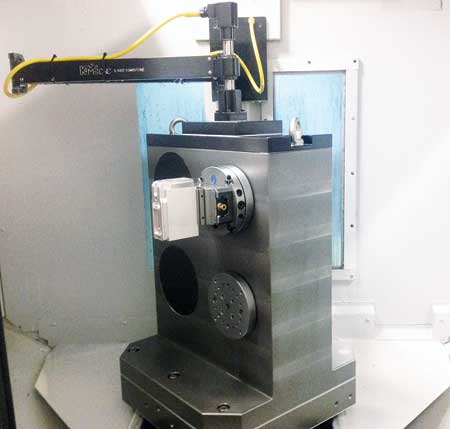
A KME CNC 5-axis tombstone in the HMC's loading station at Mainland Machine. The cable management system allows quick and easy movement of the tombstone into position for machining operations.
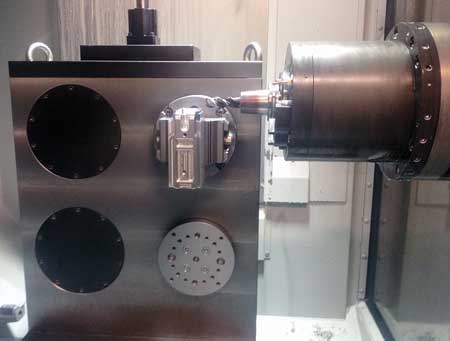
With KME CNC's 5-axis tombstone and a 5-axis vise, there is no need to make custom fixtures for the first operation of 5-axis machining.
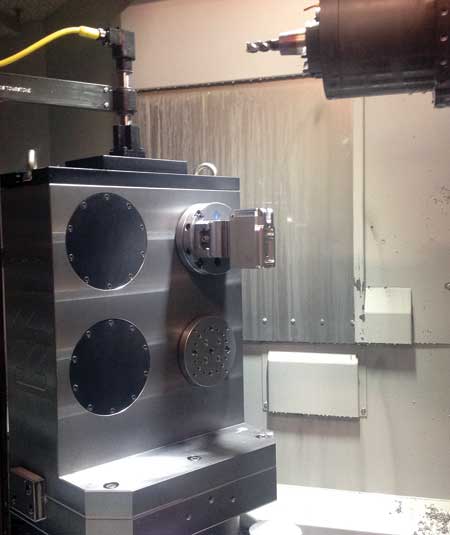
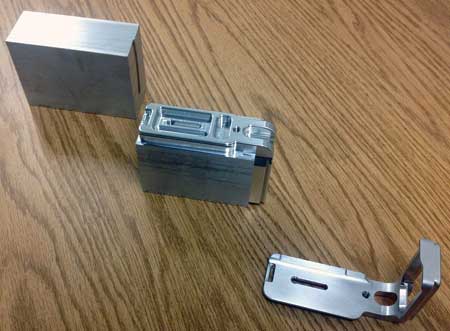
Shown is the machining stage progression for an L-plate, a device used for mounting a camera to a tripod in a horizontal or vertical orientation. The material is 6061-T6 aluminum. Requirements include highly precise tooling blends, tight tolerances and fine finishes. The part, which previously took 23.75 minutes on a VMC with a 5-axis trunnion, is now completed in 16.9 minutes with an HMC and KME CNC 5-axis tombstone.
Mainland Machine, a contract manufacturer of precision machined components specializing in close tolerance CNC production, needed to increase efficiency and improve machining reliability. Current machining operations were problematic, due to the machines being incapable of producing the needed surface finishes and blends. The machines were old and tired, breaking down on a regular basis and driving up maintenance costs and lowering production.
"We were at a point where we were reevaluating the way we did everything," said Mark Ames, President, Mainland Machine. "If there was a more efficient way to do things, we were willing to explore it and find the best way to move forward.
"Our first major step took place three years ago, when we invested in two Mori Seiki horizontal mills. With horizontal milling, the machine does not have to be devoted to a single part for weeks at a time; the machines are capable of running multiple jobs simultaneously."
Five-axis machining has been a major part of Mainland Machine's production for quite some time. "The more surfaces that can be machined without letting go of the part, the more precise the part will be," said Ames. "Constantly letting go of a part and putting it into another set-up means tolerance is dependent upon the machine operator placing the part correctly and precisely into the fixture."
"We were open to any ideas," said Ames. "After reviewing all of our options, we ultimately selected a KME 5-axis tombstone." This was based on its ability to combine the reliability and flexibility of horizontal machining and the ability to hold tighter tolerances with 5-axis machining. "It was too good to pass up," said Ames.
Another reason for the selection of the KME 5-axis tombstone over a conventional trunnion was costs associated with repairs. "To have a conventional trunnion repaired requires removing it from the mill, crating it and paying freight each way," said Ames. "It can require a three to four week lead time and cause almost unrecoverable costs in production loss. On the other hand, with our KME 5-axis tombstone, the replacement components are light enough to ship by UPS and we can easily replace the components ourselves. So there is no need to ship the whole unit down for repairs. We are even able to perform software updates over the Internet through the use of a USB cable."
KME CNC's 5-axis tombstones provide a way to utilize 5-axis positioning on virtually any machine. All that is required is one M-code, no matter how many indexers are involved. According to the company, the harmonic drive technology used allows a +/- 5 arc second repeatability as well as a guaranteed zero backlash for 10,000 hrs.
KME CNC's standard 5-axis tombstone for horizontal machining centers comes with four platters or can be customized, based on customer needs, to include up to eight platters (or even 12). This live tombstone lets customers machine multiple 5-axis work in a single set-up. It allows the operator to index each 5-axis platter independently or simultaneously. "With one set-up, customers never have to remove the workpiece," said a KME CNC spokesperson. "For instance, a custom tombstone with eight platters will have its platters working simultaneously or independently, giving it the ability to share tools with eight different parts, thus minimizing tool changes in addition to producing close tolerance parts and saving a tremendous amount of time."
According to Ames, the 5-axis tombstone has solved their production challenge. "In some cases, we are getting double the production we were getting from our older machines," he said. "We have been making similar parts for years and they have never looked this good. In addition, our deburring department does not have to work on the parts nearly as much."
For one aluminum component in particular, machining time was 23.75 minutes on a vertical machining center (VMC). Using the 5-axis tombstone and an HMC, machining time has been reduced to 16.9 minutes. In addition, it meets the highly precise tooling blends, tight tolerances and fine finishes required by the customer.
Founded in 1983 by Mark Ames, Mainland Machine features a variety of machines and capabilities, including four turning centers (sub-spindle, live tooling, Y-axis), five VMCs (two Okuma M560-V one 5-axis, one pallet changer, up to 45 x 25 table size), two Mori Seiki NH5000 DCGs (spindle speed 14,000 RPM, 240 tool changer,), CAD/CAM (SolidWorks, Esprit) and a rapid prototype machine, and also offers vibratory deburring, laser engraving, and precise, multi-component product assembly services.
For more information contact:
Mark Ames, President
Mainland Machine
2930 McMillan Ave Unit E
San Luis Obispo, CA 93401
805-543-7149
mark@mainlandmachine.com
www.mainlandmachine.com
Robert Reynolds, Director of Sales
KME CNC
1643 West Orange Grove Ave.
Orange, CA 92868
310-709-9364
robert@kmecnc.com
www.kmecnc.com