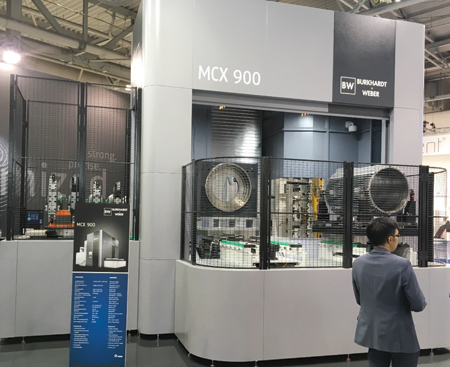
MCX 900 for large industrial motor frame production
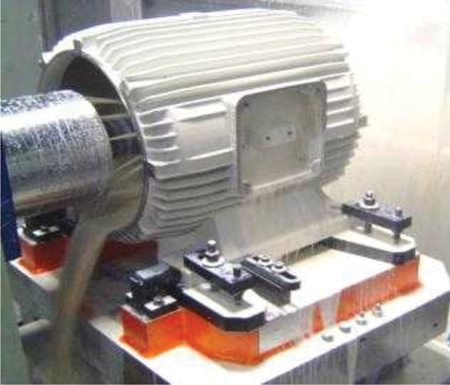
Boring a large bore with Bearing Spindle Extension
"Four-axis machining center designs have matured and mostly are thought to be within a known range of capabilities by today's manufacturing engineering standards. A customized BURKHARDT+WEBER MCX 900 machining center proves to differ. Today's state of the art reliable technologies engineered into customized machining centers can supply highly productive exceptions and are expanding into more economical multitasking opportunities," said a company spokesperson.
Large industrial motor frames have several challenges often thought to be solved by using vertical turning centers (VTLs) with Y-axis and live tool capabilities, or a combination of VTL turning and machining on a horizontal boring mill or large horizontal machining center (HMC) to create economical solutions. "Here the customized BURKHARDT+WEBER MCX 900 HMC offers a more cost-effective method and a faster process overall," said the spokesperson. "The MCX 900 features more automation, more production safety and more flexibility while keeping a simple approach. It is a great example for highly productive automation with complete machining on a 4-axis CNC machining center, replacing multiple CNC machines (turning and milling)."
According to the company, the customized MCX 900 machining center is configured with exceptional standard options, making it a unique production tool for large motor frames and other components with similar machining challenges. "While the MCX 900 is a fully featured machining center, ready for integration into automated systems with Industry 4.0 features and lights-out machining capabilities, it offers some additional unique advantages," said the spokesperson.
The standard features include a 2-step geared headstock with up to 1,900 Nm torque and spindle speeds up to 10,000 RPM, and a large tool magazine with capacity for more than 600 tools that can include machining heads. The direction setting BURKHARDT+WEBER magazine features a tool weight capacity of up to 70 kg and 1,200 mm in tool length and batch type tool loading.
BURKAHRDT+WEBER automation features allow the use of tool extensions, increasing the boring capacity to 900 mm diameter for a boring depth of up to 1,200 mm with fully automatic tool exchange. Rough and finish boring of the large bores is fully automated and improved upon with better roundness and straightness while delivering shorter cycle times. The tool extension provides rigid support with extended spindle bearings reaching far over the pallet. "Typically, this type of performance is only found with conventional boring mills that cannot match the MCX 900 productivity," said the spokesperson. Additional boring tools outside of the tool magazine capacity are fully automatically exchanged from a third pallet station in pick-up mode.
Process parallel monitoring features increase the spindle in cut time overall. Tools are maintained or new tools are loaded fully parallel to the machine cutting via an operator friendly batch type tool load station at the magazine. The MCX 900 is equipped with a robust BURKAHRDT+WEBER facing head, allowing full featured static turning with fully automatic facing head exchange from the magazine.
"The customized MCX 900 features a combination of high spindle speeds, large boring capabilities at low speeds with long tool reaches, and integrated static turning features while fully automated. The machine delivers productivity to the process that is difficult to match with conventional CNC machines," said the spokesperson.
For more information contact:
BURKHARDT+WEBER LLC
Machines and Methods
1845 Airport Exchange Blvd.
Erlanger, KY 41018
859-308-6625
info@burkhardt-weber.com
www.burkhardt-weber.com
NORTHEAST
CT, ME, MA, NH, W.PA, RI, VT
INIRAM Precision Machine Tool Inc.
333 North Main Street
Middleton, MA 01949
978-854-3037
www.iniram.com
WEST
WA, OR, ID, MT
Machines & Methods, Inc.
13400 NE 20th Street
Suite 15
Bellevue, WA 98005
425746-1656
www.machinesandmethods.com