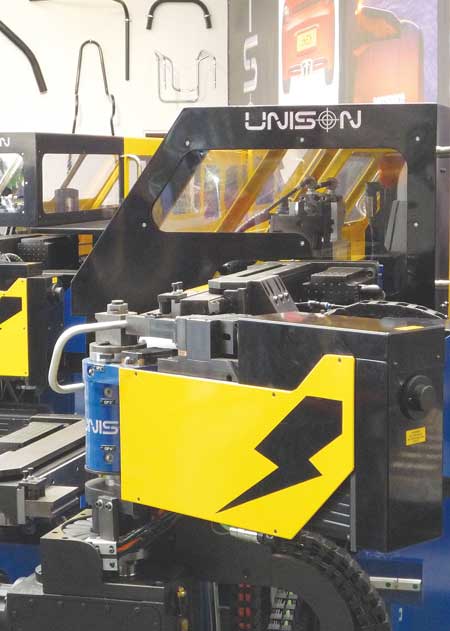
Unison will be demonstrating techniques for increasing the productivity of tubular parts fabrication.
Unison will be demonstrating techniques for increasing the productivity of tubular parts fabrication. Throughout the show, users will be able to see demonstrations on an all-electric Unison machine capable of bending tubes and pipes up to 3.5" in diameter. Unison will be part of Horn Machine Tools' display.
"Unison employs numerous advanced techniques to help manufacturers to increase throughput and quality, and eliminate the potential for errors and scrap," said a company spokesperson. "One of the techniques is a quick-change tooling system that speeds tooling changeovers. Covering all of the tooling components on the machine, it includes barcode identification to verify the changeover process. A fully validated, error-free changeover from manufacturing one good part to another can be accomplished in less than three minutes, for instance. The system is ideal for companies producing high value-added tubular parts, enabling expensive early-stage errors to be eliminated from the manufacturing process, and is of benefit for companies that manufacture parts to demand and in small batches.
"Another new advantage is a range of mechanical architecture and control software improvements that Unison has implemented to optimize tubular part fabrication times. These reduce the time required for intermediate handling and movement of the tooling that the machine performs before and after a bend by as much as 40%. As there might be four or five auxiliary movements for each bending move, as well as changes of tooling dies, these savings can add up to very large productivity gains - particularly for companies fabricating parts with multiple bends. This speed gain is complemented by Unison technical support, which helps clients to optimize their bending programs by employing techniques such as moving several machine axes in parallel. Automatic collision checking software is also available to help with this process."
"All-electric bending technology has come to dominate the tube bending industry, and is making significant inroads into pipe bending markets - with machines now available for diameters up to 8 inches," said Unison's Jim Saynor. "Most users now understand that all-electric tube benders offer major advantages over hydraulically-powered machines, in terms of automatic and repeatable set up, and right-first-time/scrap-free production. However, the benefits of such a software-controlled architecture extend much further. They allow users to simulate offline to find the most efficient way to make parts, for example, and reduce the cycle times for parts by optimizing bending programs, plus many other benefits."
Visitors to Unison's stand will be able to sign up for an educational tour demonstrating the productivity gains that can be made using servomotor-controlled tube bending. Unison will take attendees to see how real-world users employ the precision bending technology - with a choice of applications including aerospace, automotive, subcontract manufacturing, shipbuilding, and oil and gas equipment manufacturing.
For more information contact:
Horn Machine Tools
Unison North America
40473 Brickyard Drive
Madera, CA 93638
559-431-4131
sales@hornmachinetools.com
www.hornmachinetools.com
FABTECH Booth #S-3961