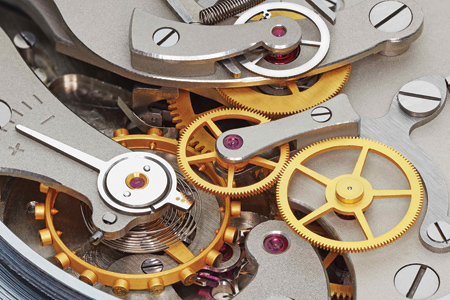
In order to prevent undesirable friction processes or rapid wear, the microscopic components of high-quality watches must have optimal surface properties.
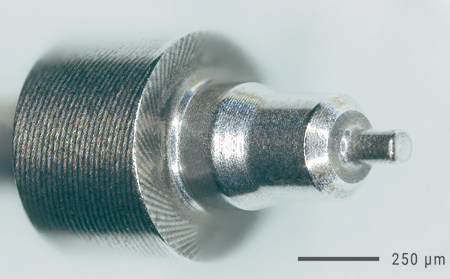
The laser is put into rotation with trepanning optics. Different corner radii on the pivot can be manufactured by automatically changing the rotation diameter and incidence angle.
In order to prevent undesirable friction processes or rapid wear, the microscopic components of high-quality watches must have optimal surface properties. This also applies to the pivots of the various shafts in the movement. If their quality suffers, then this would quickly lead to the clock noticeably gaining or losing time. These components are traditionally manufactured using a mechanical turning process. "However, chip formation, heat effects and tool wear lead to large variances in quality," said a GFH GmbH spokesperson. "In addition, conventional lathes are not always able to reliably reproduce the often challenging geometries, for example at the transitions. To avoid rejects, a high-end watch manufacturer from Switzerland is now having the pivots manufactured using a laser turning process."
This process was developed by GFH GmbH, headquartered in Deggendorf. "The system uses an ultra short pulse laser with special trepanning optics, which is able to produce even the smallest radii or undercuts without wear and without chip formation," said the spokesperson. "Blanks made from a wide variety of steel grades can be machined, as can ceramic or diamond materials that are difficult to machine with conventional means."
Manufacturing a high-quality mechanical timepiece requires the highest possible precision and focus, both from the machines used and from the watch makers. The work must be performed to very tight tolerances of +/- 0.002 mm. These requirements apply to all individual components of a mechanical movement: if the radius of a component is too large or the surface is too rough, for example, then the resulting friction could lead to faster wear and ultimately to the watch not keeping the correct time.
"In addition, the geometries required for turned and roller-burnished parts cannot always be produced with micrometric precision on conventional machining systems, leading to rejects," said the spokesperson. "In particular, undesirable side effects such as chip formation and heating result from contact between the tool and the workpiece. Watch manufacturers are also faced with the problem that the high strength and stainless steels and alloys, which are essential for a high quality watch, are difficult to machine or cannot be turned at all, since they have a high level of mechanical stability. This led to the partnership between the Swiss watch manufacturer and the German laser machining specialist GFH GmbH, in order to utilize the potential of laser based micro machining for watch manufacturing for the first time."
GFH was already tasked with manufacturing 2D precision components in 2016. The good results and the special trepanning optics used by GFH immediately suggested continuing the joint effort. Now the Swiss company has contracted GFH to manufacture the challenging pivots using its proprietary laser turning process, contactless and without chip formation.
5-Axis Machining System Also Handles Ceramics or Diamond
An ultrashort pulse laser (USP) lies at the heart of the micromachining centers used by GFH and produces a uniform laser spot as small as 25 µm. This provides good control of the process and allows for manufacturing within a tight tolerance range. When the laser is on, a high amount of energy is applied to the workpiece for a short time. Melting or thermal changes do not occur because the material is vaporized instantly. The "cold" removal also preserves the surface properties.
"Because a component roughness of Ra < 50 nm is specified in the contract, it is even more important to avoid negative changes to the material properties as a result of the machining process," explained Anton Pauli, Director at GFH GmbH. "By using our special laser, the blank remains free from thermal and mechanical effects."
The laser is put into rotation with trepanning optics. Different corner radii on the pivot can be manufactured by automatically changing the rotation diameter and incidence angle. The flexibility of the laser tool is also necessary to carve out the challenging transitions on the shafts. The changing diameters and resulting variance in track speed require a laser control system that uses the pulse-on-demand principle: the pulses are triggered based on the track that is being traced, not at fixed time intervals.
"This allows us to avoid elevated energy levels and lets us work with the correct dose, so that geometry transitions within a process step are not a problem," Pauli explained. "The flexibility of laser micro machining also makes it possible to perform different processes. Cutting, removal, drilling and structuring processes can be performed in one clamping operation in addition to laser turning. We achieve the high precision requirements and save valuable time in this manner. GFH GmbH did not have to customize the systems for this contract, since their flexible kinematics meant that they were already designed to handle the challenging pivot structuring."
Tribofinish Also Possible on Laser Turned Parts
The Swiss company is highly satisfied with the final quality of the components. Since laser turning was able to meet the requirements for the pivots, the industry-standard finishing steps can be implemented as well: in order to keep the surface roughness of the watch components particularly low, a final finishing process using slide grinding or tribofinishing is often used. "Normally, the abrasive mixture and the polishing process must be matched precisely to the component," said the spokesperson. "The lower the desired roughness of the final component, the more time-consuming and costly this process becomes. Since the laser machined pivots delivered by GFH already exhibit a surface roughness in the sub-micrometer range, Tribofinish can be applied here as well. This allows the roughness to be reduced even further, without deforming the fine geometry of the component."
For GFH, this contract has shown that high performance materials can be machined very effectively with laser turning, so that the process can be used not only for pivots, but also for other components in watch manufacturing. In addition, it allows for greater freedom with regard to the choice of material used, since laser machining using USP lasers does not introduce any limitations.
"We will continue performing material tests in the future, in order to continue pushing the boundaries of what is possible," Pauli said. The company has already implemented similarly successful projects in the field of medical technology, with equally tight tolerance specifications. The Swiss watch manufacturer is also satisfied with the results. The collaboration was characterized by transparency and a high level of technical expertise on the part of GFH GmbH, so that we want to continue jointly exploring the potential of laser turning for our production."
For more information contact:
GFH GmbH
info@gfh-gmbh.de
www.gfh-gmbh.de