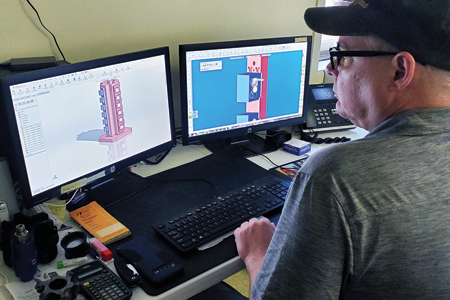
Rich Slacum, owner of Atlantic Precision Technology, reviews a tombstone with 18 workpieces in SolidWorks (left) and individual part with toolpath in GibbsCAM.
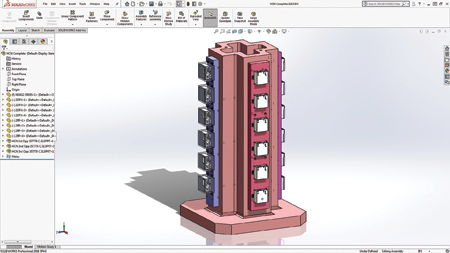
After receiving a part file in STEP format from a customer, Slacum loads the part into SolidWorks CAD, designs a fixture and populates the tombstone with workpieces in place. The tombstone is shown mounted on a pallet.
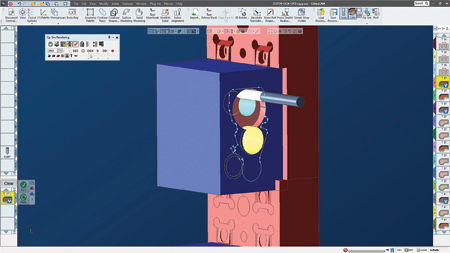
GibbsCAM screen shows initial operations on the face of a workpiece, which will become a slit changer housing for a customer.
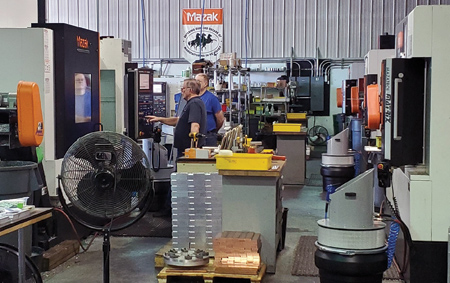
Atlantic Precision has four VMCs, one HMC, a 2-axis lathe and a 5-axis multitasking machine, all from Mazak. Here, machinists Gary Reeves and Jerzy Linda review code on a Mazatrol.
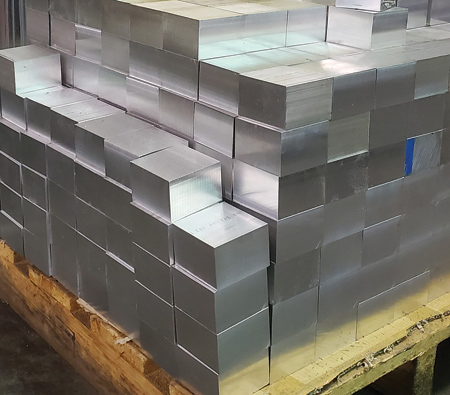
The shop cuts and prepares its own stock, such as this stack of 2"x3"x3" billets for the slit changer housing.
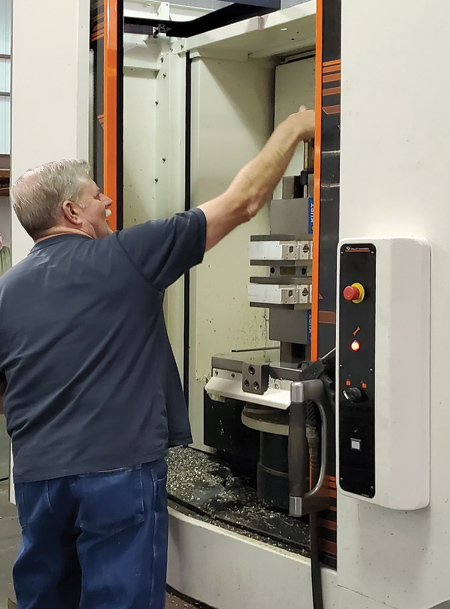
CNC Machinist Gary Reeves loads a tombstone on the back of a Mazak HMC, which is working on a tombstone on the front side.
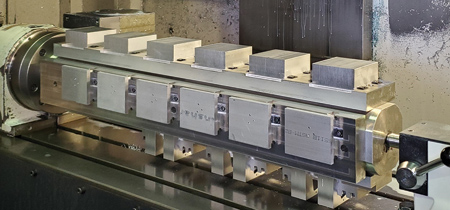
Slacum calls this configuration a "poor man's horizontal," which emulates a tombstone on a horizontal with a laterally mounted, multi-facet fixture on the trunnion of a vertical machine. He uses a similar configuration on four verticals, such as this Mazak Nexus 510C-II.
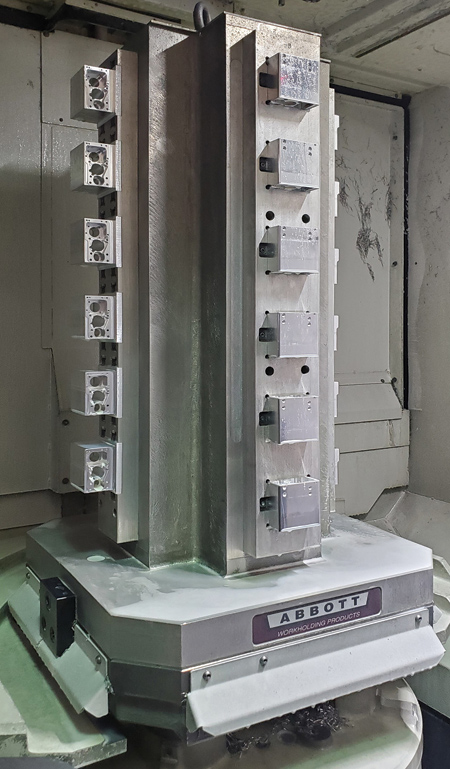
A tombstone on the Mazak HMC showing pieces in different stages of completion. At the end of each cycle, six finished parts are taken off, six new workpieces are mounted and the other 12 parts are rotated and refixtured while machining commences on another tombstone.
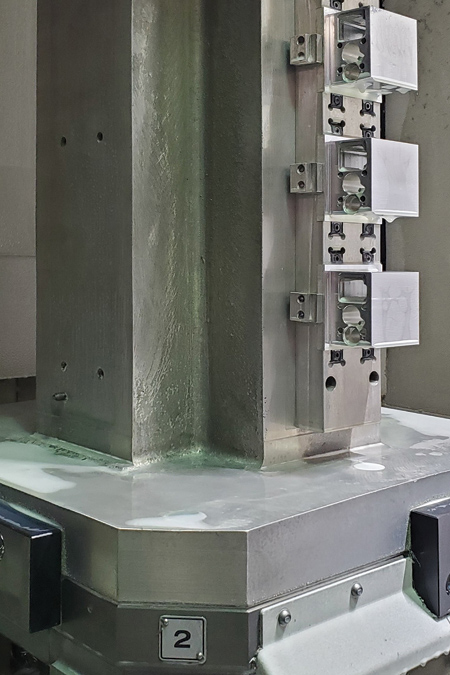
A close-up of a populated tombstone with nearly finished parts on one of three populated faces and the unused face.
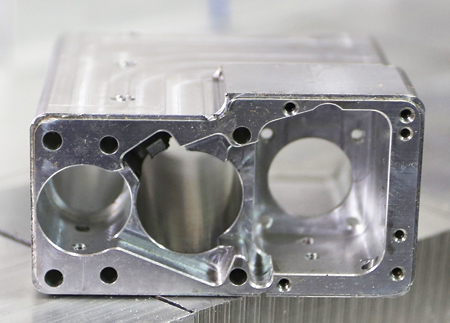
Close-up of finished housing. Slacum uses the Surface Machining GibbsCAM feature on external radii since form cutters will not blend with full 90° arc. The part is for a precision light sensing instrument, so razor-sharp edges are intentionally made into some internal features as light baffling. Razor edges reflect no light.
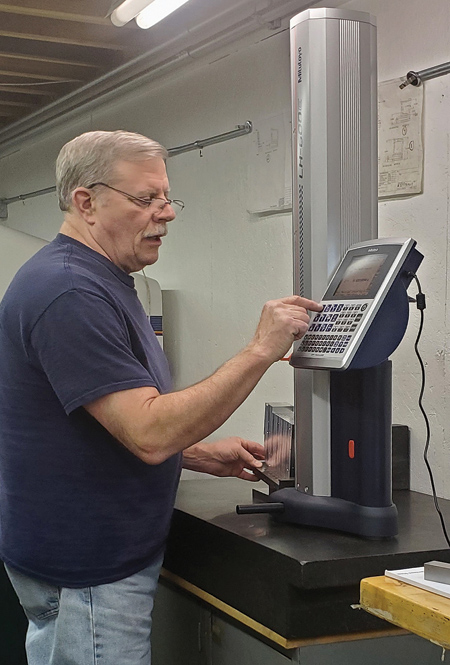
Machinist Gary Reeves inspects a finished slit changer housing.
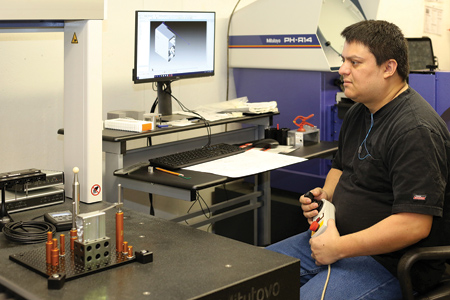
Machinist Jorge Mora-Sobrado monitors a CMM as a software program drives an automated inspection. Because many scientific instrument parts have tolerances of .0004", Atlantic Precision performs in-process batch checks.
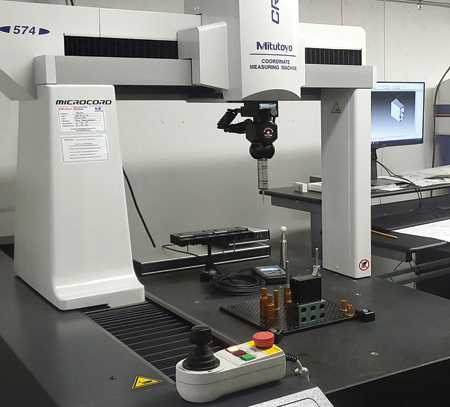
An anodized housing mounted and ready for inspection. Due to close tolerance requirements, inspection of a part from each batch of anodized parts is performed.
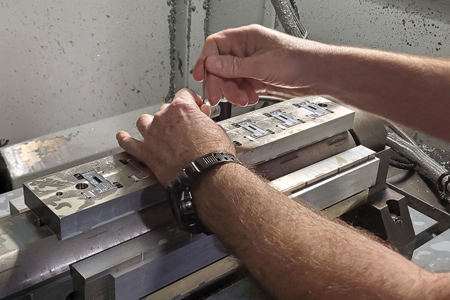
A machinist removes aluminum diode board mounts for instrument company Horiba Jobin Yvon.
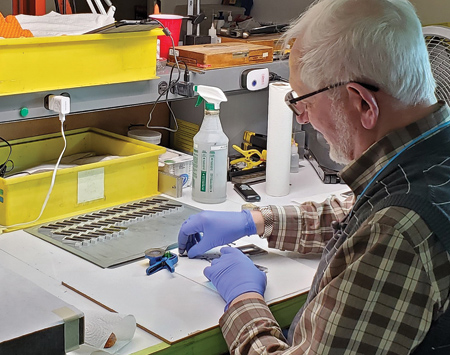
Quality Specialist Alex Boguslavskiy assembles diode board mounts, incorporating tiny parts sprayed with a total light absorbing paint (Eastern Chem-Lac Solar Black, specially formulated for applications requiring zero reflection), and then baked on at 325 °F for 30 minutes.
The probability that Rich Slacum would start his own machine shop was close to zero, until he actually did it. He had a good, stable job that he really enjoyed, working for machine tool builder, Mazak. Furthermore, his aversion to risk dampened any thoughts of a new venture. Year after year, he turned down a partnership offer from a shop owner and Mazak user. Then, in 2008, a couple years after the shop owner had sold his business, and a year when most people would never start a business, Slacum accepted the challenge.
With the country in deep recession, it was a bad time to find customers, but a good year to buy almost anything. Slacum leased space, bought a band saw and a compressor, made down payments on two Mazak machines, and opened what is now Atlantic Precision Technology, in North Brunswick, NJ.
Straight out of high school, Slacum went to work running Acme Gridley screw machines. From there, he went to a Revlon subsidiary, making cosmetics machines. During his five years there, the company paid for his apprenticeship, which included night school to learn mathematics, drafting, metalworking and AutoCAD.
A layoff led Slacum to Mazak, where he spent 12 years as an applications engineer providing pre-sales support, training customers and helping with turn-key deliveries to large companies, which sometimes included having machines already making specific parts before customer sign-off.
Slacum continued to work for Mazak while moonlighting part time at his shop. "It was exhausting, but seeing something I did, seeing the shop grow, gave me the energy to keep going," he said. "It sure was not the income, because I did not draw any salary. It all went back into the shop. After another year I left Mazak."
He had learned all about Mazak machines and their conversational programming language, Mazatrol, and had gained exposure to nearly all CAM software available to industry, learning use of the primary systems used by customers. "When with Mazak I saw every CAM vendor's software, because they all wanted to show us what they could do," said Slacum. "I was traveling with software that would retail for $300,000, but free for us to use. I ended up using only three CAM packages because, together, they covered most of what our customers used."
However, with limited capital and only two machines, Slacum chose to do all Atlantic Precision's programming with Mazatrol. The shop built its customer base through referrals from friends working within large companies or in other shops. With more customers, Slacum added more Mazaks, but as customer parts became more complex, programming became too time consuming. So, in 2014, he decided it was time to purchase CAM software, and began the evaluation process. "Every system I have used has positives and negatives, but you choose a specific system because it is the best for what you are trying to do," Slacum said. "I knew that GibbsCAM could do the type of work I wanted. It could handle everything, and it was easy to use. Then, once GibbsCAM embedded VoluMill software, it became super powerful."
At Mazak, Slacum had been kept busy in the field and never had the opportunity to attend software training, so he taught himself. "GibbsCAM had built-in tutorials, so I went through all the examples and learned to use it by myself. That is how easy it is to use. GibbsCAM was one of my two strongest packages and the easiest to use. It was also great at multitasking, including programming mill-turn machines. Whenever I used it, it always worked flawlessly."
Slacum had also developed an appreciation for software support, and had come to believe that no matter how good the software, it is only as good as the support you get from the vendor. At the time, the GibbsCAM representative who supported Mazak was Bart Ehlers, who would eventually start his own company, CAMCO, to sell and support GibbsCAM in the Northeast.
In 2019, Bart Ehlers' company, CAMCO, inherited Atlantic Precision as a customer when it expanded its territory. "My previous reseller had great technical expertise, but as a one-man operation, he was unable to respond quickly," Slacum said. "I may need help only once a month, but when I need it, I cannot wait, so it is great that Bart is forward thinking and a good organizer. He knew that customer support is critical, and made sure to have enough customer support when he formed CAMCO. Now I get an immediate call back when I need help."
Bart Ehlers explained, "CAMCO does one thing, and one thing only, and that is GibbsCAM. We have a staff with a combined 75 years of GibbsCAM-specific expertise and machining experience. We know that software is only half of the solution and that the other half is the supplier. Will they answer the phone and be there to support you? Do they have the expertise to understand your machining challenges, beyond software assistance, and help you overcome them? You can have the best software in the world, but if you do not have support, it is as if you are working with a hand tied behind your back."
In addition to its ease of use, GibbsCAM was designed as a modular system, intended to allow the small shop to grow as machining requirements and complexity increase while simultaneously allowing a large shop to acquire the comprehensive package with multiple workstations on a network. Instead of having separate applications for different machines, the software integrates modules that, when added, appear as part of the same menu as the original. Beginning with basic machining and turning, the software grows to 3D machining, into 4-axis options, then 5-axis and multitask machining, all supported with additional modules.
Having selected GibbsCAM, Slacum purchased all but the Tombstone Management System, which was in its early stages of release. Partly as a result of the software, and partly because of steady, recurring orders, Slacum no longer spends up to two days programming a part, and estimates that he spends no more than eight hours programming each week.
The majority of the shop's jobs are production work, the balance being engineering work for prototype and short-run jobs, always with the hope these become production jobs. Most of the orders are for an annual quantity, sometimes longer, but customer demand usually exhausts the order quantity long before the contract period.
The shop has 14 employees, running two shifts, in a 7,000 sq. ft. space. All the machines are Mazaks, including a 2-axis lathe, a 5-axis multitasking machine, four vertical machining centers and a horizontal machining center. All the machining centers are equipped with tombstones or multi-sided fixtures-the only way the shop runs production. The company serves various industries, such as power, medical and scientific instruments, including Horiba Jobin Yvon. Parts are primarily made from aluminum and copper, usually oxygen-free electronic (10100) copper, as well as steel, stainless steel, brass and bronze.
Slacum demonstrated his workflow using a slit-changer housing for Horiba Jobin Yvon, part of a contract for 3,000 pieces, to be delivered at 120 per month. The normal process at Atlantic Precision Technology is to receive the part model in STEP or Parasolid format. Slacum then opens the model in SolidWorks CAD, where he designs a fixture, combines it with the part model, fixtures and tombstone, and sends the combination to GibbsCAM, which can open files in SolidWorks and other formats. In GibbsCAM, he opens the Parasolid file and does his programming. For this part, he highlights a feature of the software that he particularly likes-the 3D surface machining-which he uses on all parts that require radiused outer edges, since form cutters will not blend cutting a full 90° arc.
Nearly all of the shop's work is done using three sides of a 4-sided tombstone, with multiple parts mounted on each face, and each face having parts in a different orientation. By rotating the tombstone, each cutting tool machines all operations on three set-ups. Each cycle finishes machining on the three sides of the fixture. At the end of the cycle, a tombstone is moved out for unloading and reloading, while a second one is moved in. At the end of the third cycle, finished parts come off one face of the tombstone, raw stock is loaded on that face, and parts on the other faces are rotated for their next operation.
For the slit changer housing, the shop starts by sawing stock to 2" x 3" x 3" billets, which are clamped into fixtures on a pallet-mounted tombstone, six parts per face. While that pallet is in use, the second pallet is loaded so it is ready to be switched when the first is done. With a pallet in place, the stock is quickly roughed out and machining proceeds through finishing operations, each tool working down and around all faces of the tombstone before a tool change.
As he explained this, Slacum highlighted the value of VoluMill, a GibbsCAM high-speed machining routine. He had been programming the first roughing pass with a large face mill. One day, a machinist forgot to tighten a clamp, and the face mill tore the workpiece out of the fixture and jammed itself into the spindle, destroying it. Crash insurance covered the $42,000 spindle and other damage, but it cost nearly a month of downtime waiting for technicians to repair the machine. "That was an expensive lesson," Slacum said. "I switched the top milling operation to a .500 in. cutter with VoluMill. If this were to happen again, I prefer breaking a small cutter rather than jamming a big face mill into the spindle. Because VoluMill calculates volumetric material removal for steady, high speed removal, it is probably just as fast as a large face mill."
Finished parts for one customer, whose instruments perform prismatic light separation and precision light sensing, often have tolerances of .0004". Some are anodized while others are painted with special light absorbing paint-a service Atlantic Precision provides-along with minor assembly.
The shop could be growing faster than it is, but Slacum needs to add electric power. He has been working with his landlord and power company to install 480-volt service. As soon as that happens, he plans to add another horizontal machining center with a 500 mm Mazak Palletech System and robot. Although the system has capacity to serve up to 12 machines, Slacum plans to start with a two-machine cell. Once that is installed, he plans to add the GibbsCAM Tombstone Management System, which will greatly reduce the programming time and further automate the cell.
Rich Slacum is also considering a Swiss-style multitasking machine. "I can easily justify that type of machine," he said. "It would be a huge change for our shop. I would need to learn how to run it, how to handle multiple turrets and how to synchronize wait codes-all a lot more complex than 5-axis machining, so I will be relying a lot on support from GibbsCAM and the machine tool builder."
For more information contact:
Atlantic Precision Technology
432 Quarry Ln.
North Brunswick, NJ 08902
732-658-3060
Mazak Corporation
P.O. Box 970
Florence, KY 41022-0970
859-342-1700
www.mazakusa.com
GibbsCAM
3D Systems Corp
323 Science Dr.
Moorpark, CA 93021
805-523-0004
www.3dsystems.com/gibbscam
SOUTHWEST
Jason Heyse
Texas Offline Inc.
281-376-2003
sales@texasoffline.com
www.texasoffline.com
NORTHEAST
New England to VA
Bart Ehlers
CAMCO ne
6 Della St
Ithaca, NY 14850
720-317-9578
camco-ne.com
bart@camco-ne.com
Central & W. PA
BryCAM Solutions
4017 Washington Rd
Suite 3000
McMurray, PA 15317
412-737-5363
gibbscamsales@brycamsolutions.com
brycamsolutions.com
Midwest only
IA, KS, MN, ND, NE, SD
Midwest CAM Solutions
877-444-0982
midwestcamsolutions.com
IL, MO
Port CNC, Inc.
817-985-0331
WI
Port CNC, Inc.
414-817-7070
portcnc.com
West only
CO, NM, AZ, NV, KS
Daystrom Technologies, Inc.
303-534-8345
daystromtechnologies.com
Pacific NW & N. CA
WestCAM Solutions
888-530-6068
westcam.co
Southern CA
Complete Automated Manufacturing
805-577-8811
camcnc.com