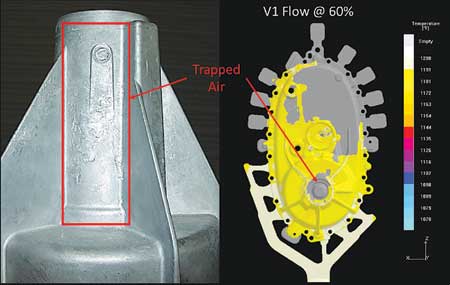
The simulation of the transfer tool showed that the filling pattern trapped excessive amounts of air during filling.
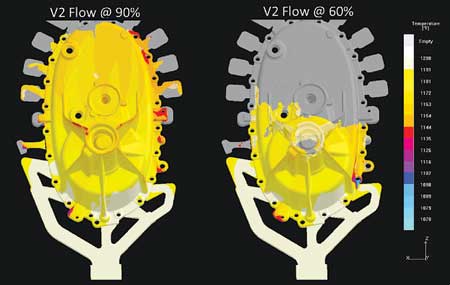
The simulation of the transfer tool showed that the filling pattern trapped excessive amounts of air during filling.
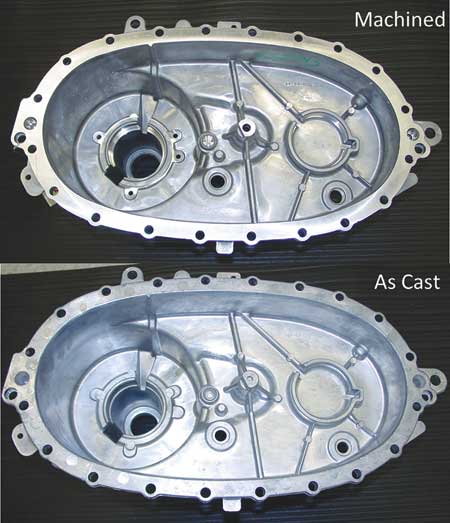
Extensive machining is performed at the customer's facility. Aallied Die Casting performs none of the secondary machining.
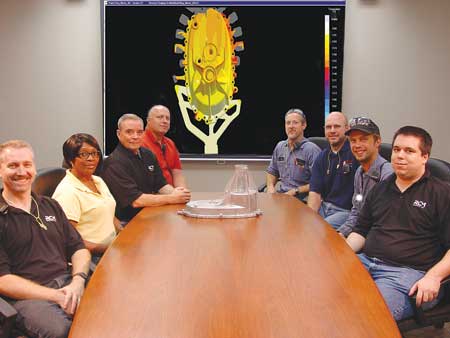
The Aallied team reviews the final simulation of the optimized casting process set-up.
An automotive transfer case housing, which is used on a full-sized four wheel drive truck, was experiencing a fallout rate of over 7% - 70,000 parts per million (PPM) - at the customer, prior to its arrival at Aallied Die Casting. The result of this was that the customer needed to leak test 100% of the castings; those that failed leak testing were impregnated. Due to the high volume of the casting, a solution was needed to reduce associated costs. Aallied Die Casting (Rutherfordton, NC), a division of RCM Industries, selected MAGMASOFT casting simulation technology to meet this challenge.
When the die arrived at Aallied Die Casting, the team was able to analyze the runner and gating system using MAGMASOFT. The simulation results showed that the filling pattern was not optimal. Numerous trapped air pockets were indicated during the fill of the casting. The Allied team went to work optimizing the gating and runner design to reduce the entrapped air pockets and achieve a more uniform frontal flow. With small changes to the runner and gating system the team was successful in reducing the trapped air indicated in the MAGMASOFT simulation.
Further optimization was achieved utilizing another tool within the MAGMASOFT software. After reviewing the air pressure result, the team noticed that the transferred design did not have adequate venting. The optimized gating system provided a more uniform frontal flow and improved the initial air pressures. However, uniform flow alone was not sufficient to eliminate the high air pressures in the die cavity, so properly placed chill vents were added to correct this issue.
All of this optimization allowed Aallied to eliminate the need for the squeeze pins, which were present in the previous die caster's design. "This reduces the complexity of the tool," said an Aallied spokesperson. "It also reduces the complexity of the process, making it more robust and reliable. The improved robustness is clearly shown in the resulting reduction in fallout."
After implementing all of these design changes, Aallied reported a significant improvement in casting quality. "The customer was able to eliminate the 100% leak testing and impregnation," said the spokesperson. "This resulted in cost and time savings for the customer. The fallout at the customer now currently stands at 0.015% (157 PPM) over the last six months of production. This represents a total of approximately 21 defective parts out of over 130,000 shipped castings. This is even more impressive considering that the part is also heavily machined by the customer. There is no secondary processing, no machining, no 100% x-ray and no 100% leak testing performed at Aallied.
"Continuous improvements drive designs and processes at Aallied Die Casting," said the spokesperson. "We strive to produce the best possible product at the best possible cost."
The Aallied team has been using MAGMASOFT products for 16 years and utilizes this valuable engineering tool on every project they undertake. By working together with their multi-disciplinary team they are able to include all of the parameters that they use in the real world, allowing them to have the utmost confidence that the results are as close to optimal as possible.
For more information contact:
MAGMA Foundry Technologies Inc.
10 N. Martingale Road, Suite 425
Schaumburg, IL 60173
847-969-1001
info@magmasoft.com
www.magmasoft.com