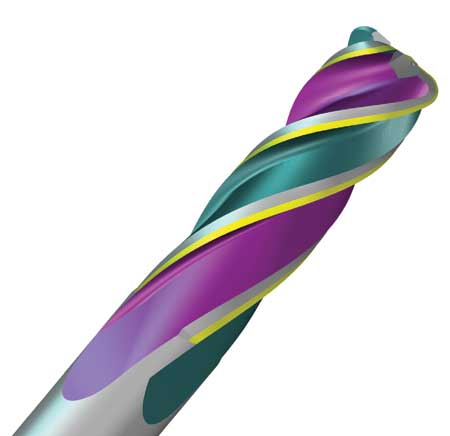
NUMROTO tool grinding software now automates production of complex geometry tools, such as this corner radius cutter featuring differential helical edges with constant land width.
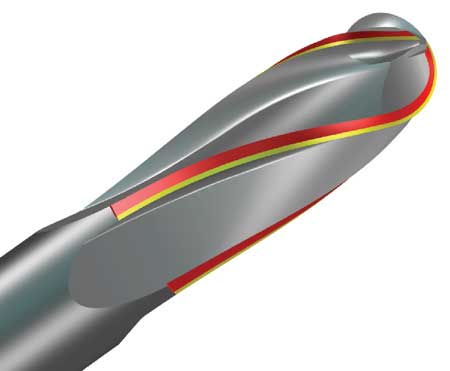
Complex geometry cutting tools, such as this full radius cutter with differential helical edges and a constant land width, can now be easily produced by using NUMROTO tool grinding software, according to the company.
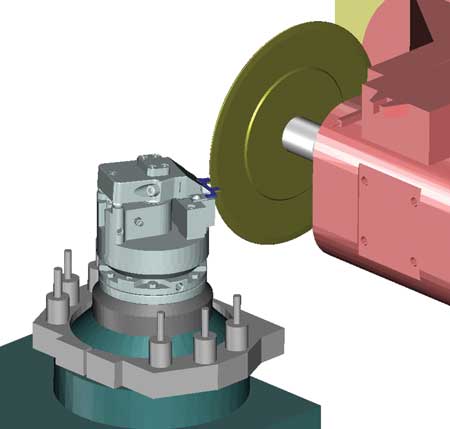
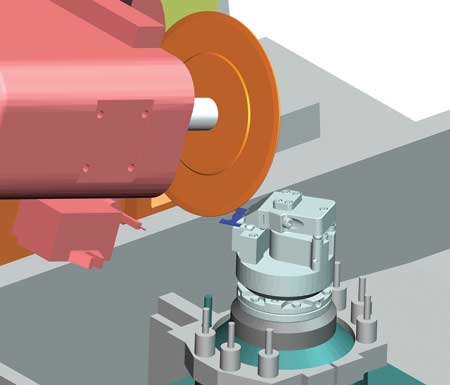
NUMROTO tool grinding software now allows use of a production clamping system for profile inserts in the 3D simulator (image courtesy of Michael Deckel GmbH).
The latest release of the NUMROTO tool grinding software package is designed to resolve the growing challenges of grinding and servicing new generations of complex-geometry drills and end mills. Version 3.8 of NUM's software automates multi-helical and variable flute grinding and provides a new form cutter function for profile inserts. It is available to existing NUMROTO users as an update.
NUMROTO runs on NUM's Flexium+ CNC system. According to the company, it utilizes sub-nano interpolation to help ensure high quality surfaces with short cycle times to allow fast 5-axis movement - even if the part program contains a high density of ISO sequences. "Flexium+ supports all the safety functions that are needed on today's high performance machines and can be operated very easily, using the same type of 'dual touch' gestures that are employed with modern smartphones," said a company spokesperson. The software is used on more than 40 different types of machine tools.
"Many of the high performance end mills that manufacturers now employ for precision machining applications, such as the production of aircraft components from specialist alloys or composite materials, are multi-helix tools designed for use at speeds up to 30,000 RPM," said the spokesperson. "Producing these types of tools cost-effectively is a demanding process that requires increasingly complex grinding capabilities. For example, to help prevent vibration, each of the tool's cutting edges is twisted at a different angle - and with differential helix designs, the twist angle of each individual cutting edge also changes along the length of its body, from the tip of the tool to the shaft. Furthermore, the width of the flute area of these tools can vary considerably, demanding precise positioning of the grinding wheel to ensure that the land width on the back of the tooth is correct.
"By harnessing the speed and computational capabilities of modern PCs, the latest version of NUMROTO software is able to handle the extremely complex path calculations necessary to create these sophisticated flutes. Users can now define the core path geometry of flutes on end mills easily and accurately.
"Designers and manufacturers often seek this functionality when optimizing the chip transport characteristics of high performance machine tools. The rate at which chips are removed from the cutting face has a major bearing on the tool's cutting speed and efficiency."
By allowing the core path of each flute to be defined individually, NUMROTO also makes it possible for tool designers to compensate for any potential imbalance caused by irregular helices or asymmetric cutting blades. Additionally, by enabling the entry point of the grinding wheel to follow the corner radius of the cutting edge, the software now facilitates the grinding of a defined rake angle on complex body forms and on cutting edges that pass from the body of the tool to its tip - a task that, according to the company, was previously difficult to achieve.
Today, the cutting edges of most cutting tools are ground from tungsten carbide. Small rotary tools are usually manufactured from a single piece of carbide, whereas larger rotary tools and the majority of non-rotary tools feature individual cutting blades in the form of carbide inserts, which are retained in a holder made from a less expensive material. "Until recently, the inserts were soldered or cemented to the holder prior to being ground, which sometimes made it very difficult or impossible to produce or maintain such tools on a CNC tool grinding machine due to their size and complexity," said the spokesperson. "Another disadvantage of this approach is that it requires the manufacturer to define the complete assembly as a rotary tool in the CNC program, which requires time-consuming and expensive programming.
"Working in partnership with a number of leading machine tool manufacturers and tool sharpening companies, NUM has further developed NUMROTO's form cutter function to simplify insert grinding. Users can now define a form cutter as a rotary tool or as a standalone profile insert. Holders with soldered or cemented inserts can still be defined as rotary tools, and the position of each insert can be probed individually, allowing any mounting inaccuracies to be detected and compensated for automatically during the grinding process."
Many of the latest cutting tools employ user-replaceable profile inserts, which are ground as physically separate blades on a CNC grinding machine. Instead of being fixed to a holder during grinding, the insert is held in a production clamping system that has an optimized geometry for efficient grinding, with unobstructed working space for the grinding wheel.
"NUMROTO's new profile insert function simplifies the programming of the new types of ultra high efficiency CNC tool grinding machines that are now coming into service," said the spokesperson. "After selecting the profile insert form cutter, users are presented with an easy-to-understand menu that enables them to specify whether the part to be ground is held in a fixed or adjustable collet, or by clamping plates. The software supports different mounting plate arrangements to allow the insert to be oriented in any of three planes and provides a simple means of specifying parameters such as transverse and longitudinal offset values."
NUMROTO also now supports 3D models for the production clamping system, which enables it to be visualized during 3D simulation and monitored for collisions with the grinding wheel. The insert itself is displayed as a cube-shaped blank.
For more information contact:
Steve Schilling
NUM Corporation
603 East Diehl Road, Suite 115
Naperville, IL 60563
630-505-7722
sales.us@num.com
www.num.com
www.numroto.com