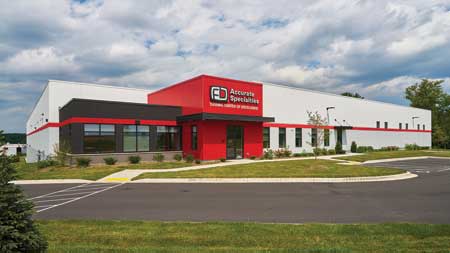
Accurate Specialties' new, ultra-modern and ITAR registered Turning Center of Excellence, strategically located in America's heartland, is tailor-made to help shore up the supply chain for precision parts that are hard to make and in short supply.
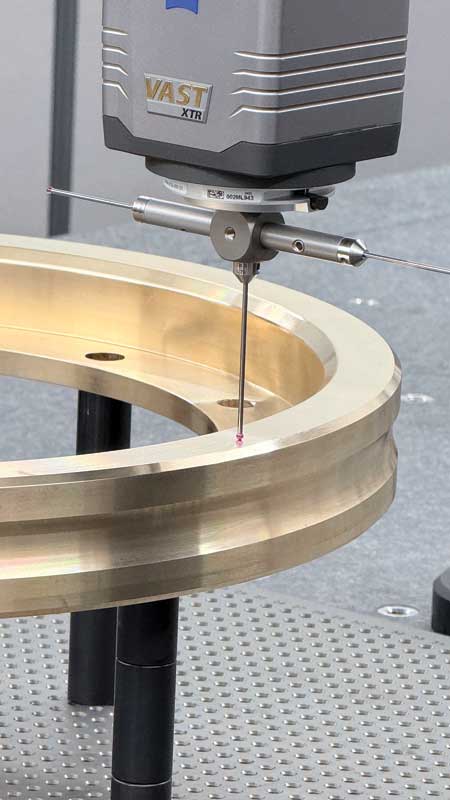
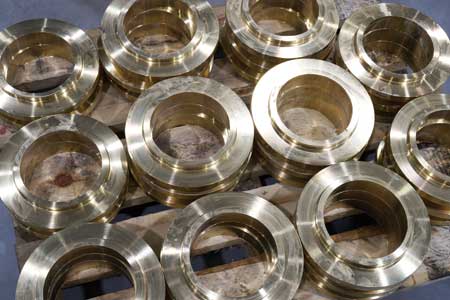
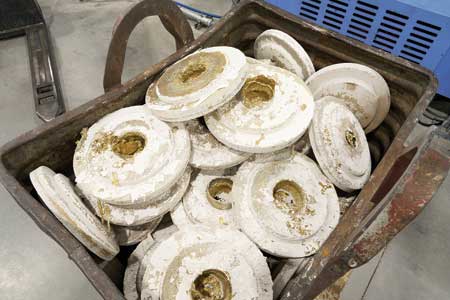
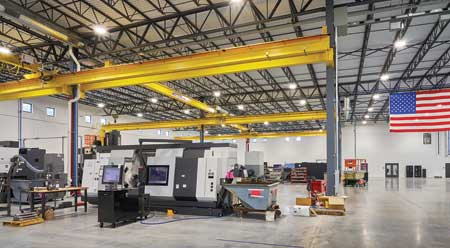
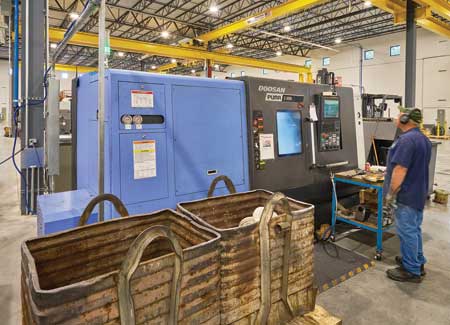
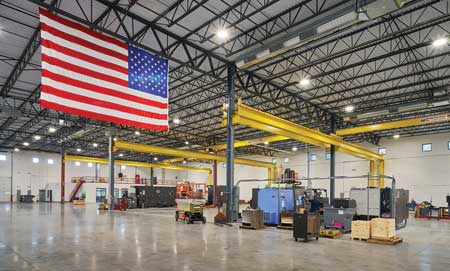
Fisher Barton's Accurate Specialties division, a Waukesha, WI-based producer of bronze gear blanks used for power transmission, agricultural applications, shipbuilding and military applications, has announced its new Turning Center of Excellence. This 56,000 sq. ft., climate-controlled factory offers complete production of high-precision, low-volume or high-volume components-especially parts that are increasingly hard to find, difficult to make and in particularly high demand.
"Cylindrical parts made from tough-to-machine exotic metals and alloys come in all shapes and sizes, from screw-size to 6-foot casting, for everything from seals for submarines to shafts for snowblowers, lawnmowers, to elevators, in industries as varied as food processing equipment, military applications, commercial, oil discovery and agricultural," said Jim Scott, COO, Accurate Specialties. "The common denominator is their requirement for ultra-precision CNC machining centers. With supply chains stretched thin, and manufacturers trying to keep pace with older, slower processes and equipment, it is no wonder Fisher Barton ear-marked a significant part of its multiyear, $20 million capital investment programs for this new ITAR-registered facility."
A spokesperson added: "Manufacturers, particularly in the aerospace and defense market sectors, are increasingly seeking to outsource to more reliable partners with ultra-modern manufacturing resources and experience. Fisher Barton project engineers are partnering with these OEMs to offer a better solution than can be produced either in-house or outsourced to their traditional suppliers. Where the need exists, Fisher Barton will even produce parts to specification to help improve designs and validate manufacturability."
Case in point: four-day turnaround on a large (14" diameter), critically important bearing seal component for the next generation of U.S. Navy submarines, machined complete from exotic material meant to last for 50 years in the harshest undersea environments. The facility's ITAR certification, investment in late-model, large-capacity turning centers and CMM inspection on-site to meet the military's high qualification requirements all contributed to this first test part "passing with flying colors," and the order for large-scale production, according to Lee Herman, Accurate Specialties' Plant Manager.
"Our Turning Center of Excellence is purpose-built to meet this critical need for single-source, start to finish production, all under one roof, of the types of parts-large and small-that are in high demand but hard to make, like this one," Herman said. "We can machine complete, inspect and even package high-precision components made from all types of even the most exotic metals and alloys-whether small-diameter, high-volume orders or a one-off shaft with a 2 m diameter or 20 ft. length-all in a fraction of the time these customers have come to expect from their traditional sources."
The new facility features a Tsune CNC saw with automatic bar feeding to cut any size bar stock down to size; G&L VTC 2500 for parts with diameters as large as 100"; Okuma and DN Solutions turning centers, a Multus multi-axis machining center offering a wide range of close-tolerance machining operations, speeds and capacity options; Swiss-type machines for the complete machining of smaller parts in high volumes; and a temperature-controlled quality room. The quality room features a large-capacity Zeiss CMM capable of sub-micron measurement of finished parts and their features, as well as a new 3D imaging system that speeds inspection of smaller parts.
"Raw material comes in on one truck and a week or two later departs as a completely inspected and finished component ready for installation into truck or tractor, marine vessel or military vehicle," said Herman. "We have designed this facility for maximum throughput, minimum manpower and processes that are always under tight control. Almost every machine has on-board probing and inspection, so we can dial in tolerances and confirm that we are within the tightest specs at every step of the process."
The new Turning Center and its affiliation with the Fisher Barton global organization offers further added value, according the spokesperson: "At its core, Fisher Barton is a metallurgical innovation partner. Its engineers understand the behavior of material and the application of their proprietary heat treating and surface engineering solutions that reimagine a component's lifespan. These capabilities offer more than just a foundry or typical machine shop. For example, through partnership with another Fisher Barton division, TST Engineered Coating Solution, thermal spray coatings can be applied to add considerable value by extending shaft life, reducing corrosion, minimizing material costs and solving problems like leaking due to shaft wear from seals with imbedded abrasive particles. Advanced wear resistant materials, including hard metals, carbides and metal oxide ceramics, are engineered into highly resistant coatings for critical shaft sealing locations. These advanced coatings can also be used to greatly reduce material costs. In one recent application, Accurate Specialties devised a solution that enabled the customer to replace the expensive carbide material used for its shaft components with a much less expensive steel alloy but coated to deliver the wear resistance and durability of its carbide predecessor."
The Turning Center of Excellence has access to all the R&D resources made available through the Fisher Barton Technology Center, located in nearby Watertown, WI. In this way, it can address design and material deficiencies and explore ways to improve manufacturability and performance in the field. For example, if a customer's worm drive experiencing premature wear or failure, a Zeiss scanning electron microscope can perform a sophisticated analysis of fracture surfaces and microstructures, or a Keyence laser scanning microscope can analyze the material in 3D. Abrasion and erosion testing, fatigue testing can be performed as well-all with the ultimate goal of finding and applying the ideal alloys, coatings and processes.
Authored by Lee Herman, General Manager, Accurate Specialties, a Division of Fisher Barton
For more information contact:
Accurate Specialties
560 Bluemound Road
Waukesha, WI 53188
262-547-5450
www.fisherbarton.com