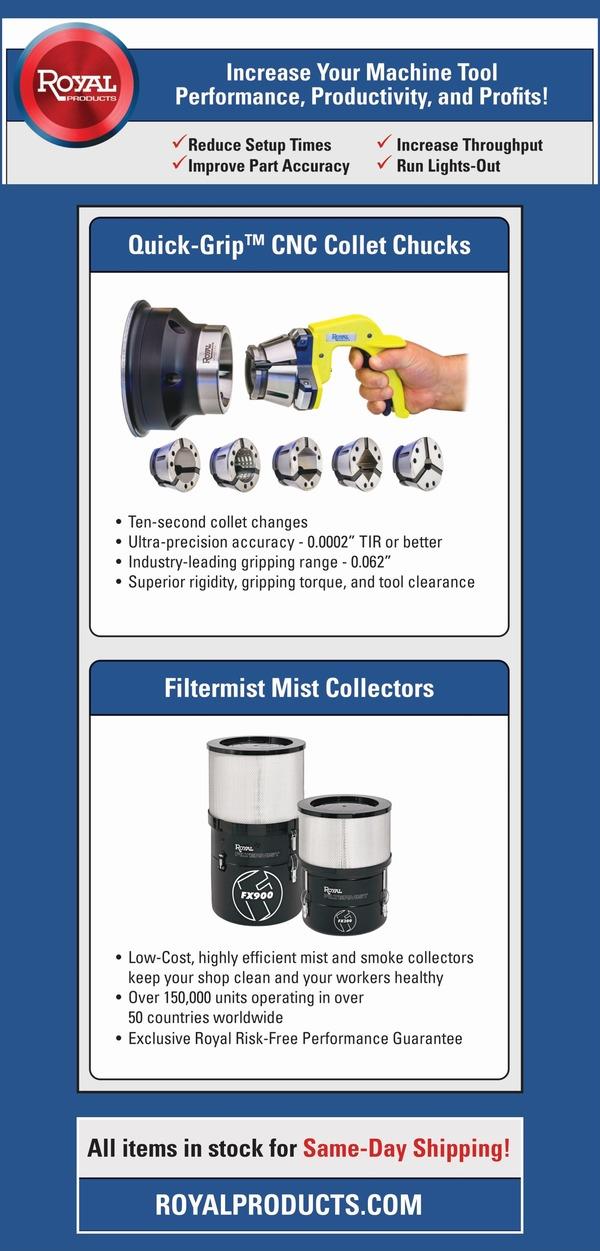
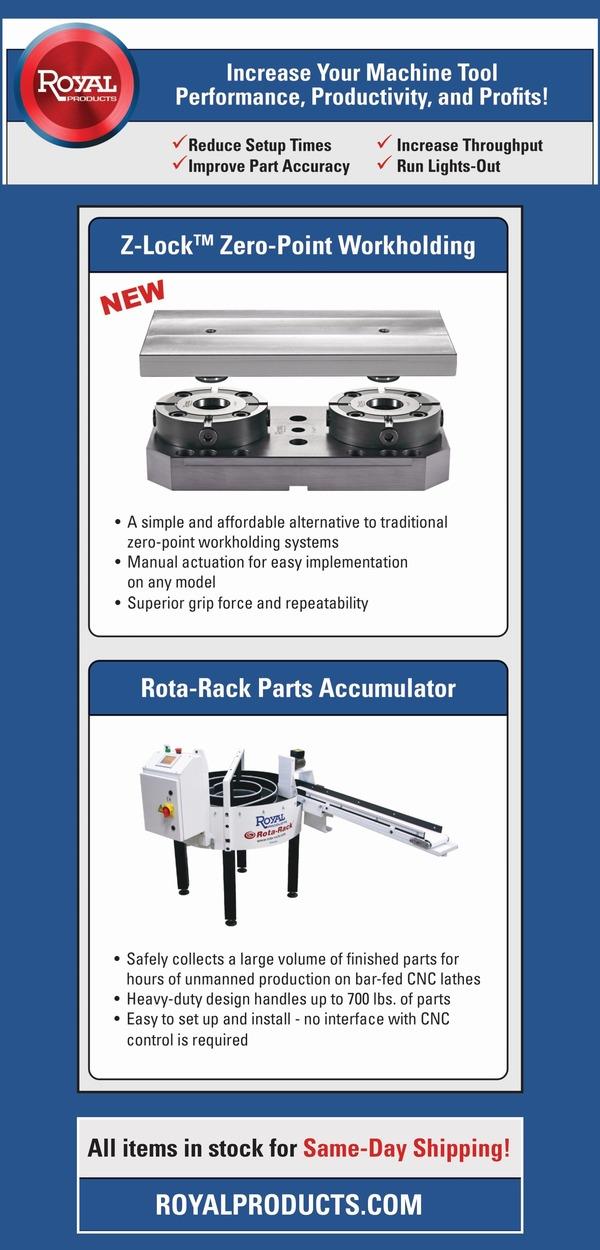

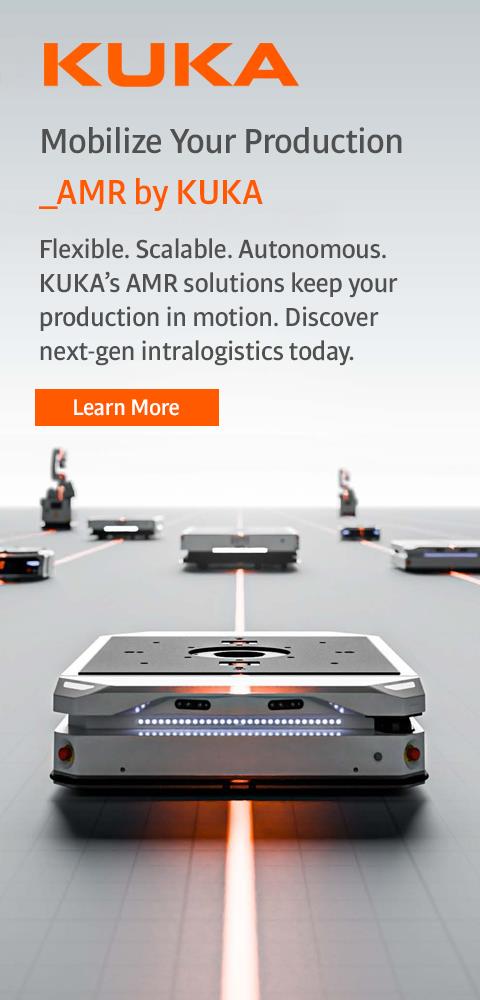
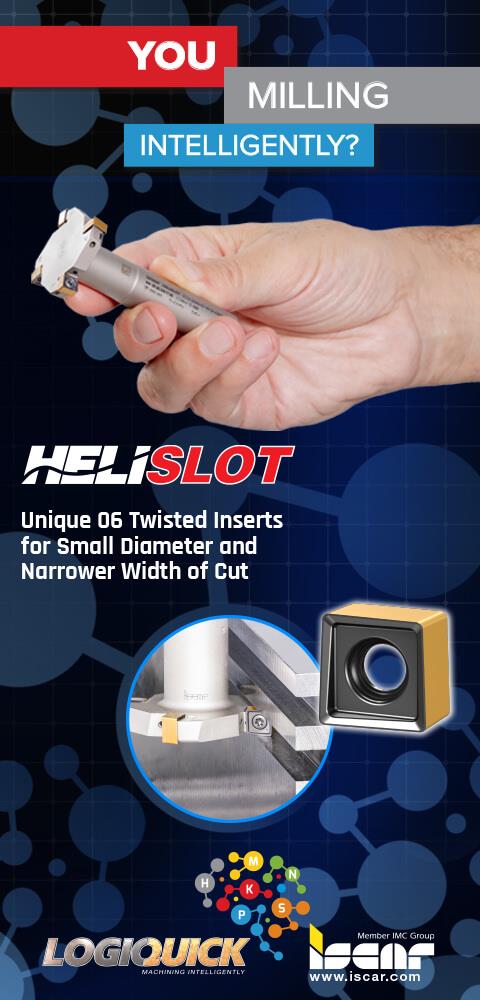
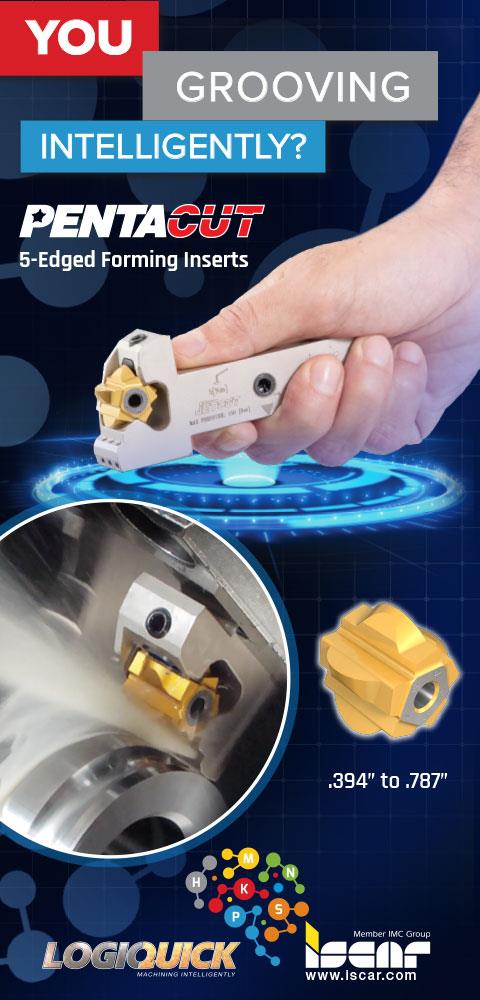
Direct Clamping for Small Diameters on the Micro Scale
July 1, 2016
MAPAL has expanded its program of narrow contour HTC clamping chucks. Through the use of additive manufacturing (AM), the narrow shapes are produced without a restrictive brazed joint. These chucks can directly clamp diameters of 3, 4 and 5 mm, now also allowing hydraulic clamping chucks to be used on the micro-scale, for example in medical technology or the timepiece and jewelry industries.
"Until now, reduction sleeves were usually required to clamp diameters below 6 mm; with the new chuck, these are no longer needed," said a company spokesperson. "Moreover, the advantages of combining hydraulic clamping technology with the contour of a narrow shrink chuck can now also be enjoyed on the micro-scale." Like its counterpart for diameters above 6 mm, the new HTC is made using AM. The reason: as of yet, it has not been possible to produce either the narrow contour or diameters ≤ 6 mm for direct-clamping hydraulic clamping chucks using conventional manufacturing methods.
The clamping area is very close to the front of the chuck. This provides a concentricity of < 3 µm at the locating bore and < 5 µm at 2.5 x diameter, plus high geometrical accuracy along with vibration damping. The damping built into the system helps reduce micro-outbreaks at the cutting edge, giving the tool a longer life expectancy and reducing wear on the machine spindle.
The HTC with a narrow contour offers all the advantages of the MAPAL HTC (High Torque Chuck) technology, with the "T" standing not only for "torque" but also for "temperature-resistance." The wide operating temperature range of up to 170 °C helps ensure additional process reliability. The balancing quality is G = 2.5 at a turning speed of 25,000 RPM. The chuck is designed for machining in contour-critical areas. It allows the tool to be clamped easily and quickly. "In other words, no training courses are required on its implementation, and no high set-up costs or expensive peripheral devices are needed," said the spokesperson.
For more information contact:
MAPAL Inc.
4032 Dove Road
Port Huron, MI 48060
810-364-8020
info@us.mapal.com
www.mapal.com
< back