
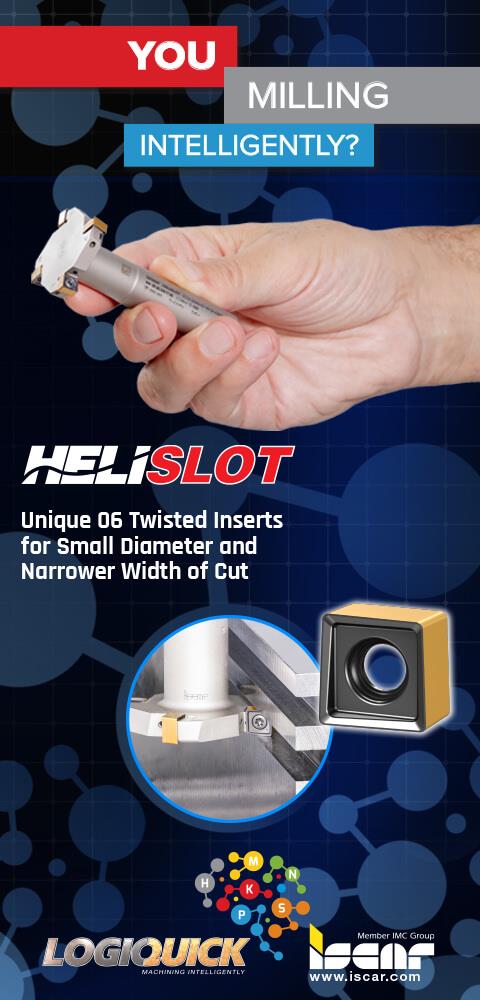
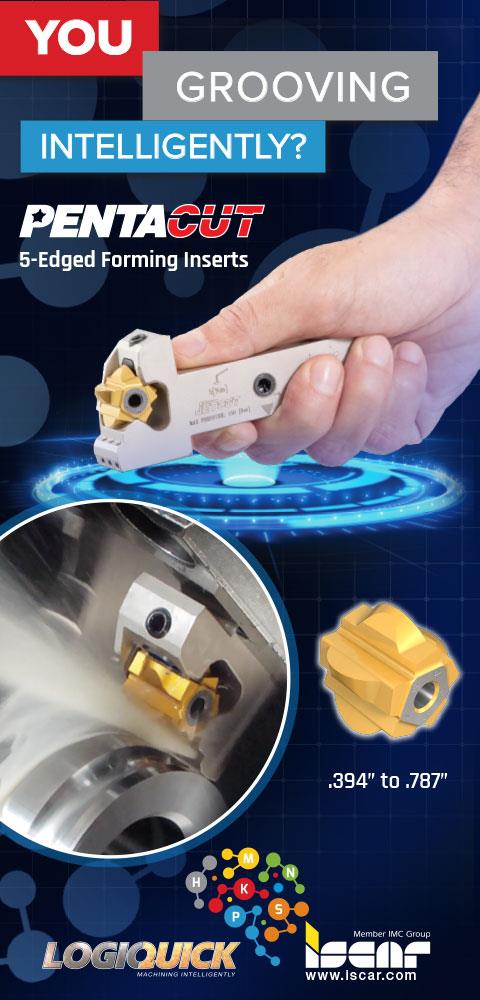
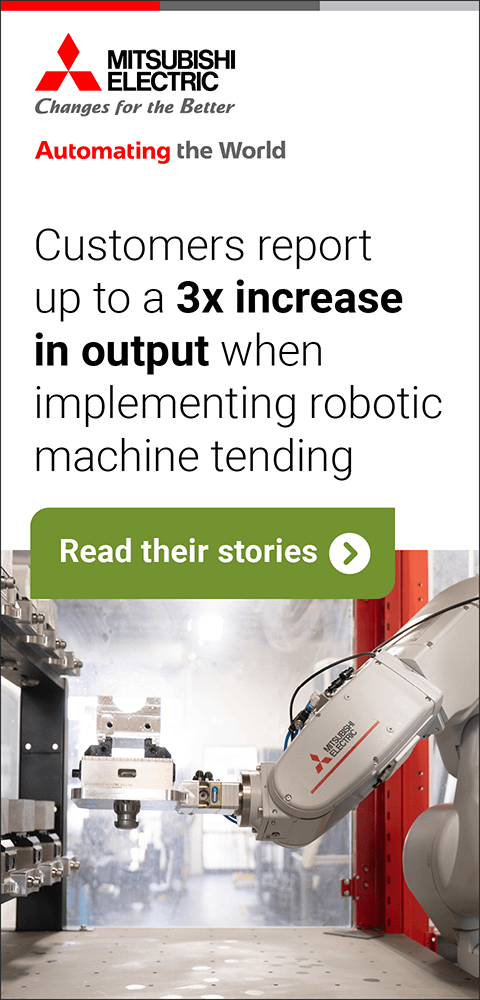
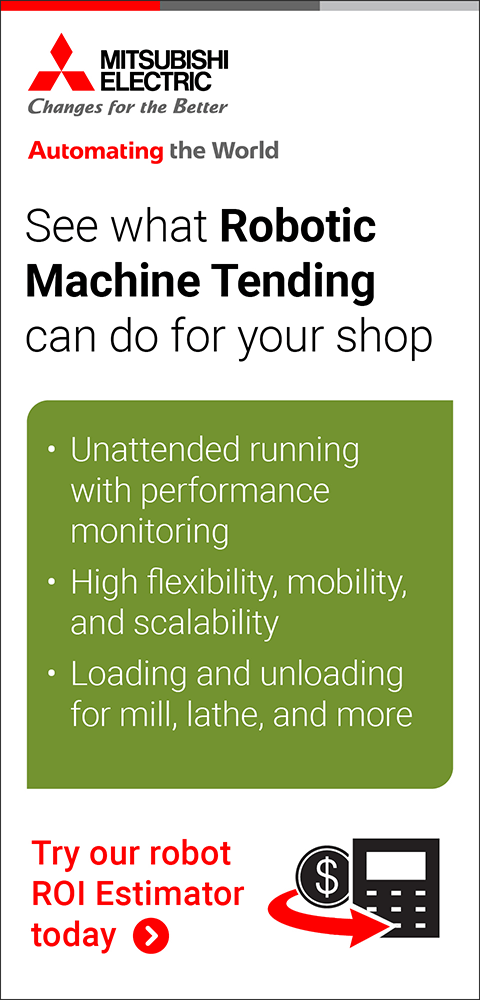
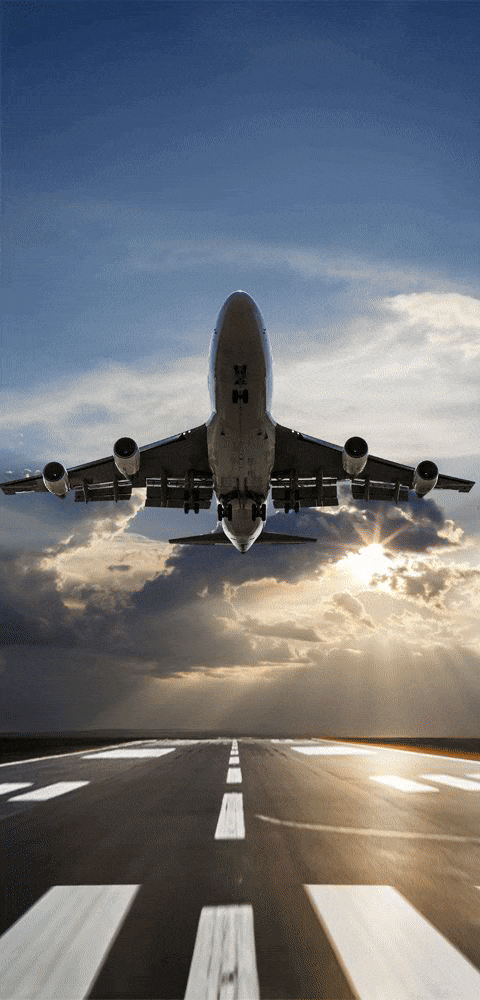
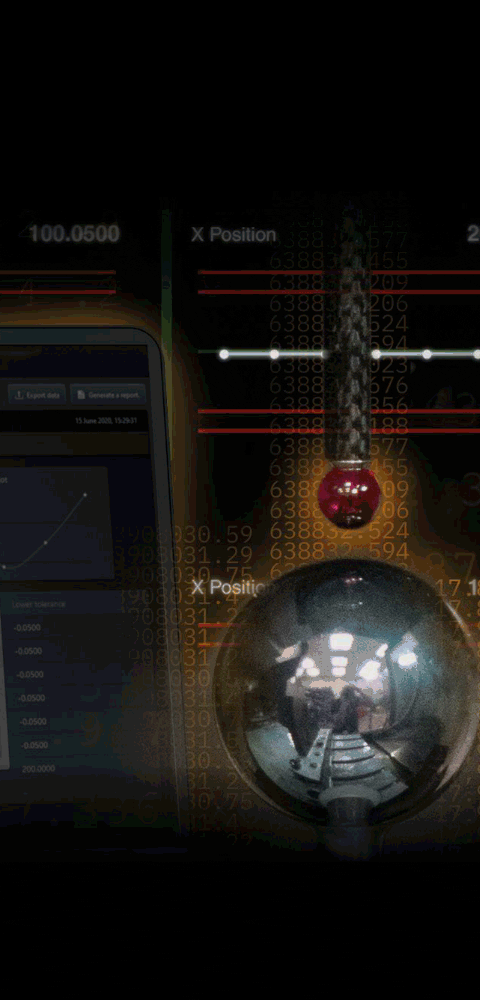
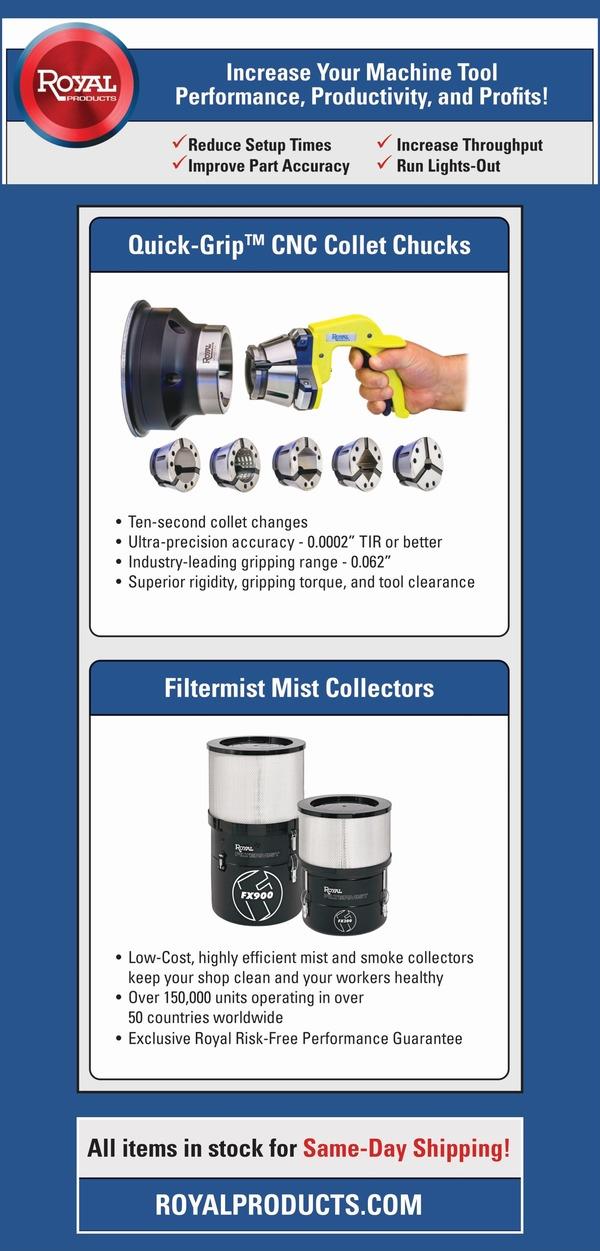
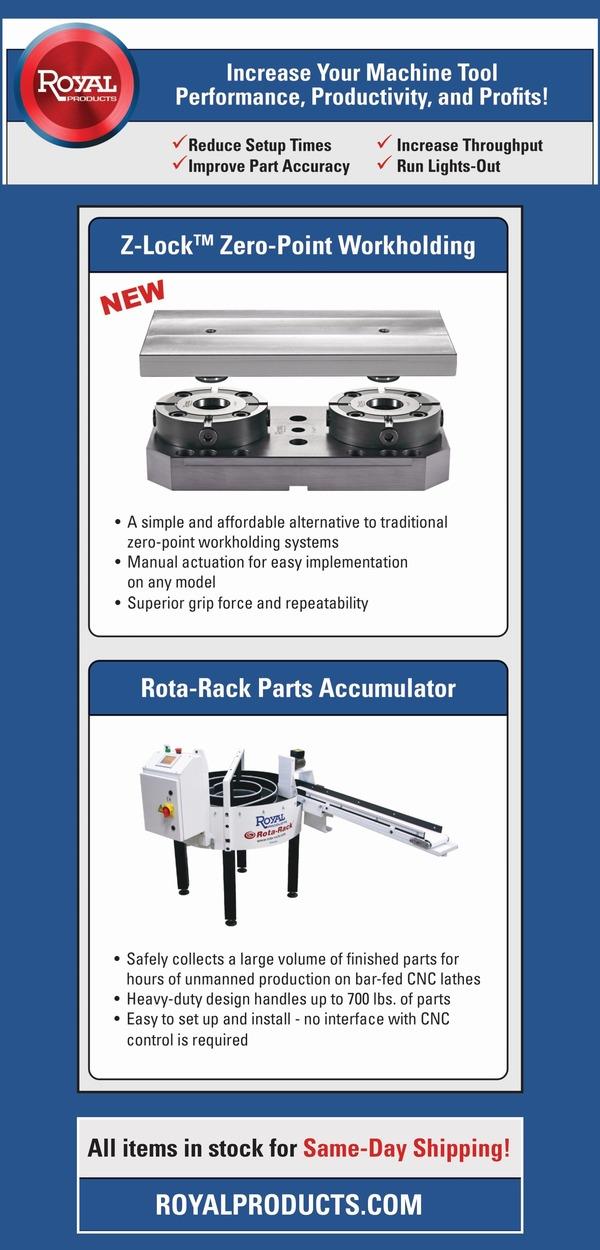

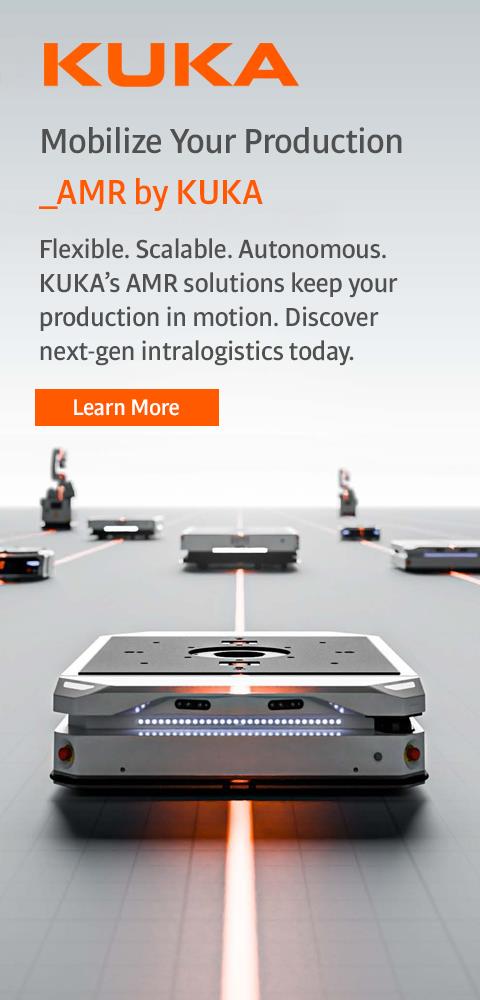
Radan Software to Showcase at FABTECH 2013
November 1, 2013Radan Software (Booth #S1838) will showcase the newly released Radan 2014 during FABTECH 2013. The latest release incorporates new features including 3D workflow improvements, safety measures to prevent tipping on flat-bed lasers along with strides in common cutting on punches and support for cluster and asymmetric wheel tools. FABTECH 2013 will be held at the North and South Halls of McCormick Place, Chicago, Illinois November 18-21, 2013.
“Radan 2014 has been under development for more than 12 months and recent feedback from the Beta testers, reseller channels and a number of selected end users shows it contains something for everyone,” said a company spokesperson.
“For example, Simulation and time calculation have improved by moving away from NC verification to the area where sequences are defined. Another improvement includes enhancements to 3D Workflow, which reduces the time taken to get parts to the nest.
“In addition, support for cluster tools means they can now simply be added to the master tool file, allowing Radan to automatically ensure the best arrangements of cluster tools to punch a specific pattern.”
Radan 2014 adopts the same common cutting strategy for punch presses as that used for profiling machines. It allows for common cut nests to be created automatically, meaning the user can choose how many parts form a common cut cluster of parts, reducing the sheet's instability. Tagging for common cut parts has also been improved. "With the absence of a skeleton - which is inherent to common cutting - the tag placements have to be absolutely right," says Olaf Körner.
The nest project workflow has also been improved providing graphical and interactive help when necessary, informing a user when a part is not closed, when tooling is out of date or what improvements are needed.
< back