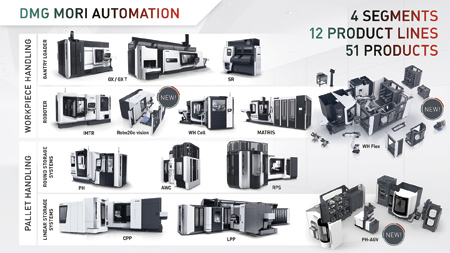
In addition to fully integrated, customer-specific solutions, DMG MORI has a total of 51 standard automation products in its portfolio. Today almost every DMG MORI machine can be automated.
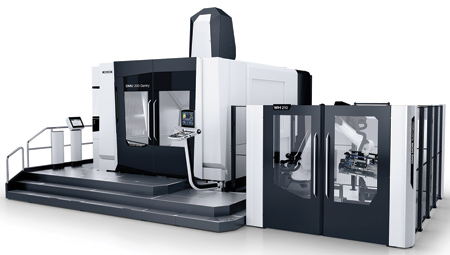
With the WH 210 on a DMU 200 Gantry, DMG MORI enables handling of up to 2,000 mm x 1,350 mm large workpieces.
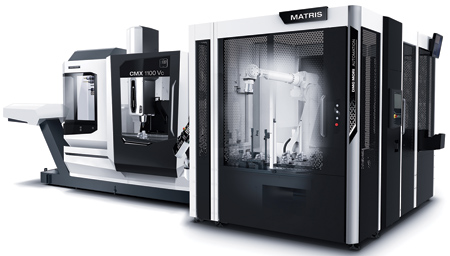
MATRIS workpiece handling
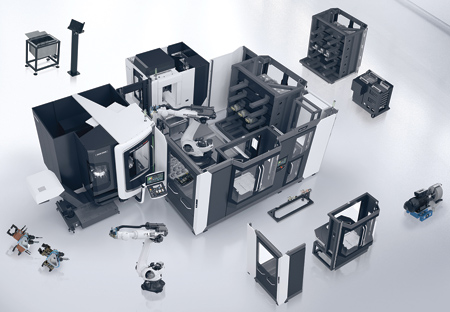
The WH Flex enables customization with its modular design.
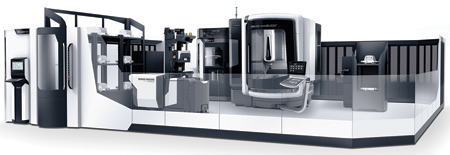
The PH-AGV 50 (automated guided vehicle) driverless transport system moves independently on the shop floor and can be easily integrated into already existing production areas with its open layout design as well as simple extendibility.
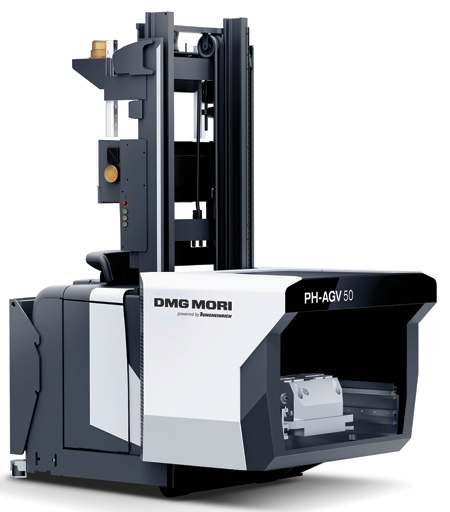
The PH-AGV 50 is designed for workpieces of a diameter up to 840 mm x 500 mm and 600 kg.
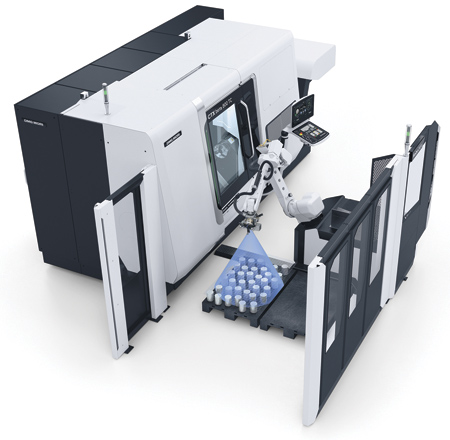
The new Robo2Go Vision is a further development of the flexible robot automation with an innovative camera system.
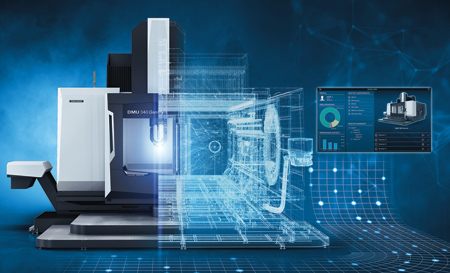
With the commissioning of automation solutions, the DMG MORI Digital Twin achieves a time saving of up to 80%.
With the consistent automation of its machine portfolio and its interlinking with digital solutions, DMG MORI is creating a future-oriented production. DMG MORI will offer all machine tools in its portfolio with automation solutions in order to meet increasing demand. The business area is continuously growing in the field of integrated automation solutions as well as for the preparation of respective interfaces. By 2022, 80% of machines will be delivered with automation. Consequently, the new development of automation solutions is just as important as the development of new machine models.
The increased requirement of automation solutions is addressed by the entire product portfolio of DMG MORI-from workpiece handling for small components up to pallet handling for large components. At the Polish production site FAMOT, DMG MORI recently demonstrated how three DMC 210 U duoBLOCK machines can be linked via the LPP 160. The linear pallet pool can be flexibly planned and is designed for 1,600 mm x 1,600 mm pallets and workpieces with a diameter of up to 2,100 mm and a height of 1,400 mm, and provides a transport capacity of up to 8 t. With the WH 210 on a DMU 200 Gantry, DMG MORI enables handling of up to 2,000 mm x 1,350 mm large workpieces. The automation solution is directed at customers in aerospace, mechanical engineering as well as automotive industries and reduces idle times. Increase in productivity of up to 95% is possible.
These and other automation solutions are part of an integral production process for DMG MORI. This approach is emphasized by the machine tool manufacturer DMG MORI HEITEC, with the following objective summarized by Managing Director Markus Rehm: "We design and realize the linking of all processing steps related to the topic of automation. Together with DMG MORI, we offer a consistent and reliable solution-from engineering through equipment, tooling, NC programs up to integrated automation and connection to the IoT world. The service portfolio covers everything with regard to consultancy, from the concept and the offer up to commissioning. This way, service, maintenance and spare parts are all also available from one source."
DMG MORI HEITEC complements the product portfolio of DMG MORI with standardized automation solutions for the handling of workpieces and flexible automation solutions. This includes the WH Cell for machining centers and turning machines as well as the WH Top and WH Front for the CTX beta series turning machines. "We have been able to successfully complete several dozen projects since DMG MORI HEITEC was founded in December 2017," said Rehm in reference to robot solutions already delivered. "We have been able to significantly improve the autonomy and availability of our customers. In the area of pallet handling, which accounts for 60% of the automation volume, the DMG MORI plant in Pfronten is responsible for development. The flexible robot automation Robo2Go is located at the site in Bielefeld."
MATRIS: Modular Variety of Features
An individual adjustment of automation requirements enables the MATRIS workpiece handling for workpieces up to 20 kg. It can be equipped with different grippers and can be combined with standardized peripheral modules, among others for washing, measuring, storing or visualizing. The structured design of the robot programs and teach-in functions enable a fast launch into serial production. No robot programming knowledge is required, as everything is programmed on the CELOS basis by means of cycles in the dialog via input masks as master computer LPS 3 can be used for connecting the different peripherals and also makes maintenance and operation easier. The MATRIS is available for turning machines of series NLX and NZX up to size 2500, vertical machining centers of the CMX V (MAPPS) and NVX 2nd Generation up to size 5100 as well as the NHX 2nd and 3rd Generation (MAPPS) up to size 5500.
WH Flex: Versatile Handling for Workpieces and Pallets
DMG MORI's automation concept WH Flex is the latest further development in the product portfolio. This is a flexible and modular automation solution for both workpiece and pallet handling. With its modular construction, WH Flex can be easily customized and link up to nine lathes or milling machines. "It allows us to react even better to the very individual and unique requirements of our customers," said Rehm. "Starting with the basic configuration of the WH Flex, we can put together an optimal solution for the customer from a large range of standard options. Included in the modules are storage systems such as shelving, paternosters or pallet stations, as well as various gripping and gripper change systems. Other options such as the PLC outward transfer, alignment and turning stations and a cleaning station as well as various add-ons for laser marking or measuring round off the system. Even a simple control has been included: the DMG MORI CELL CONTROLLER provides an intuitive user interface with intelligent job management and grid programming for comfortable teaching and set-up of new components."
PH-AGV 50 and Robo2Go Vision: Flexible and Retrofittable
In the field of pallet handling, DMG MORI and Jungheinrich have developed the PH-AGV 50 (automated guided vehicle), a driverless transport system that moves independently on the shop floor and provides even more flexible production processes and unrestricted access to the machines. Because of the open layout design and simple extendibility, the AGV system can also be effortlessly integrated into existing production areas. The PH-AGV 50 is designed for workpieces of a diameter up to 840 mm x 500 mm and 600 kg. The automation solution enables enhanced flexibility through free accessibility to the machines and freely programmable travel paths for the handling unit. The configuration of the pallet rack and the set-up stations is modular. The number and positioning can thus be completely adapted to suit the specific requirements of the customers. The control and the management of the system is taken on by the DMG MORI LPS 4 master computer, which optimizes all processes in production.
This new flexibility and the retrofitting capability of the PH-AGV 50 is regarded by DMG MORI as a future concept for pallet automation. A similar degree of flexibility has already proven its worth in the area of turning machines with the Robo2Go 2nd Generation, as Harry Junger, Managing Director of GILDEMEISTER Drehmaschinen, stated: "The new Robo2Go Vision is a further development of the flexible robot automation with an innovative camera system. With 3D camera detection, we can use standard pallets to store parts and in this way avoid restacking parts." With the aid of the dialog-guided control via CELOS and the 3D-camera, the teach-in takes less than 10 minutes.
DMG MORI Digital Twin
The DMG MORI Digital Twin, a complete, digital image of the real machine, enables DMG MORI to put the system into operation on the PC virtually. "The real-time capable digital models enable the processes and procedures to be simulated prior to the machine being assembled at the customer's facility," said Rehm. "This means time savings of up to 80% during real commissioning. There will also be a clear improvement in quality. With the DMG MORI Digital Twin, the customer is able to retool for new products parallel to primary machining also during ongoing production and thus continuously optimize the production process. This example demonstrates that we are increasingly linking our new automation developments with digital productions using open interfaces. This means we can create a unit with integral connectivity for our customers as the basis for a production of the future."
For more information contact:
DMG MORI - Americas Headquarters
2400 Huntington Blvd.
Hoffman Estates, IL 60192
847-593-5400
Service Hotline:
855-DMG-MORI (364-6674)
us.dmgmori.com