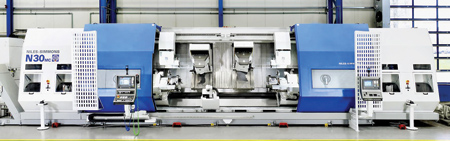
Turning-milling center N30 MC with CLOSED-DOOR-MACHINING manufacturing concept
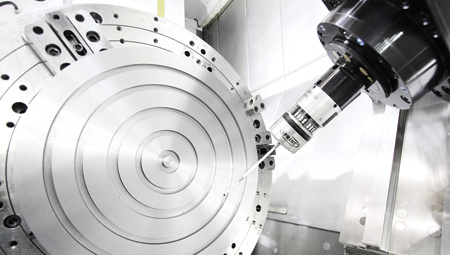
Renishaw Sprint measuring sensor
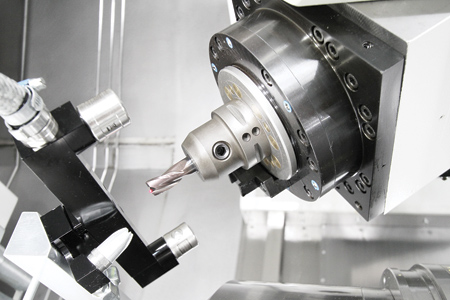
Integrated tool measurement with laser
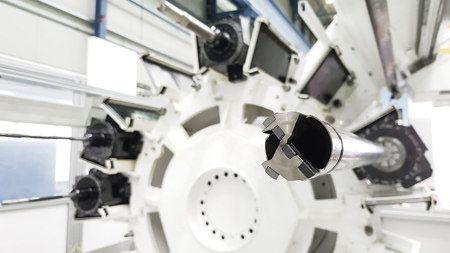
Additional boring bar magazine for complex internal machining
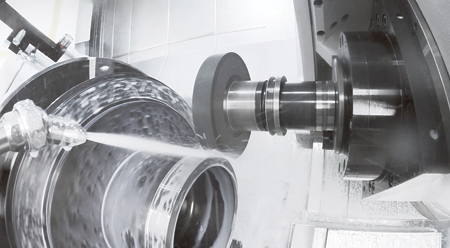
Process integration: Grinding including dressing unit and specific process software
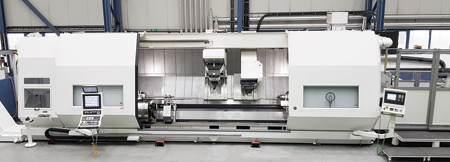
N30 MC including boring bar magazine and up to 32 NC axes
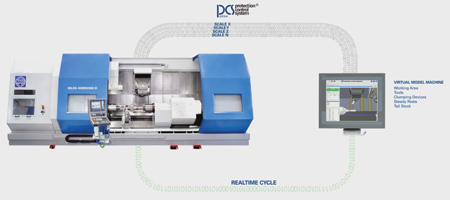
Software module PCS and VCS for high process security
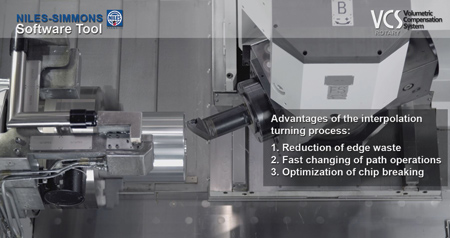
NILES-SIMMONS has developed a "CLOSED-DOOR-MACHINING" concept to meet the ever-increasing requirements for the manufacturing of complex, high-precision parts and components, initially for the aviation industry.
This concept allows the complete machining of parts in one continuous process within one machine and without any operator interventions. It is applicable for various part types which, historically, had to be manufactured in several process steps on various machines.
When using the CLOSED-DOOR-MACHINING concept, a raw part is clamped into the machine and after several fully-automatic re-clamping and re-chucking procedures, it can be removed as a completely finished part. The machining runs entirely uninterrupted and, depending on the part complexity, shifts can be overlapped a number of times throughout the cycle.
Since the process runs fully automated, the time associated with labor-intensive part handling procedures is removed and lay down spaces can be reduced. Since fewer machines are required, less operator intervention is necessary.
By integrating all the necessary technology-such as turning, milling, drilling, deep-hole drilling, boring, bottle boring thread cutting, gear hobbing, power skiving and grinding-into one machine, there is no need to use process-specific single machines, which in the long term contributes to more cost-efficient production.
For the implementation of the concept, NILES-SIMMONS introduced several new machining and measuring technologies engineered to make it possible to achieve high accuracies of <5µm in a process-reliable way by the use of scanned part measuring through Renishaw Sprint measuring sensor and automatic tool compensation after the measurement cut. As well as Sprint there are also other various touch measuring sensors such as RMP60 or RMP600 fitted to carry out other measurement tasks.
At the same time, the measurement of all necessary tools also takes place, again fully automated within the machine using a touch measuring system for fixed tools and an optic measuring system (laser) for rotationally symmetric tools.
In order to accommodate the large number of tools required, it is possible to configure two tool magazines headstock- and tailstock-side with a capacity of up to 144 tools, each to service the multi-axes turning-milling unit. The tools can be exchanged automatically into the working area from either side.
Alternatively, for specific machining tasks, an additional magazine can be applied for the counter spindle- or tailstock-sided boring bar slide. This long tool magazine has a maximum of 16 positions for long tool cartridges. These long tools are also exchanged automatically into the second slide.
The long tools with up to 2 m in length can be operated with high coolant pressure of up to 300 bar and with a high flow rate of up to 150 l/min. "Consequently, any deep-hole drilling requirement can be achieved as part of an extremely stable and reliable process," said the spokesperson. The temperature-controlled coolant can be programmed with both pressure- or volume-controlled and monitored via sensors.
For surface optimization of the parts, it is also possible to integrate grinding operations in the machine. The grinding wheel can be exchanged, measured and dressed fully automated. For sparking, there are also sensors available. The coolant, which needs to be positioned close to the process, is controlled and positioned by a separate, programmable NC-axis.
The fully equipped machine with turning-milling unit, boring bar slide, turret (bottom), main and counter spindle as well as steady rests and tool change units can be configured with up to 32 NC axes. "Due to this complexity, a CAD/CAM system with integrated post-processor is essential," said the spokesperson.
Furthermore, a liquid-cooled concrete machine bed is used to achieve higher temperature stability and to maintain required accuracies despite variation of temperature. The machining centers are also equipped with damping and vibration reducing components such as FEM optimized slide geometry, hydraulic clamped components of the part axes, damping surfaces in machining direction and roller guides of the machining axes in size 45/55.
To facilitate clear and easy operation, the control is a Siemens OP 19 panel with additional touchscreen for process monitoring.
The process security within the CLOSED-DOOR-MACHINING concept is enhanced through NILES-SIMMONS' comprehensive software modules driven by Industry 4.0, such as Volumetric Compensation Software, spindle modulation, axis compensation, tool breakage and drive monitoring.
For more information contact:
Bill Archer, Sales Manager USA
NILES-SIMMONS-HEGENSCHEIDT
513-519-2079
b.archer@nshgroup.com
www.niles-simmons.de