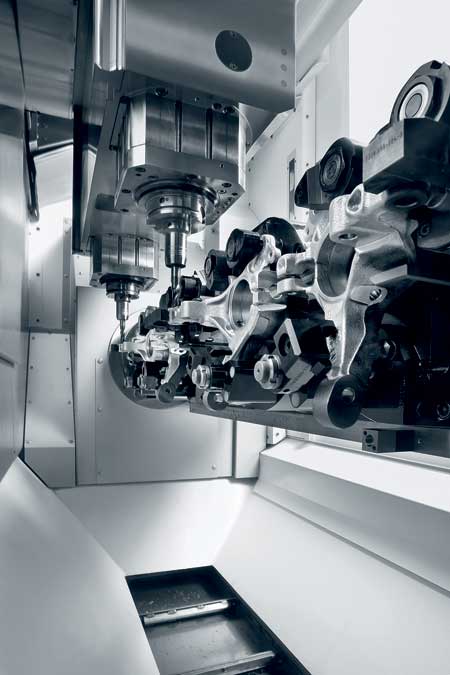

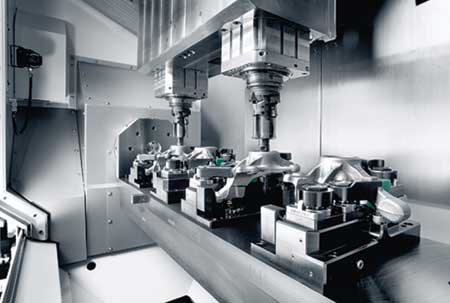
Double-spindle heavy-duty chip removal from wheel mountings. The machine features complete machining in two fixing positions on a two place center.
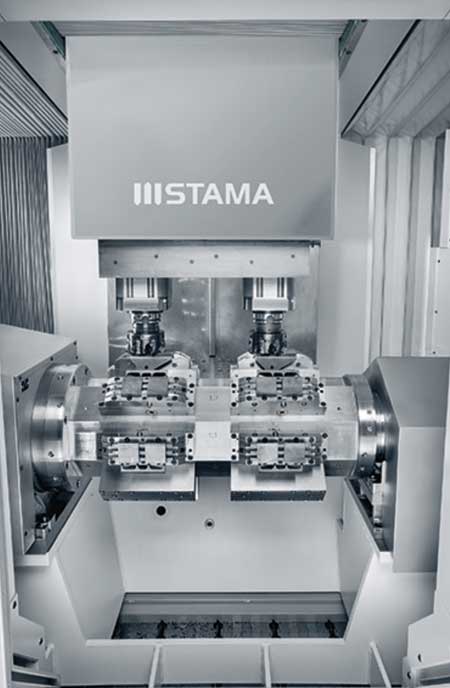
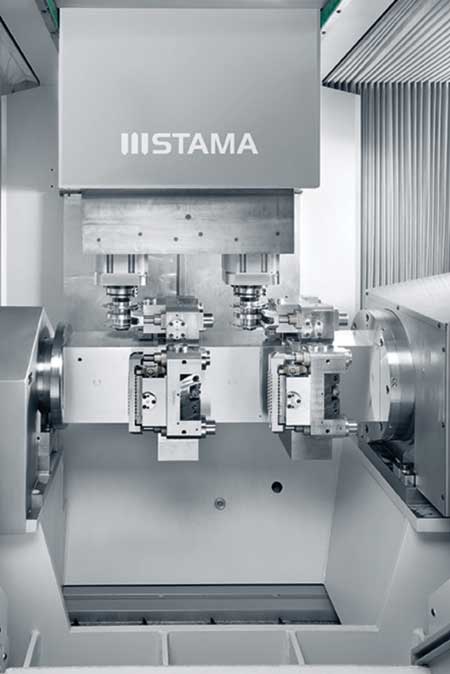
High productivity heavy-duty chip removal for notched bar impact tests with loading and unloading parallel to main time on a Twin two place center.
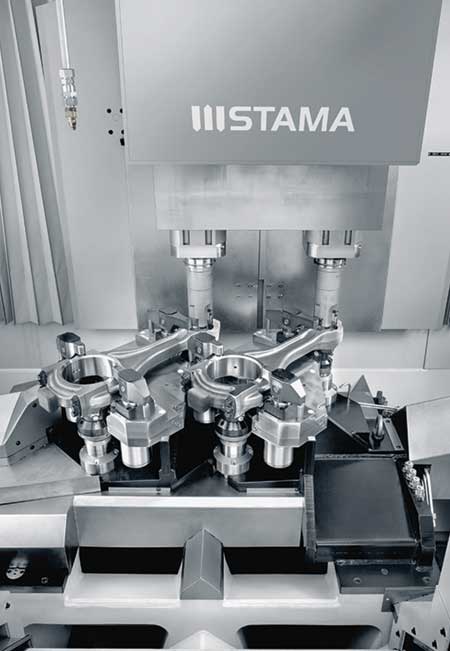
Double-spindle fine machining of connecting rods with HSK-A100. Required precision: 5 um.
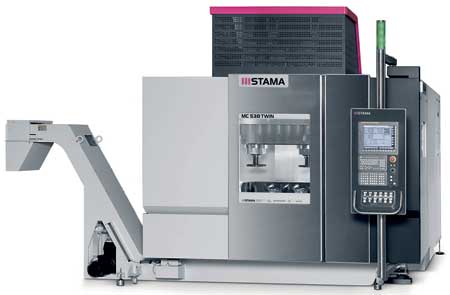
The MC 538 Twin one place model features an HSK-A100 and spindle distance of 600 mm.
The MC 538 Twin machining center from Stama features double-spindle 3-, 4- and 5-axis machining with a dynamic power development for heavy-duty chip removal. It is designed for difficult-to-machine workpieces, such as those found in the automobile and aerospace industries, as well as those that require precision in the 2 to 5 um range, such as the fine machining of connecting rods.
According to the company, the overall height of the new MC 538 Twin's body is about 30% less than its predecessor model, and the guideways in the Y and Z axes are 80% bigger. All machine components are designed using the finite element method for improved thermal and mechanical stability. The HSK-A100 motor spindle provides heavy-duty chip removal. Movements are in units of one hundredth. Stama offers four spindle distances (266, 320, 400 and 600 mm) in different performance classes with the Twin models.
The Twin's 2 plus 4 principle (two work spindles, four clamped workpieces) is designed to provide a unit cost benefit of 30 to 40%. With an interference area diameter of 850 mm and a length of 1,600 mm between the rotary indexing table and counter bearing, there is enough workspace for a large range of parts and multiple fixtures. This gives operators flexibility in process design and for varying manufacturing tasks. All machining forces are dissipated directly into the machine's base frame for enhanced stability and precision. The workspace is designed for optimal chip removal. The opening travel of the newest door system is 50% wider than that of the previous version. The operating area is laterally and vertically stepless adjustable and offers ergonomic improvement for the operator.
Another benefit of the new 38 series is the compact design. The machining center features a small footprint of 13 square meters. Including peripherals, i.e. cooling lubricant and chip remover, and requirements, the footprint is a little over 20 square meters. Having less mass to move increases the dynamics. With the new 38 Twin series, the operator platform's crosspiece no longer carries all the tools around with it. The active tool magazine with 40 places (optionally 64 places) is now integrated and positioned in the base frame and each tool can weigh up to 18 kg. The large interface gives tool manufacturers more freedom to optimize the various chipping operations when designing processes and fixing devices.
For more information contact:
Stama Maschinenfabrik GmbH
D-73278 Schlierbach
Germany
+49 7021 572-1
info@stama.de
www.stama.de
Chiron America Inc.
10950 Withers Cove Park Drive
Charlotte, NC 28278
704-587-9526
info@chironamerica.com
www.chironamerica.com