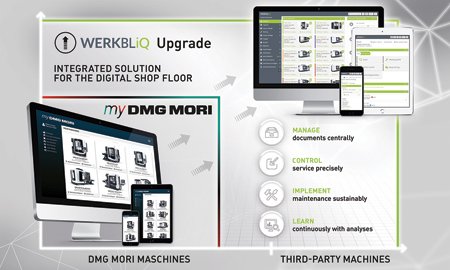
The service and maintenance platform WERKBLiQ is an integral solution for the shop floor-from DMG MORI machines to third-party machines.

WERKBLiQ digitizes maintenance and repairs.
Maintenance processes in production are more important than ever, but some may cost valuable time and fray nerves. WERKBLiQ from DMG MORI is designed to simplify day-to-day work in rapid traverse so customers can keep an efficient grip on their service-internally and externally.
"WERKBLiQ allows machine operators to visualize all structures and processes of the maintenance organization digitally and independently of manufacturer. This also includes the internal and external interaction channels and the entire contract and documentation management," explained Dr. Tim Busse, Managing Director of WERKBLiQ.
As a consequence, WERKBLiQ optimizes the entire service process for all machines and equipment with quantifiable benefits. Even machines without a network connection can be integrated and managed in WERKBLiQ via mobile end devices. According to the company, incorporation into existing IT systems can be effected quickly and without any great effort on the shop floor. Implementation takes just 48 hours on average.
Employees record and document all activities and processes on the machinery during their day-to-day work. They are supported by customizable and interactive input masks. All it takes is the press of a button to alert internal maintenance directly from the machine in the event of a breakdown and to trigger the saved service process.
my DMG MORI users can upgrade their account to WERKBLiQ. All DMG MORI machines are then transferred to WERKBLiQ, where they are integrally expanded and managed together with third-party machines and objects. The integral networking of WERKBLiQ and DMG MORI SERVICE is engineered to provide high customer benefit because all functions available in the my DMG MORI account are also part of WERKBLiQ.
Users benefit from integral functions for managing and optimally controlling the entire maintenance process, allowing full control at all times. Because individual challenges require individual solutions, a number of possible customer-specific configurations were integrated during the development of WERKBLiQ, which can then be used by each user to develop his or her own solution.
Continuous documentation and recording of data on the shop floor enable end-to-end transparency in the subsequent process. The WERKBLiQ evaluation module enables maintenance and production managers to evaluate relevant key indicators and use the results to implement continuous improvements.
For more information contact:
DMG MORI - Americas Headquarters
2400 Huntington Blvd.
Hoffman Estates, IL 60192
847-593-5400
Service Hotline:
855-DMG-MORI (364-6674)
us.dmgmori.com