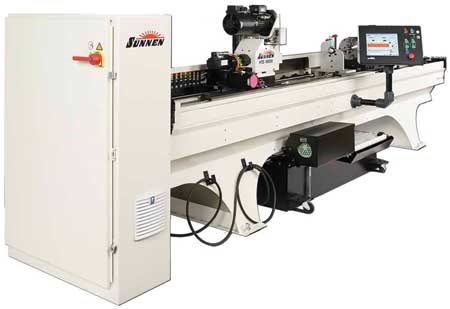
Sunnen's new HTE honing system is purpose-designed to produce precision bore geometry and surface finish in long, small bores. The machine's one-piece base is designed to maintain excellent tool/part alignment. The sensitive tool-feed system provides protection against tool overload - critical to successful honing of long, small bores. Tool specific force limits and run settings are stored in the Windows-based touchscreen control. A feed system senses tight sections in the part and corrects them automatically.
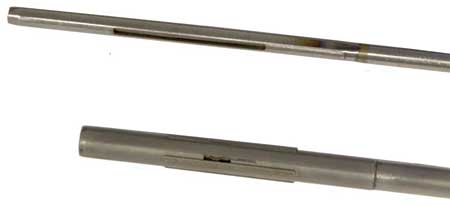
Sunnen LBT tools for gun barrels are available in diameters from 0.168" to 0.500". They carry two, three or four superabrasive stones (CBN or diamond) of varying length and width, depending on the tool's diameter. The LBT tool has a 0.005" adjustment range on diameter. The tool is made of through-hardened tool steel, and the stones are field-reloadable. Larger diameter tools can be custom-ordered.
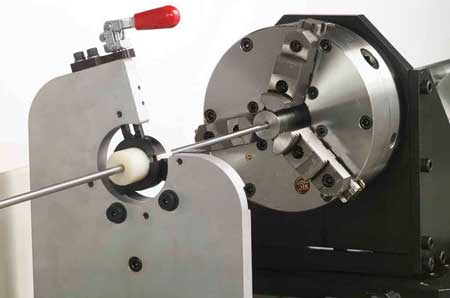
Three fixturing options are available with the HTE honing machine: a manual chuck, a pneumatic chuck or a V-type chain vise for parts with O.D.s up to 6" (150 mm). A traveling steady rest is standard. An optional guide pot automatically guides the honing tool straight into the bore without operator assistance.
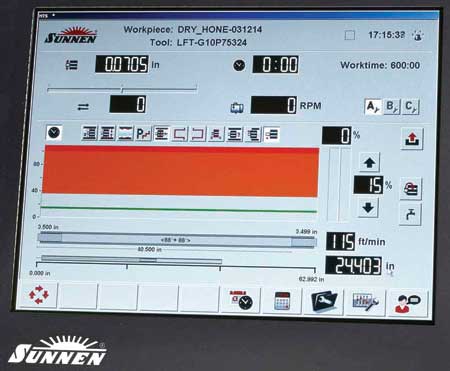
Highlights of the touchscreen display on Sunnen's HTE honing machine include a load meter (orange field) that shows tight or loose spots in a bore. The green band shows the programmed tool load. If the load goes into the orange for a programmed amount of time, the tool will retract and then continue to expand. If the load reaches the red band, the machine stops. The upper left box displays the expanded tool diameter. Once zeroed for a specific size, this shows the workpiece bore diameter while honing. The machine can also be programmed to hone for a set period of time, for example in a polishing/finishing operation where diameter size is not an issue.
Hammer forged barrels are not well thought of by precision rifle shooters, but a critical manufacturing process used in hammer forging is suddenly getting attention from custom barrel makers today. It is honing. Honing produces a high-quality bore surface fast, which is critical to hammer forging. Surface imperfections in a barrel blank before hammer forging tend to be amplified as the blank is formed on the rifling mandrel. In addition, if the bore is chromed afterward, imperfections in the surface finish become even more obvious.
Surface finish is the one feature of the barrel that cannot be controlled in hammer forging - garbage in garbage out. Some may ask, "What about a reamed bore finish?" Sure, hammer-forged barrel blanks are gun drilled and reamed, just like all barrels. But a reamer starts to dull after the first part; scratches in the bore get rougher. For this reason, makers of hammer forged barrels regularly hone the bores of barrel blanks to enhance the product and improve process consistency.
Honing improves bore diameter size uniformity and accuracy, surface finish and roundness throughout the length of the barrel and can be used in place of a pre-rifling lap. The chief difference between a lapped and honed bore is the direction of the finish lines in the bore. Honing leaves fine spiraling crosshatch lines, while a lap leaves lines going longitudinally in the bore. After rifling, the manufacturer can remove the crosshatch finish with a quick lap if desired. Honing is designed to be fast and accurate, and it can be automated. Its surface quality and geometry can duplicate lapping, except for the longitudinal lines of the lapped finish. Honing is one of the processes used to make affordable, mass-produced, hammer-forged barrels that regularly hit minute of angle (MOA) accuracies.
MOA accuracy may be a joke to precision benchrest shooters, but it is a breakthrough for the consumer market, and competition has some manufacturers bragging about half-MOA as their new standard.
For custom barrel makers, honing is a time-saver and cost cutter. A few minutes on a honing machine can cut lapping times in half, leaving a crosshatched surface finish in single or low double-digit Ra. Honing is the same process used to make diesel fuel injectors with bore roundness and straightness controlled to fractions of a micron (<0.000040"), with surface finish Ra 0.15 um (6 in).
Sunnen Products Company, a maker of these honing machines, is also a supplier to defense contractors and commercial firearms makers. The company recently introduced a new machine for .17 to .50 caliber. According to the company, its spindle can correct bore size imperfections so small only an air gauge can measure them. Early users aim to make sub-minute accuracy the norm for their standard rifle barrels.
Custom barrel makers are catching on to this, too, so it is time for a tip of the hat to the hammer forging guys for leading the way.
Authored by Dave Sengelaub, Sunnen Application Engineer
For more information contact:
Sunnen Products Company
7910 Manchester Road
St. Louis, MO 63143
800-325-3670 / 314-781-2100
sales@sunnen.com
www.sunnen.com