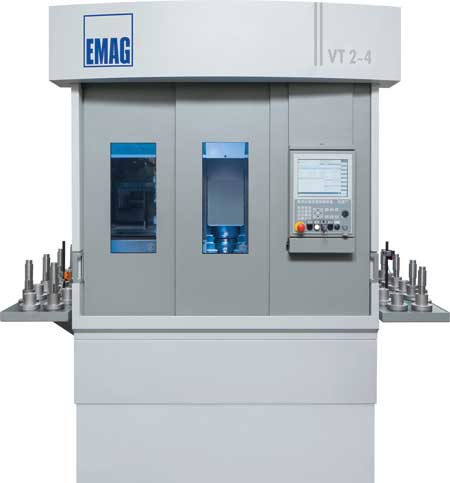
The VT 2-4 is a 4-axis turning machine for shafts up to 400 mm length and 63 mm diameter.
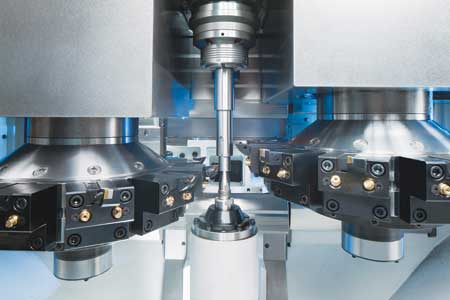
The VT 2-4 is 4-axis large-batch machining of shafts for electric motors.
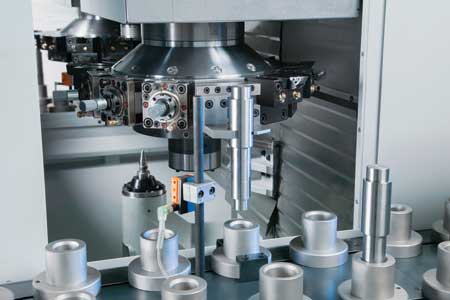
A grab in the turret collects the workpiece from a laterally placed conveyor belt and ensures that the machine loads itself.
"According to market experts, the demand for electric motors will grow dramatically, and this at a time when new transmission systems are becoming highly efficient," said an EMAG spokesperson. "The European Union commission, for example, has expressed that inefficient motors presently used in the automotive industry and other sectors should be replaced by the new electric motors by 2020. To ensure that the manufacture of complex components becomes even more efficient, the focus must be on the systems used to make them. The EMAG Group has developed a tailor-made solution for the manufacture of shafts for electric motors: the fully automated VT 2-4 Vertical Turning Machine. It makes the called for step-change in shaft machining a reality.
"According to latest EU guidelines on the manufacture of electric motors, the energy-efficiency of many electric transmission systems is to be increased by 30%. As manufacturers explore this market opportunity, this development also brings with it some challenges. As the manufacture of these components not only calls for solutions of greater effectiveness, the design of these modern motors also increases the demands made on its constituent components."
"We know about these challenges in the manufacture of the central components for electric motors," said Dr. Guido Hegener, Managing Director of EMAG Salach Maschinenfabrik GmbH. "A particular focal point is demanding shaft manufacturing, where a lot depends on the machine tool used. In a batch production environment, idle times must be kept short and component costs low. But this must be achieved without loss of flexibility in the production process."
Automation for Short Idle Times
The specialists at EMAG have developed the VT 2-4 4-axis Vertical Pick-Up Turning Machine for the machining of shafts up to 400 mm length and 63 mm diameter. Its automation provides for fast chip-to-chip times and helps ensure component costs are kept low. Workpiece grabs are used to transport the raw parts into the machine and retrieve them again upon completion of the machining process. Depending on the component, the changeover time can be as short as six seconds. "In a mass production environment, such short idle times soon add up to provide enormous time savings," said Hegener. "They also guarantee an energy-efficient production process, as a large part of a machine tool's energy is consumed during downtimes."
The actual turning process, with spindle speeds of up to 6,000 RPM, also helps to achieve short cycle times. The shaft is clamped vertically between workspindle and tailstock and machined from two sides. This work is done by two turrets with 12 tool stations each. The stations can be equipped with turning tools and driven tools (with one station being occupied by the grab). For milling work, required for keyways for example, the machine can be equipped with a Y-axis. The vertical alignment of the workpiece is designed to ensure permanent process integrity, where the unhindered chip flow prevents the build-up of chip nests in the machining area.
Space-Saver
"Another decisive factor for economic production is the external dimension of the machine tool," said the spokesperson. "In the case of the VT 2-4, the machine base is already small as the vertical design minimizes its footprint." Production planners also do not have to provide for additional raw part and finished component storage, as this is integrated into the VT 2-4. These machines can also be linked-up in close formation, forming a complete manufacturing line.
"We have developed an altogether very compact manufacturing system that is highly flexible and a future-safe investment," said Hegener. "There are a lot of possible applications out there for this system, especially in the manufacture of shafts for electric motors. We are offering a machine tool that allows the user to implement demanding machining processes and to save on costs."
Specifications include:
- Chuck diameter: 160 mm
- Travel in X: 340 mm
- Travel in Z: 625 mm
- Spindle: 1 qty
- Main spindle power rating 40% / 100% duty cycle: 34 / 26.5 kW
- Torque 40% / 100% duty cycle: 144 / 112 Nm
- Speed max.: 6,000 RPM.
For more information contact:
Peter Loetzner
EMAG LLC
38800 Grand River Avenue
Farmington Hills, MI 48335
248-477-7440
info@usa.emag.com
www.emag.com
Southwest
AR
Ken Pope
EMAG LLC
256-642-6842
kpope@emag.com
www.emag.com
TX, OK, LA
Ric Lorilla
EMAG LLC
248-595-1530
rlorilla@emag.com
Southeast
VA, NC, SC, GA, FL
David Fitzgerald
EMAG LLC
248-595-1117
TN, AL, MS
Ken Pope
EMAG LLC
256-642-6842
kpope@emag.com
www.emag.com
Northeast
PA, NY
Kirk Stewart
EMAG LLC
248-996-4703
kstewart@emag.com
ME, NH, VT, MA, RI, CT, NJ, DE, MD
Jonathan Chomicz
EMAG LLC
248-497-8526
jchomicz@emag.com
WV
Ken Pope
EMAG LLC
256-642-6842
kpope@emag.com
www.emag.com
Midwest
IN, OH
Kirk Stewart
EMAG LLC
248-996-4703
kstewart@emag.com
MI
Geoff Fuller
EMAG LLC
248-632-2021
gfuller@emag.com
ND, MN, WI, SD, NE, KS, IA, MO, IL
Tod Petrik, Regional Sales Manager
EMAG LLC
248-470-2646
tpetrik@emag.com
KY
Ken Pope
EMAG LLC
256-642-6842
kpope@emag.com
www.emag.com
West
Arnie Sugiyama
Caltec International
19801 Hamilton Ave
Torrance, CA 90502
310-527-4110
arnie@caltecusa.com