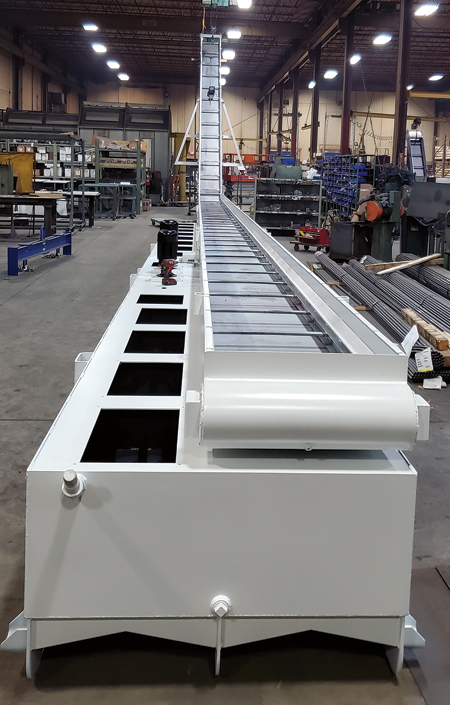
For a giant gantry machine making parts for a huge space telescope, Jorgensen designed a chip handling solution that uses two 133' long horizontal conveyors that deposit chips and stringers to a 104' cross conveyor, which transports the chips 20' up and out of the building where they are collected for recycling.
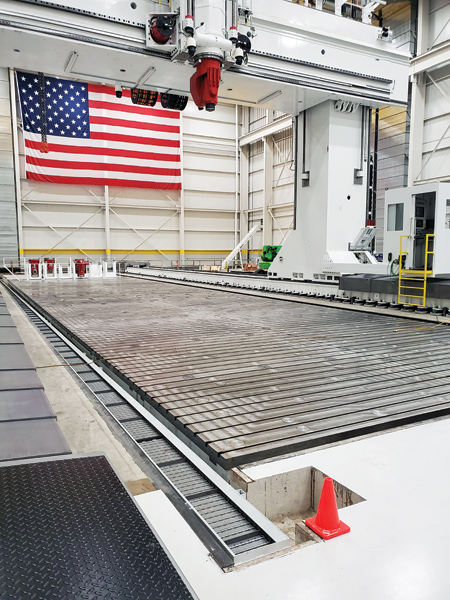
A massive 5-axis gantry machine works 12 hours per day, six days a week machining huge space telescope components. The process generates mountains of chips that are managed by a special Jorgensen chip conveyor system.
With seven mirrors and almost 4,000 sq. ft. of light collection area, the Giant Magellan Telescope (GMT) will have 10x the resolving power of the Hubble Space Telescope and 4x more resolution than the James Webb Space Telescope. Its supporting structure and mount will stand 12 stories tall and weigh 2,100 metric tons.
A project years in the making and the progeny of a sweeping consortium of international academic, scientific, private and government organizations, the GMT will be the world's largest Gregorian optical-infrared telescope ever built. It is anticipated to be fully operational in the late 2020s.
One can only imagine the amount of chips generated when machining its huge components on a giant gantry 5-axis multitasking machine. This machine runs 12 hours per day, six days a week milling GMT parts.
In addition to the vastness of the project, logistics require that a demanding mix of chips-including cast iron, steel, titanium and alloys-be filtered and evacuated. This process requires chips to travel up and out of the central manufacturing floor, through a wall and into another building.
Wisconsin-based Jorgensen Conveyor and Filtration Solutions was chosen by the project's prime manufacturer, Ingersoll Machine Tools, to find a solution and make it work in a very tight footprint. The massive MasterMill machine took up most of the available space.
"That was one of the big challenges," said Mike Weckerle, Jorgensen OEM Sales Manager. "The Ingersoll machine took up all the space, so the conveyor system ran out of real estate."
When they received Ingersoll's initial call, Jorgensen engineers wasted no time designing a conveyor and filtering solution that would move chips and filter to 25-micron clarity for a machine the size of a football field that flushes cutting fluid at the rate of 30 to 40 gallons per minute.
"Ingersoll knows us from previous jobs, and they reached out for a quote in 2021," said Dustin Krueger, Jorgensen Director of Engineering. "We jumped right in on the design."
"We have had a long-standing relationship for more than 40 years," said Ingersoll CEO Dr. Jeffrey Ahrstrom. "They are a great a partner to work with."
To transport the mountain of chips and river of cutting fluid generated by machining on such a massive scale, Jorgensen designed a solution that incorporated two 133' long horizontal conveyors to run the MasterMill's bed length. Those conveyors deposit chips and stringers to a 104' cross conveyor that transports the chips 20' up and out of the building, where they are collected for recycling. The cross conveyor sits atop a 261-cu. ft. coolant tank equipped with a self-cleaning gravity filter and electronic coolant monitoring system to minimize maintenance. As in all machining applications and especially on one of this magnitude, clean coolant is essential.
"A reliable coolant system is critical to this manufacturing process," Ahrstrom said. "It provides us with better performance, longer tool life and lower operating expenses."
The Jorgensen team worked for three months to design and build the system in its own facility. Upon approval by Ingersoll, they sent two technicians to Ingersoll's 40,000-sq.-ft. dedicated technical center and manufacturing facility in Rockford, IL, for the four-day installation. Overall, the Jorgensen design-build-installation effort took about a year to complete.
In addition to machining parts for the GMT, the facility will manufacture components for the defense, commercial and transportation sectors.
Jorgensen usually completes two to three considerably large projects each year. "This was all in our wheelhouse," Weckerle said. "We do this every day-designing and manufacturing a project specifically to a large machine in a tight window. It is what we do."
With so much on the line in so many areas, Ingersoll needed to rely on a partner it could trust. "They always come through for us on these large applications," Ahrstrom said.
For more information contact:
Jorgensen Conveyors & Filtration Solutions
10303 N Baehr Road
Mequon, WI 53092
262-242-3089 / 800-325-7705
info@jorgensenconveyors.com
www.jorgensenconveyors.com
Ingersoll Machine Tools Inc.
707 Fulton Ave.
Rockford, IL 61103
815-987-6000
info@ingersoll.com
www.ingersoll.com
Giant Magellan Telescope
www.giantmagellan.org