

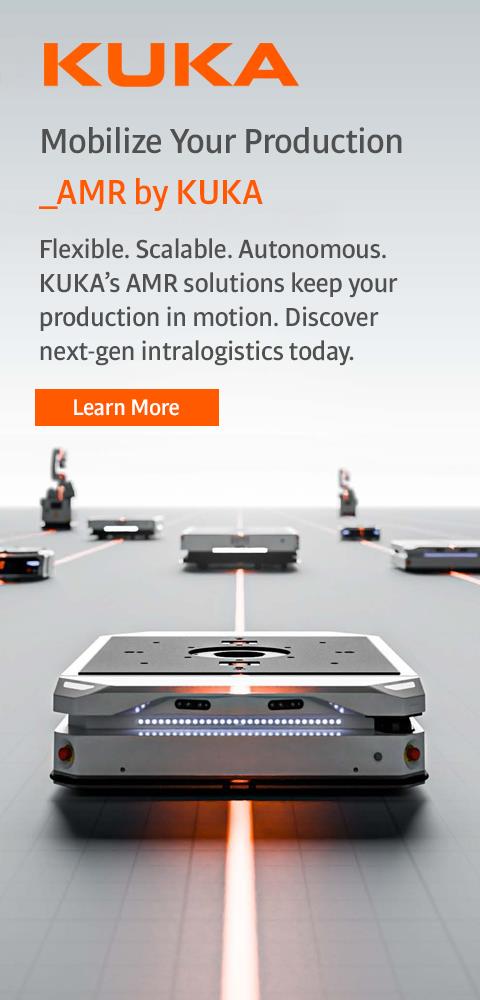
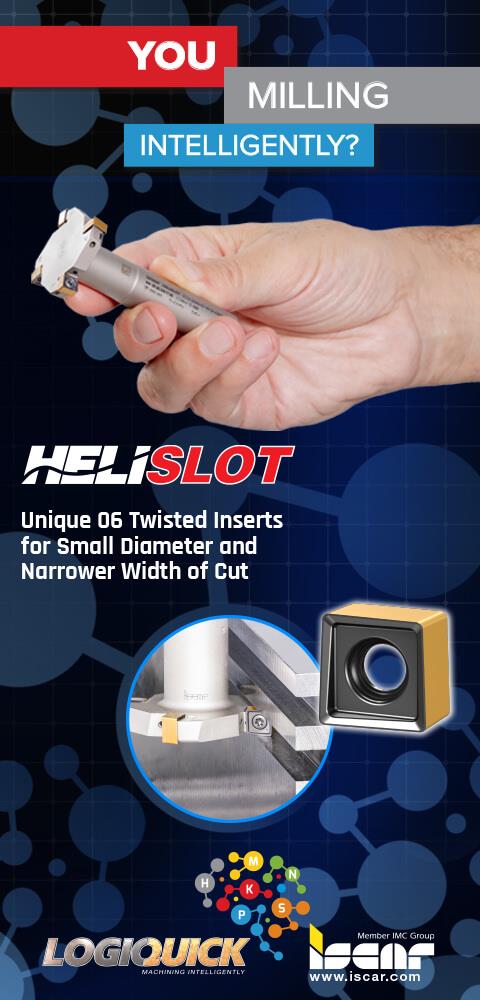
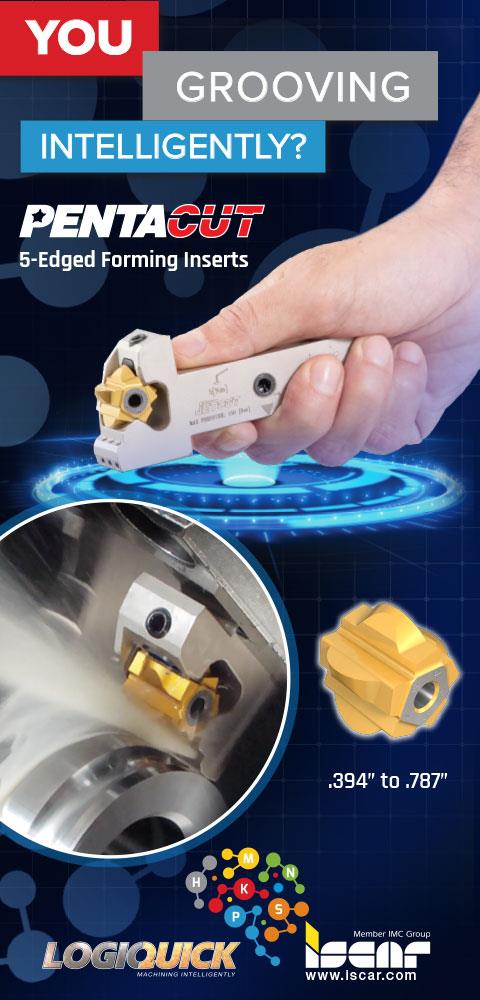
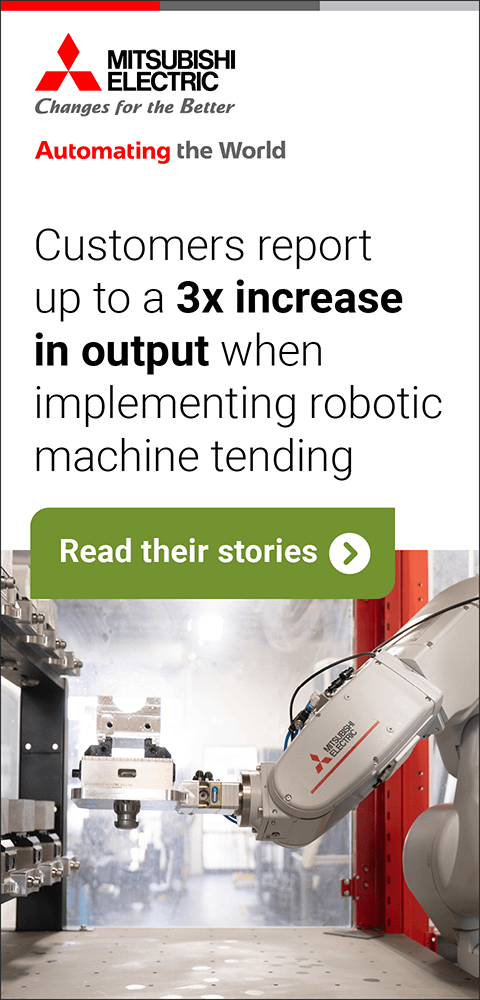
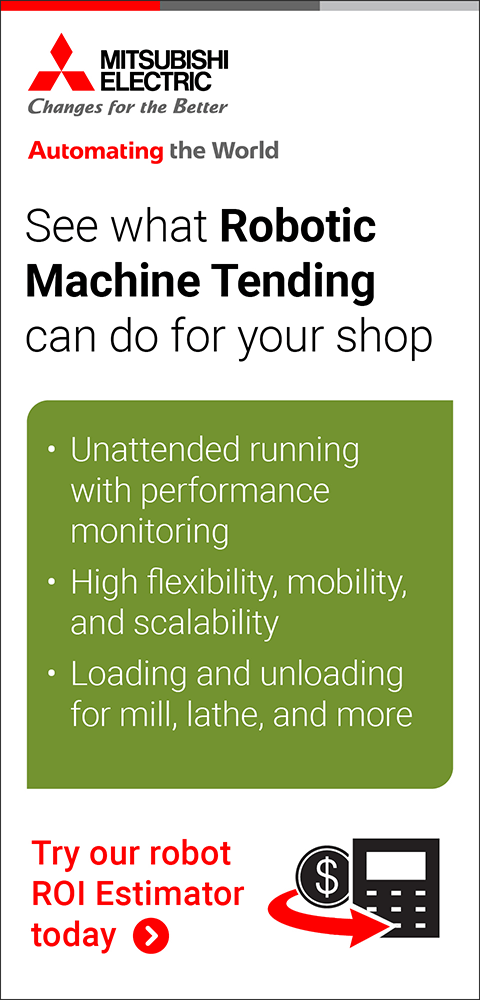
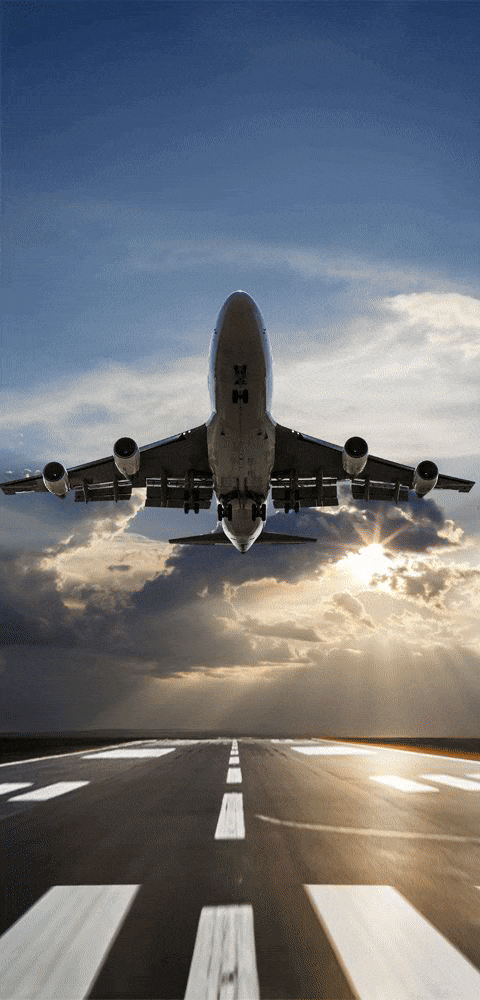
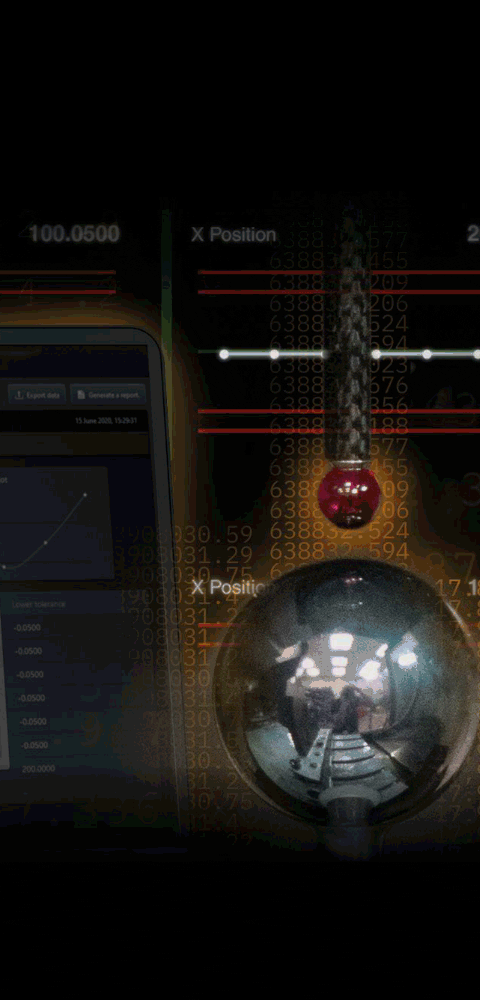
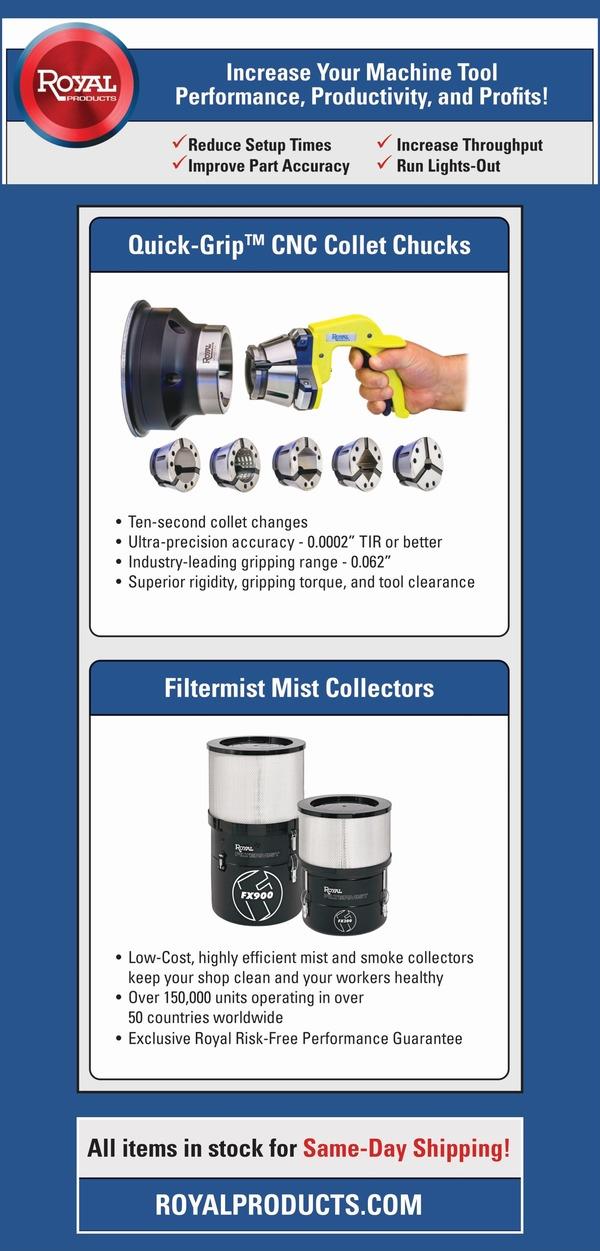
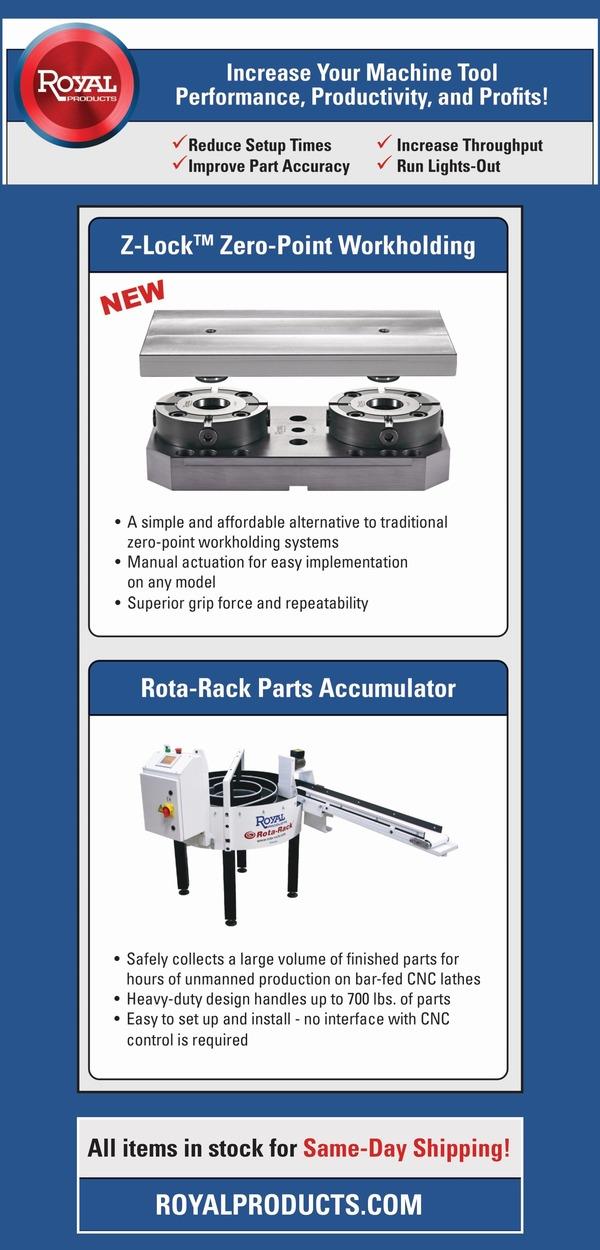
Wire and Sinker EDM Lines Expanded
July 1, 2016
A new addition to the wire and sinker lines of ONA EDM Machines is the QX4C Electrical Discharge Machine. For use in industries that need very fine surface finishing (VD1=0), the product consists of the machine tool, the microfine generator, the dielectric filtration system and the CNC control unit. Also standard on the machines are a fire-warning device, pendant controller, lamp and flushing nozzles.
Optional equipment includes both a five-position, 20- and 40-position automatic tool changer and pressurized glass scales that incorporate an internal air flow system to prevent the entry of dust particles. This helps maintain the scales for a longer period of time and leads to more precise work. Additional filtration and generator options are also available as is security pack software for both the normal and advanced user and plant monitor software for remote control. Both 1- and 2-axes rotary tables and rotating spindles can be added to the base unit with in the field installation.
The QX4C Series was produced with Digital Sinker EDM process technology to increase machine productivity for both existing and new applications. The generator works with advanced materials such as titanium-based alloys, ceramic hard metals, moldmax and others. This system can decrease electrode wear and can be used for high aspect ratio cavities in aero-energy materials and the mold industry.
"Application oriented and flexible, the All-Digital T-Rex Generator allows for quick technical development for specialized applications. The T-Rex Generator was designed with the Aero/Energy and Medical markets in mind," said a company spokesperson.
"When comparing the QX4C machines to the NX product line, there are a number of benefits to the user," continued the spokesperson. "Improved applications include: Ribs where productivity is increased from 23% to 50% over past technologies, with reduction in electrode wear to 500%, depending on the application. Productivity in finish machining increases productivity up to 60%, with improved surface finishing. Micromachining increases productivity for roughing to 30% and finishing to 50%. For close corners the minimum radius is in the inner circle is 5 µm, compared to 15 µm in the NX series."
Southwest
For more information contact:
Mark Emerson, President
ONA EDM USA, Inc.
15943 Angelo Dr.
Macomb, MI 48042
586-697-5880
memerson@onaedmusa.com
www.onaedmusa.com
Southeast
Terrill Sizemore
Regional Sales Manager
ONA EDM USA, Inc.
15943 Angelo Dr.
Macomb, MI 48042
937-307-3276
tsizemore@onaedmusa.com
www.onaedmusa.com
Northeast
Terrill Sizemore
Regional Sales Manager
ONA EDM USA, Inc.
15943 Angelo Dr.
Macomb, MI 48042
937-307-3276
tsizemore@onaedmusa.com
www.onaedmusa.com
Midwest
Terrill Sizemore
Regional Sales Manager
ONA EDM USA, Inc.
15943 Angelo Dr.
Macomb, MI 48042
937-307-3276
tsizemore@onaedmusa.com
www.onaedmusa.com
West
Mark Emerson, President
ONA EDM USA, Inc.
15943 Angelo Dr.
Macomb, MI 48042
586-697-5880
memerson@onaedmusa.com
www.onaedmusa.com
< back