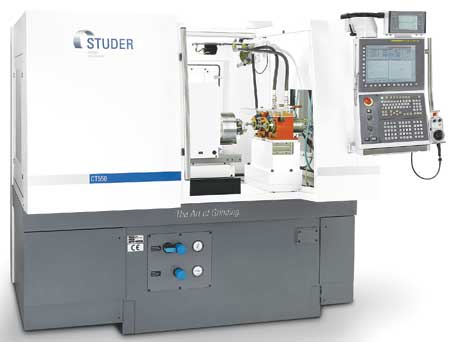
Featuring up to three inline grinding spindles, the CT550 is a compact machine for medium-sized workpieces.
United Grinding has increased its I.D. grinding capabilities with the addition of the Studer CT internal cylindrical grinding machine series. The series is designed to provide enhanced precision, surface quality and metal removal rates. By saving on auxiliary times, the CT550 shortens the cycle times of the grinding process, reported the company.
The CT550, which offers up to three inline grinding spindles, is a compact machine for medium-sized workpieces. "The modular and flexible arrangement of spindles enables optimal dimensioning of the machine, ranging from the manufacture of individual parts to large-scale production," said a company spokesperson. "This machine also supports an integrated and autonomous loading system."
The Granitan S103 machine bed provides a rigid and thermally stable base. The formula of this mineral casting is designed to absorb the high forces that occur during grinding.
"Due to its thermal behavior, the machine bed largely equalizes brief variations in temperature so that the machine operates with consistently high precision, even with changing ambient temperatures," said the spokesperson. "Its rigidity and damping characteristics provide enhanced surface quality of ground parts and long grinding wheel lifetimes."
Studer's CT550 can be utilized for small- to medium-sized internal cylindrical grinding applications such as die plates, spring collets, tool holding fixtures, hydraulic components and thread ring gauges composed of hard materials like tool steel, carbide, ceramics and glass.
Three inline modular spindles provide flexibility and optimal dimensioning. The diameter of the high frequency (HF) spindle ranges from 80 mm to 120 mm. The belt-driven spindle diameter is 80 mm. External grinding wheel is 305 mm. Axes travels are 520 mm (X) and 250 mm (Z). The manual B-axis setting angle is +1°-1°. Workhead speed is 1,200 RPM, maximum. Load on the spindle nose is 100 kg. Center height above the table is 1,500 mm. Maximum part length, 650 mm, while the grinding length is 150 mm. The control is the intuitive FANUC 310i-A.
For more information contact:
United Grinding Technologies
510 Earl Blvd.
Miamisburg, OH 45342
937-847-1253
www.grinding.com