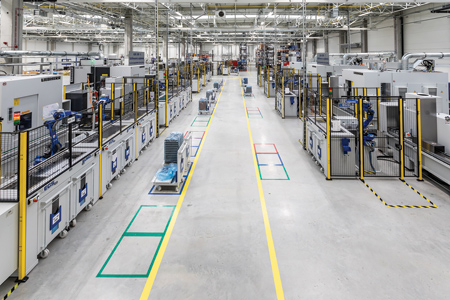
Morat Swoboda Motion's plant has three Liebherr gear hobbing machines and six Liebherr generating gear grinding machines.
Morat Swoboda Motion GmbH, a joint venture comprising the Franz Morat Group and Swoboda, develops and produces drive components for e-motive products. In 2017, the company received a nomination for a large-scale project and decided to commission a new manufacturing facility.
"Our aim was to address the specific challenges of gear wheel production for e-motive drives. We wanted as much automation as possible and, above all, a machine landscape at the highest technological level," said Stephan Mayer, Project Manager.
The basic prerequisites were high process stability, series suitability and short machining times. Of particular importance was the production of toothed gears. "The teeth interlock with each other, which is how the rotation of one toothed gear is transferred to the next one," said Mayer. "The whole thing works like a clock mechanism. If the individual teeth do not lock in perfectly, the motor will not work at all."
Morat Swoboda Motion selected Liebherr as its solution provider, and Liebherr installed three LC 60 gear hobbing machines and six LGG 180 generating gear grinding machines in the plant. The entire production is fully automated.
"With the e-bike, disturbing noises from the drive create an unnatural riding feeling. That is why we have performed diverse modifications to the surfaces of the toothed gears and optimized the gear geometry," said Mayer. "To do this, we worked together very closely with Liebherr's technology application department. Together, we found a very successful method and adapted the process parameters so that the drive units produce no noise, and the e-bike rider hears a natural soundscape during the ride."
Purchasing a total of nine Liebherr systems paid off. "The decisive factor when selecting machines was that, with Liebherr, we had a provider that covers both technologies: gear hobbing and generating grinding. We wanted a competent point of contact who would completely understand our process and deliver suitable solutions," said Mayer.
With the gear hobbing and generating gear grinding machines, Liebherr contributed to the company's ability to provide high-quality components on a large scale. "The entire process development, up to acceptance, ran very smoothly," Mayer said. "We developed a lot of things jointly with the technology department. The installation and support also work flawlessly."
For more information contact:
Liebherr Gear Technology, Inc.
1465 Woodland Drive
Saline, MI 48176-1259
734-429-7225
info.lgt@liebherr.com
www.liebherr.com