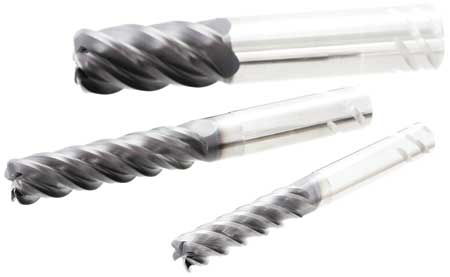
As a licensed partner, OSG will begin offering its cutting tool shanks with the patented pull out protection system, Safe-Lock from HAIMER.
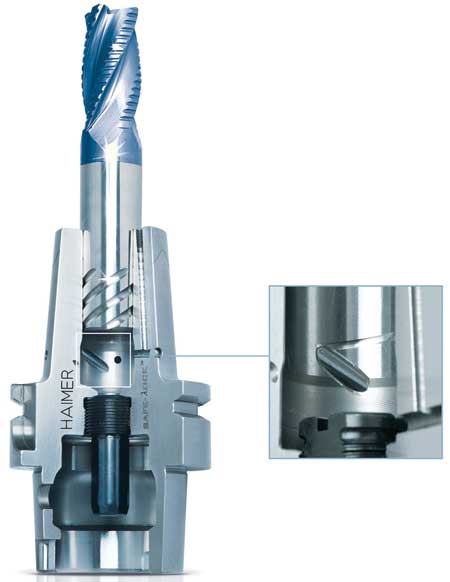
The Safe-Lock System from HAIMER is an integrated pull out protection for round cutting tools that uses a friction and form locking system. "It increases process security, enables a higher metal removal rate and provides results that are significantly better than conventional tool clamping systems," said a company spokesperson.
In April 2015 the OSG Corporation, a manufacturer of round cutting tools, and HAIMER GmbH, provider of toolholding technology, signed a strategic partnership and licensing agreement. The OSG Group is bringing its round endmill cutting tools to the global market now with the HAIMER Safe-Lock system.
The Safe-Lock design in cutting tools and toolholders combines a high precision press fit clamping with a positive form locking mechanism. This prevents round cutting tools from being rotated or completely pulled out from their toolholders during heavy machining. "The combination of symmetrical pull out protection, high concentricity and balance of the Safe-Lock system results in a vibration free machining process," said a HAIMER spokesperson.
OSG had been testing various systems for pull out security over the course of several months. Jiro Osawa, Technical Managing Director at OSG headquarters and CEO for North America, explained: "Our field testing proved that the combination of our endmills with Safe-Lock resulted in higher RPMs and feedrates even with difficult-to-machine materials. This enables our customers to obtain a significant increase in their current metal removal rates, while at the same time having a higher security in their machining processes. Safe-Lock also has a very positive effect on tool wear." For the globally oriented corporation that is represented in 29 countries with 52 subsidiaries, over 5,000 employees and annual sales of approximately one billion dollars, there was one further crucial factor, as Jiro Osawa noted: "Safe-Lock is available in various clamping methods. Since we are not only in Japan but also well represented in North America and in Europe, we have decided to sign this license agreement and integrate the Safe-Lock design into our tools worldwide." OSG is headquartered in Toyokawa, southeast from Tokyo, where it has its solid carbide endmill production, coating facilities and production halls with modern CNC grinding machines. "Due to these manufacturing capabilities, the company is able to insure the highest level of quality and availability of their tools," said an OSG spokesperson. "An additional global production network enables the demands of local markets and customer needs to be met with fast delivery and the high levels of service and support."
Andreas Haimer, President of the HAIMER Group, said: "We have established Safe-Lock as a standard in roughing and heavy machining for which a variety of tools are available worldwide. We are very proud to have reached a strong partnership with OSG, one of the largest and leading producers of tools in the world."
"Productivity increases resulting from the pull out protection is not restricted to typical aerospace applications, but can also be used in any typical milling application," said the HAIMER spokesperson.
For more information contact:
HAIMER USA
134 E. Hill Street
Villa Park, IL 60181
630-833-1500
haimer@haimer-usa.com
www.haimer-usa.com
OSG USA, INC.
676 E. Fullerton Ave.
Glendale Heights, IL 60139
800-837-2223
info@osgtool.com
www.osgtool.com