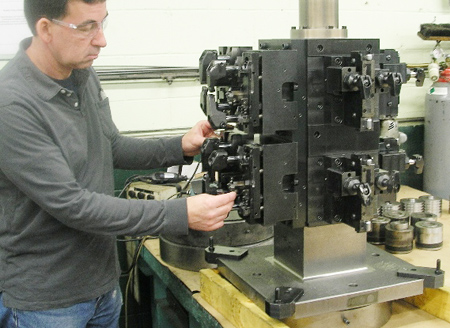
Albert Tessman, Royal Machine & Tool Design Engineer, checking clamping locator mechanisms on hydraulic fixture with robotic load/unload
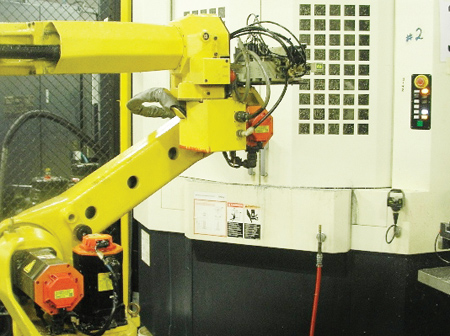
One of two horizontal machining centers with a single robot for load/unload of parts
"Today automation is taking a key role on the manufacturing floor to improve quality, production, and to stay competitive in obtaining contracts," said a company spokesperson.
Automation, whether a robot, gantry, or pick and place load device, helps provide consistency in the load/unload operation. It can operate continuously, thus reducing downtime and allowing management to concentrate on key areas of production.
"Many people have felt threatened by automation in the sense that it would be replacing them. However, automation has kept us competitive with other countries who have lower labor costs," said the spokesperson. "Plus, it has also created new and safer career jobs, making manufacturing an appealing career.
"However, in many instances companies take the wrong approach and jump into the automation trend with little thought of all the aspects of integration with the machine, tooling and fixturing. To avoid this, it is better to consider visiting companies that have taken the path to automation and learn what obstacles they have had or mistakes they have made and then learn their solutions."
Many prefer to go to the machine builder or dealer who has the personnel to provide a turnkey proposal. Since communication must pass through the machine control, it is recommended that machine personnel lead the project and do the integration.
In the planning stages first define what are the end results to be accomplished, and will they assist in the future in assuring a successful installation? Then consideration must be given to the following:
1. The machine and tooling parameters
2. The best way to hold the part and allow room for the automation device to pick and place the part without any obstructions
3. Allow for any machine or automation repairs that may occur to eliminate technicians having to dismantle the system each time servicing the system is required
4. Allow sufficient workholding clearance for the automation to load/unload the part plus, provide sufficient chip evacuation and insure that required safety measures are in place.
In addition, through the machine control the workholding device has to communicate with the machine as well as the automation regarding such actions as:
- Clamp/unclamp confirmation
- Clamp pressure monitor
- Part seat confirmation
- Spindle on/off.
These actions allow or disallow certain actions of the machine and automation.
"Not doing a thorough sequence of events, including all the options and possibilities, could possibly lead to a poor installation," said the spokesperson.
Certain actions are a must, such as:
- Stopping the spindle before unclamping the part
- Unclamping the part before the automation loads/unloads the part
- Cleaning of any chips from the fixture clamping and locating surface
- Preventing human intervention of the area while in operation.
Depending on the extent of the operation, there could be other factors that need to be taken into consideration. It is recommended to contact other companies who have had automation installed to provide insight on various areas of installation concern.
Authored by Royal Machine & Tool Corp.
For more information contact:
Bernie McAloon, Sales Manager
Royal Machine & Tool Corp.
P.O. Box Y
4 Willow Brook Drive
Berlin, CT 06037
860-828-6555
royal@royalworkholding.com
www.royalworkholding.com