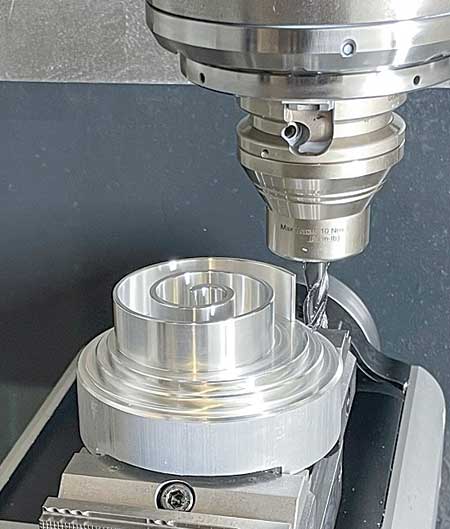
A standard milling machine with a supplementary pL LEHMANN precision rotary table offers higher precision at smaller investment costs, pL LEHMANN reported.
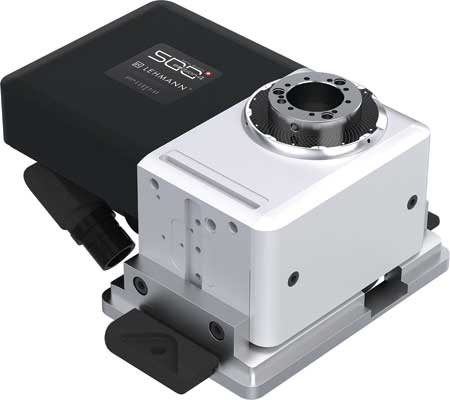
PGD A-510v rotary table from pL LEHMANN has a backlash-free, preloaded gear unit and advanced bearing technology for high precision.
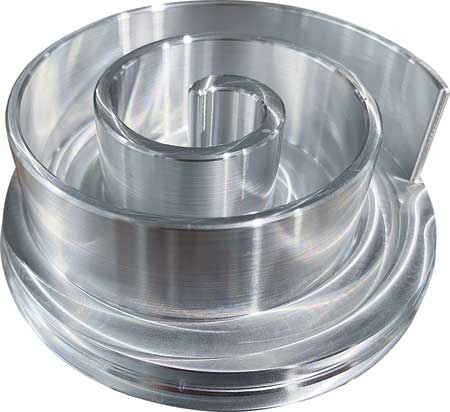
Scroll compressors mainly consist of two functional components with interlocking spirals that have to be machined with high precision.
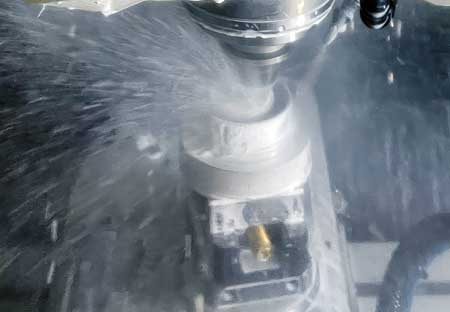
The roto-milling process offered by pL LEHMANN is an affordable scroll machining process that can be used to achieve high precision and surface quality, the company reported.
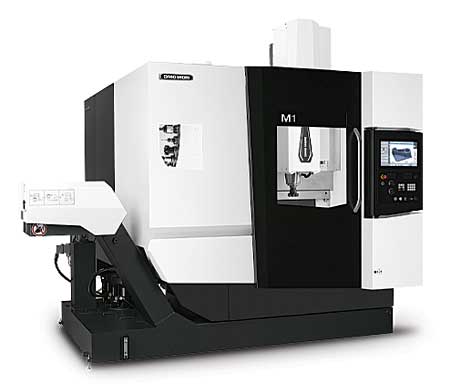
"The DMG MORI M1 VMC with a pL LEHMANN precision rotary table is an ideal solution for scroll cutting in rotomilling," said a pL LEHMANN spokesperson.
Scroll compressor manufacturers serve a promising market-and with the right equipment, this type of machining is worthwhile, reported pL LEHMANN, a Swiss manufacturer of CNC rotary tables. The company recommends a rotomilling process it developed as an efficient, precise production solution. The only prerequisite that needs to be met is a standard milling center and a supplementary pL LEHMANN precision rotary table.
"According to reliable forecasts, the demand for scroll compressors will increase substantially over the next few years," said a company spokesperson. "After all, these compact, powerful compressors increase the pressure and temperature of the coolant in the compressors in cooling systems, air conditioning systems and heat pumps. Another growing area of application is hybrid and electric vehicles in which they are used to cool electric motors, batteries and the interior of the vehicle."
This scroll compressor mainly consists of two functional components with interlocking spirals. While one part is stationary, the other (also known as the orbit) moves eccentrically along a circular path. In the process, the gaseous medium is increasingly compressed inwards. To help ensure a high level of efficiency, both spirals must maintain narrow axial and radial gaps as they must not be in contact with each other when assembled. This means that the tolerance specifications for the shape and perpendicularity of the spirals are sometimes less than 20 µm. The surface qualities are also demanding. The Rz values should be in a range of less than 10 µm.
Currently, these scroll components are milled on one- or two-spindle machining centers that usually have 4 or 5 axes, and the spiral is generated via interpolation of the X and Y axes.
"The disadvantage of the latter is that the milling spindle has to pass through reversal points at which an axis changes the movement direction-associated with physical inaccuracies of a few micrometers," said the spokesperson.
Interpolation of Rotary and Linear Axes
As an alternative, pL LEHMANN offers the rotomilling process developed for scroll machining. The core element is a highly precise, 1- or 2-axis pL CNC rotary table, which is placed on a vertical, 3-axis machining center on the machine table. It enables machining in which the linear X-axis and the rotary axis of the CNC rotary table are interpolated.
"This results in several advantages over circular interpolation: there is no quadrant transition and the machining process is perfectly controllable," said the spokesperson. "In addition, forces are not deflected to the tool, which results in excellent shape accuracy over the entire length and height of the spiral. The base of the scroll can also be machined with high precision."
The Precision Rotary Table Makes All the Difference
The high precision of the CNC rotary table is crucial in regards to concentricity, axial and wobble accuracy in conjunction with a preloaded, backlash-free gear unit with enhanced synchronization. All this comes standard with pL LEHMANN CNC rotary tables and can be bolstered even more with optional extras.
"We are not aware of any product from a competitor that meets the stringent requirements," said the spokesperson. "This is because the specified accuracies should lie within a tolerance range of 2 µm to 3 µm-which pL LEHMANN guarantees due to the high level of bearing technology and the backlash-free, preloaded gearbox. To achieve this, the bearing points are machined directly into the spindle and housing section in a production process optimized across thousands and thousands of rotary tables; in the smaller sizes, this even includes the gear wheel on the spindle side."
Measurements Confirm the High Quality
To verify the quality of rotomilling machining, pL LEHMANN milled a series of scroll components on a DMG MORI M1 machining center using circular interpolation and roto-milling. For the latter machining process, the machining center was supplemented with a pL T1-510520 TAP2 rotary table. While a step of 8 µm was measured on the quadrant transition of the circular-interpolated milled part, the rotomilling component remained step-free. The line shape accuracy was also better over the entire spiral height, the company reported.
To ensure that the process capability of scroll machining was evaluated by a neutral body, pL LEHMANN commissioned the accredited measuring lab Units Mittelland AG. The company performed SPC machining of 20 scrolls, which were produced in various series on the DMG MORI M1 BAZ with EA-510 pL rotary table. First, meaningful measuring point and line heights were determined to obtain cpk values for line shape, flatness, straightness, parallelism and perpendicularity. According to the report, the cpk values were consistently (in some cases, by a multiple) above the value cpk=1.33, which indicates that the process is highly unlikely to exceed values in the product specifications, and is therefore of high quality. Deviations from the respective nominal dimension are usually less than 0.01 mm. The measurement reports are available from pL LEHMANN.
More Efficient and Scalable, for Aluminum or Cast Scroll
In an investment comparison, pL LEHMANN compared finishing of a scroll component (orbit) on a 5-axis double spindle machine (circular-interpolated) with rotomilling on a 3-axis vertical milling center with 2-axis pL rotary table.
In the first case, the finishing cycle for two components took between 71 and 91 seconds. This is in light of the fact that during finishing, i.e., when maximum accuracies need to be achieved, double-spindle machining cannot be performed according to statements from a variety of market participants. This means that finishing can only be carried out with a tool spindle, which is why only one workpiece at a time can be finished.
In rotomilling, finishing of a component took 76 seconds. In other words, in regards to finishing, there are hardly any significant differences on the time axis. However, it is interesting to take a look at the investment costs. While a two-spindle, 4- or 5-axis machining center costs around $577,000, the manufacturer only has to pay between $126,000 and $136,000 for a 3-axis milling machine with pL rotary table. For the investment of around $524,000, the manufacturer would get four standard machines equipped for scroll machining.
The material used in the tests was the 4032-T6 aluminum alloy, which is currently used for scrolls. But pL LEHMANN also has an eye on future changes. A material change is required as new coolant standards will be in force starting in 2030. Therefore, the Swiss rotary table manufacturers have already run the tests with the new G70 casting material and achieved excellent results with rotomilling, the company reported.
Quality Advantages Through Cooperation with Tool Manufacturers
Regarding machining quality, pL LEHMANN collaborated with Mapal and Gühring to optimize the rotomilling process. After all, a high-quality machining result requires optimum coordination between the machine, rotary table, tool and machining strategy. Using special tools from both of these manufacturers, pL LEHMANN reported that it exceeded machining results on the aforementioned 5-axis high-end centers in regards to shape and surface quality, with comparable cycle times and at much lower unit costs.
A Retrofittable and Easily Scalable Process
Another advantage of standard machines equipped with a precision rotary table is that the components are usually in stock. In addition, the production capacity can be expanded as needed and can be scaled much more easily and precisely. Value retention is also high because standard machines are usually much easier to sell than highly specialized, expensive centers.
When selecting a milling machine, the manufacturing shop can choose according to its preferences. pL LEHMANN CNC rotary tables are now used on over 200 different machine brands and over 1,000 different machine models. The result is broad knowledge of the requirements for integrating them into all known CNC control systems (FANUC, Siemens, HEIDENHAIN, Haas, WinMax, Mitsubishi, Brother, etc.) for new machines and for retrofits.
For more information contact:
pL LEHMANN America Inc.
4420 Anson Blvd
Whitestown, IN 46075
463-946-0002
www.us-pl-lehmann.net