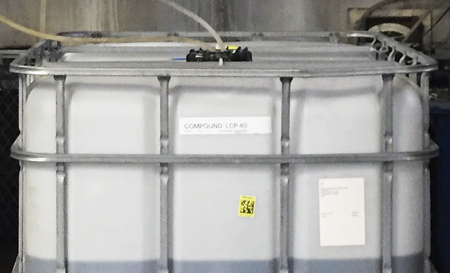
COMPOUND LCP 60 is a liquid cleaner-phosphatizing agent. This low-foaming detergent with phosphates and activators forms an iron phosphate conversion coating at room temperature.
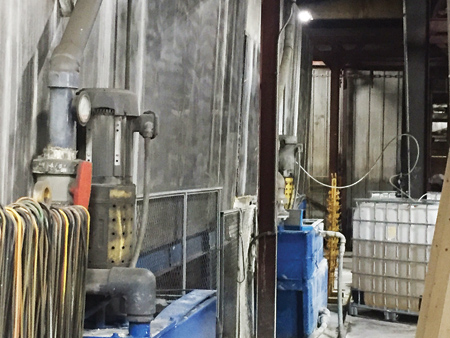
All parts at Midstate are rigorously cleaned with Madison Chemical solutions before painting to ensure good adhesion after powdering.
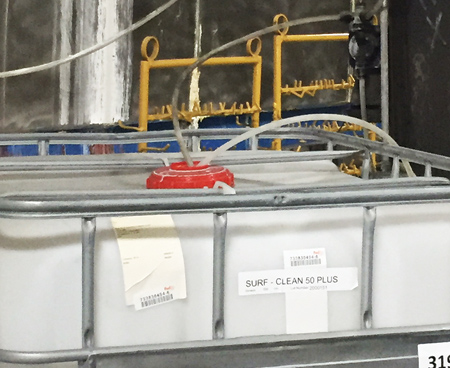
SURF-CLEAN 50 PLUS, a liquid, moderately alkaline detergent at a 5% concentration in a 100° solution. This is introduced through an automatic metering system and has immediate solubility. It removes most typical fabricating soils, including cutting oils and chips leftover from the machining process.
Not every manufacturing project fits into a nice, neat mold of standard procedure. About 95% of Midstate Manufacturing Company's production is standard, and can flow through the 150,000 sq. ft. plant smoothly due to manufacturing systems and processes that have been fine-tuned for 43 years. One step in the process is a continuous five-stage wash system prior to being powder coated.
MidState's products range from a 16-gauge mild steel fastener to a 5" thick machined stainless component. All parts are rigorously cleaned before painting to ensure good adhesion after powdering. MidState works with everything from thin sheet metal to 6" thick steel.
However, some new parts and projects do not fit as smoothly into the cleaning process as others. So, when new production challenges arise that threaten to disrupt their manufacturing process-whether it is a new material, something that needs to be wet-painted or a project that is too large to fit into the wash system-Midstate's Plant Manager Allen Pickrel turns to his cleaning chemical supplier.
When Pickrel is faced with the unknown, he begins with the end in mind. He first determines the best way to make sure the part gets good paint adhesion-whether that is wet or powder coating-and cure to their products. He mulls over his options, plans out a tentative strategy and then calls Dicky Kammer, a Technical Sales Representative at Madison Chemical. Madison Chemical's team of chemists and technical experts help concoct the cleaning cocktail that is just right for the job, helping turn Midstate's challenge into a business solution.
One particularly challenging product was a large container with mold growing inside that had to be cleaned before being coated with paint. Since the part was too big to fit into their five-stage wash system, Midstate called Kammer to come up with a way to effectively clean the container while also prepping it for paint adhesion. After their rendezvous Midstate had a cleaning solution and application method: a Hotsy power washer.
But Madison Chemical's role with Midstate Manufacturing does not end there. In fact, it does not end at all. The two companies have been working together since 1996. Kammer stops by Midstate Manufacturing at least once a week to check on chemical levels, test chemical stability, take samples for evaluation and more. After his visits, Midstate receives an emailed report from Kammer summarizing his conclusions and recommendations.
In-between special projects, Midstate utilizes alkaline and phosphate cleaners from Madison Chemical in its continuous five-stage wash system. The first stage uses SURF-CLEAN 50 PLUS, a liquid, moderately alkaline detergent at a 5% concentration in a 100° solution. This is introduced through an automatic metering system and has immediate solubility. It removes most typical fabricating soils, including cutting oils and chips leftover from the machining process.
After a thorough water rinse, COMPOUND LCP-60, a liquid cleaner-phosphatizing agent, is introduced into the 100° tank at a dilution of 2%. This low-foaming detergent with phosphates and activators forms an iron phosphate conversion coating at room temperature.
FLOW-MAX Technology, which is added to the COMPOUND LCP-60, removes existing scale deposits, allows better heat transfer and reduces nozzle plugging, reducing maintenance downtime and poor performance due to clogged nozzles and sludge deposits.
After another water rinse, the parts are immersed in a final sealing rinse solution with SurfTreat SEAL 9 at a concentration of 0.5%. Parts stay in the 100° solution for approximately 30 seconds. This promotes adhesion between paint and conversion coating and provides corrosion resistance for the painted surface.
After exiting the 5-stage wash system, parts travel through a dry-off oven. After that, it is off to a powder coating booth before parts go through the oven.
"While this process works well for 90-95% of the components that MidState manufactures, Pickrel is grateful that he has a go-to source for help on the specials, no matter what the size of the part or the material. The customer service and expertise of Madison Chemical not only help them with the new and challenging projects but with the day to day operations, allowing Pickrel and his team to deliver quality products time and time again, year after year," said a spokesperson.
Madison Chemical is a chemical formulator that provides cleaning, sanitation, maintenance and surface preparation products for metalworking, industrial maintenance, transportation and other industries.
For more information contact:
Midstate Manufacturing Company
750 West Third Street
Galesburg, IL 61401
309-342-9555
www.midstate-mfg.com
Madison Chemical Co., Inc.
3141 Clifty Drive
Madison, IN, 47250
812-273-6000
solutions@madchem.com
www.madchem.com