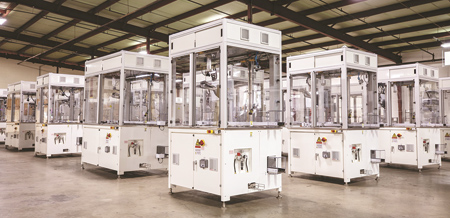
Tooling Technology's FLEXBASE flexible and modular automation work cells
Tooling Tech Group (TTG) has announced the availability of its FLEXBASE standardized modular automation cell designed to easily integrate with robotics, vision, lasers and other technologies. Flexible and scalable, the FLEXBASE systems can be configured as a standalone, automated workstation with manual loading and unloading, or linked together via conveyors to quickly create a complete automated assembly line.
"All manufacturers today are challenged by cost and delivery constraints," said Matt Phillips, TTG Automation President. "Whether their operations involve joining, marking, inspection, product assembly or other processes, our FLEXBASE solution provides an economical solution to enhance production operations, getting product to market faster while improving repeatability and reliability."
FLEXBASE features a welded steel frame base in standard sizes of either 48" x 40" or 72" x 40" and a 37" high aluminum top plate ready to be fitted with custom tooling or fixturing. Each standard system comes with an upper and lower conveyor with stop and blocked sensors and pallets with nests that conform to almost any product. Additionally, all standard systems can be quickly modified per specific application needs.
Featuring Allen Bradley Compact GuardLogix controls and 24 VDC power supply, FLEXBASE is a compact automation solution that is fully wired with all safety features in place. The electrical enclosure has space for adding a variety of components such as motion controllers and drives, robot controllers, PCs or other larger devices. Options are also available for adding pallet stops and sensors, lift and locate, barcode scanners and even elevators for recirculating pallets.
Features and benefits include:
- Reduces time to market
- Wide variety of robot adaptations and tooling
- Easily retooled for product changes
- Increases throughput
- Standard design offers ease of training
- Builds process reliability and repeatability
- Clean-room certified.
For more information contact:
Tooling Tech Group
51223 Quadrate Drive
Macomb, MI 48042
586-580-4048
info@toolingtechgroup.com
www.toolingtechgroup.com/flexbase