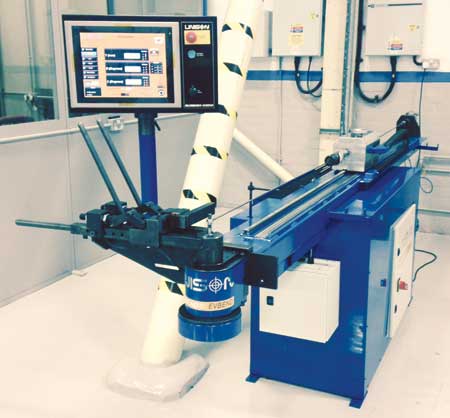
This second-generation Evbend 1000 CNC tube bender from Unison is designed to provide Supercraft with a cost-effective means of producing specialist precision parts in small batch sizes.
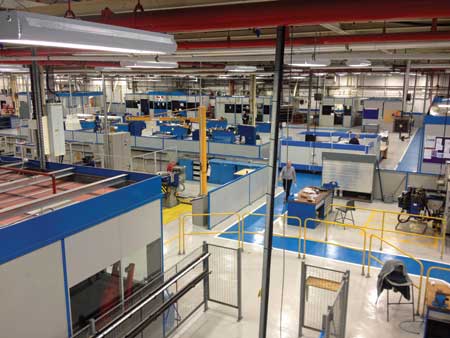

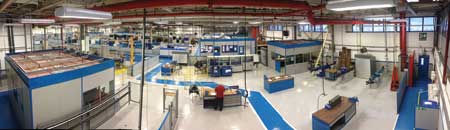
Supercraft's facility in Brough, UK, makes extensive use of tube and pipe bending technology to produce precision parts for the aerospace industry.
Unison has won a significant order for tube bending machinery from the precision aerospace engineering company, Supercraft. The machinery will help Supercraft to expand operations at its new manufacturing facility in Brough, UK, in preparation for contracts recently secured from major aerospace customers. According to Unison, the machinery will also provide the software flexibility needed to enhance productivity of specialist low volume parts through use of closed-loop manufacturing techniques.
The order calls for two Unison machines. Supercraft required an Evbend 1000 low-cost CNC tube bender - a machine designed to minimize the costs of producing small-batch high value parts by means of manually powered tube feed, rotation and bending, but with smart CNC-controlled braking on these axes to help ensure precision. The second machine is a 30 mm model from Unison's Breeze family of all-electric tube benders.
Supercraft is a leading manufacturer of precision components and assemblies for military and civil aerospace companies. Its facility in Brough specializes in the production of pipes and ducting for aircraft wings. The company makes extensive use of CNC tube and pipe bending technology and is capable of fabricating parts involving complex precision bends in tubes up to 100 mm in diameter. Automated bending machines in the workshop at Brough are networked to a central CAD/CAM resource, which includes an advanced laser-based coordinate measuring machine (CMM).
The CMM uses non-tactile laser measurement techniques to build detailed and accurate 3D computer models of bent parts. Measurements are typically taken from pre-production parts for process verification, with any necessary correction data being fed back to the bending machines. This efficient closed-loop manufacturing system helps Supercraft to meet the exceptionally high quality standards demanded of aerospace suppliers, and to minimize the time that it takes to commence volume production of parts. Measurements can also be acquired from customer-supplied parts and used for reverse engineering purposes. Customers are therefore free to specify their requirements in a wide variety of forms, including drawings, CAD models, files containing XYZ tube bending machine data and master parts.
Supercraft initially sought a replacement for a first-generation Evbend 1000 tube bender that it had used successfully for about 30 years. "Originally developed by a tube manipulation specialist to help companies reduce the cost of producing low volume precision parts, the Evbend machine has proved particularly popular in aerospace and motor racing industries," said a Unison spokesperson. "Unison acquired the manufacturing and design rights to Evbend and developed a new-generation version of the tube bender in 2014."
According to Supercraft's General Manager, Owen Sexon, "The Evbend machine provides a very cost-effective means of fabricating precision parts made in low volumes. We typically use it for bending five to 10 millimeter tubes with a half-millimeter wall thickness - many of the smaller diameter parts that we produce involve complex bend sequences and very small batch sizes - often in the order of just six to eight. Setting up one of our large existing machines for these types of needs is simply not economic."
However, until now, Evbend tube benders have essentially been standalone machines - the original controller had very limited I/O facilities - so when Supercraft sought a replacement it looked at a number of competitive machines that could be networked to its CMM. While investigating its options, Supercraft became aware that Unison had developed a new version of the Evbend 1000, which incorporated a powerful HMI and controller software designed expressly for ease of integration into factory networks.
As Owen Sexon said, "We are really impressed by the quality, breadth and ease-of-use of Unison's software. The fact that Unison was prepared to develop custom software and take responsibility for interfacing the new Evbend machine to our CMM made it an obvious purchase choice. For the first time, we are able to close the loop between inspection and bending on small batch size tasks as well as higher volume production. Eliminating what is often a highly iterative process will help us to improve productivity of prototypes and specialist parts significantly."
In addition to the Evbend 1000, Supercraft has ordered a Unison Breeze 30 all-electric bending machine to help expand production capacity to meet growing demand from aerospace customers. This machine will also feature a custom software interface for ease of integration with the company's CMM.
"Supercraft is a renowned tier one supplier to the aerospace industry," said Stuart Singleton, Unison's Head of Sales. "After evaluating our software and concluding that its ease of use conveys major productivity advantages, the company is keen to realize similar benefits on a larger high volume bending machine."
For more information contact:
ITEC/Unison
Innovative Tube Equipment Corporation
1807 W. Sunnyside Avenue
Chicago, IL 60640
866-574-TUBE (8823)
info@tube-equipment.com
www.tube-equipment.com
ITEC/Unison
Innovative Tube Equipment Corporation
16201 Dodd Street
Austin, TX 78641
866-574-TUBE (8823)
info@tube-equipment.com
www.tube-equipment.com
Owen Sexon, General Manager
Supercraft Ltd.
Building 54
Saltgrounds Road
Brough, HU15 1EQ, UK
+44 (0)1482 665971
info@supercraft.co.uk
www.supercraft.co.uk