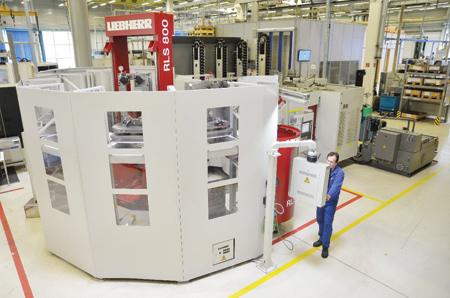
Pallet handling system RLS 800 for up to two machines
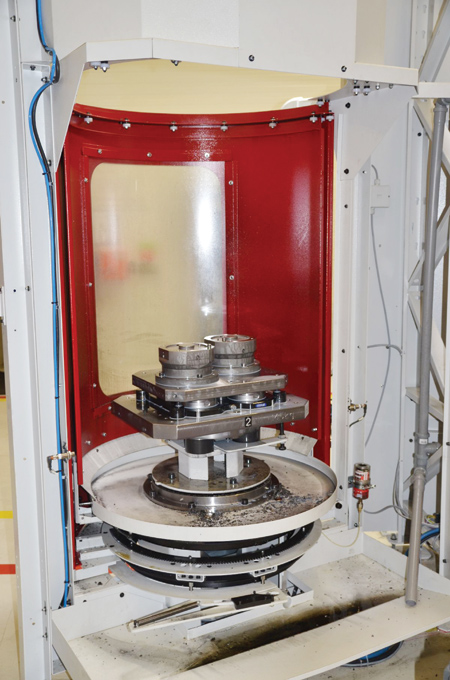
The integrated set-up space is located right next to the operator's side of the machine
"Small batch production automation poses particular challenges in terms of work processes, logistics and availability," said a company spokesperson. "The Berger Group has reacted to the markets' increasingly more stringent requirements - by rolling out Liebherr's Rotary Loading System (RLS) at its plant in Wertach, Germany. This helps enable the contract manufacturer to meet customer needs more flexibly, quickly and cost-effectively."
The components to be manufactured are complex components for innovative hydraulic power units that feature different bore and threading finishes and are available in a range of different versions. The manufacturing process itself is challenging.
Staff at Berger's plant in Wertach, which manufactures components predominantly for mechanical engineering firms, spotted the potential of an automation solution. The company decided to opt for Liebherr's Rotary Loading System (RLS) to meet its small batch and single-item production needs.
Featuring up to 24 storage bays the system has a high storage density while requiring minimal floor space. Furthermore, the design of the storage module allows another machining center to be integrated into the system. This helps ensure the required degree of flexibility. Given its modular design, this automation can be matched to current production needs quickly. The two available sizes, RLS 800 / RLS 1500, cover a range of applications. Berger specifically operates an RLS 800.
"Our focus was on reducing expensive set-up times. We needed to extend our machine-side tool storage capability," said Philipp Schneider, Head of Department at this branch of the group. The tool storage was upgraded upon request from 80 to 320 spaces. Furthermore, the modular, flexible-configuration rack columns were designed to enable customer-specific requests to be promptly met.
Liebherr specialists took responsibility for implementing the system. The equipment featured an all-purpose design, to provide as much flexibility as possible. During the period when the RLS was integrated into the existing solution, Liebherr worked with the milling machine manufacturer, Heckert. Together the two companies sorted out the interface issues between both systems.
"Operators like working on the RLS, because the integrated set-up space is located right next to the operator's side of the machine," said the spokesperson. The special design enables users to access the automation details easily. The surrounding window panels in combination with the user interface provide an overview of what is happening in and around the RLS. Through the cell controller software and the graphic user interface the required functions can be activated via `drag and drop.' The software, like the entire system, features a modular design. A range of different add-on packages can be hitched onto the basic package to enhance functionality. "Liebherr can adapt new applications to deliver process reliability - without having to modify the exiting computer system," said the spokesperson.
"The switch to the RLS for small batch production is paying dividends for Berger, particularly in terms of efficiency, customer focus and delivery capability," continued the spokesperson. "Given its newly acquired flexibility, the company is able to react quickly to short-notice changes in demand. Customers are supplied on time with exactly the models in the quantities they require and are therefore capable of reacting faster in changing market situations."
The RLS has also reduced the manufacturing cost impact of set-up times. The RLS allows operators to set up jobs in parallel with machining time. "In other words, the machine is not waiting on the next job, ensuring that set-up costs are not absorbed in machine hour rates. This concept optimizes spindle utilization and maximizes production output. Even an unmanned third shift could be feasible. Another effect of this changed production philosophy was that Berger was able to reduce its inventory," said the spokesperson.
For more information contact:
Liebherr Automation Systems Co.
1465 Woodland Drive
Saline, MI 48176-1259
734-429-7225
info.lgt@liebherr.com
www.liebherr.us