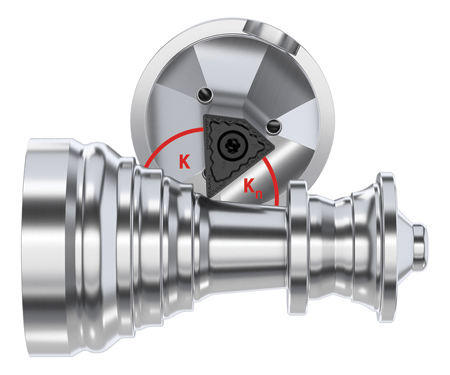
CERATIZIT High Dynamic Turning (HDT) with FreeTurn tools allow 360º rotation of the cutting surface.
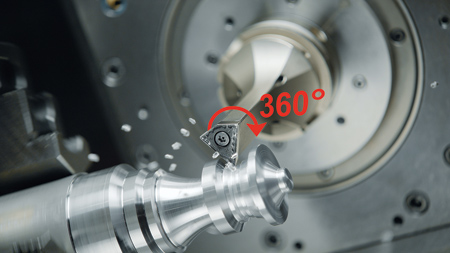
All contours can be machined in one set-up, since the traditional turning operations of roughing, finishing, contour turning, face turning and longitudinal turning are all accomplished with a single tool.
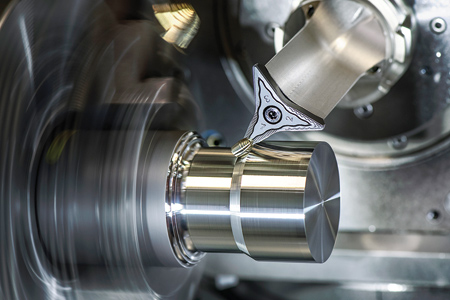
One indexable insert with several cutting edges can comprise different cutting angles, corner radii, chipbreakers, coatings or cutter materials to suit specific applications.
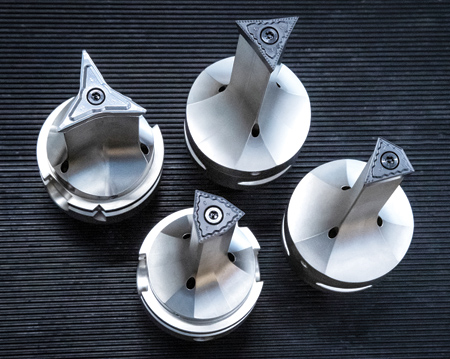
The FreeTurn test program includes four insert geometries and can be used for many standard applications. Contact CERATIZIT to arrange the program.
At EMO 2019, CERATIZIT launched the first standard range of products for its High Dynamic Turning (HDT) with FreeTurn process, and has taken the next step in turning solutions. This new development is now available and will be showcased at IMTS in Chicago in September 2020.
High Dynamic Turning (HDT) from CERATIZIT, combined with the company's dynamic FreeTurn tooling, means that it is now possible to carry out all traditional turning operations such as roughing, finishing, contour turning, face turning and longitudinal turning with just one tool. "HDT with FreeTurn represents a completely new method of turning," said a company spokesperson.
"For 100 years, new cutting materials, new chip breakers and a few new tooling systems have been invented to optimize turning," continued the spokesperson. "However, the actual basic turning process has remained essentially unchanged. Even today, a contour is created with an indexable insert at a fixed angle to the workpiece. This method has not changed, even with the addition of controllable axes in modern turning-milling centers, machines that are intended to serve one purpose, namely, to manufacture a component as completely as possible within a single machine work envelope. CERATIZIT has taken advantage of the features on these turning-milling centers and developed the HDT System. The simple idea behind HDT: the tool approach and point of contact in the machine can be varied as opposed to conventional turning with a fixed tool."
Utilize Milling Spindle for 360° Degrees of Freedom
Instead of the classic, static position of the insert in the holder, the milling spindle is now used to produce the corresponding approach angle to the workpiece. "The use of the spindle drive, in conjunction with the slim, axial tool design of the FreeTurn tools by CERATIZIT, creates a degree of freedom of 360° without the risk of collision, thus providing unprecedented flexibility," said the spokesperson. "Due to the rotation around its own tool axis, the cutting edge change can be done without interrupting the cutting process. Additionally, the angle of approach is freely variable at any time and can even be changed while cutting. This not only enables flexible machining of almost every workpiece contour, but also optimum chip breaking, higher feedrates and an increase in tool life."
Depending on the machine capabilities, the technology can be used functionally in all areas of turning operations. "The approach of the milling spindle on the Y/Z axis on turning-milling centers is widespread," said the spokesperson. "As a result, further possibilities can be achieved with HDT that seemed previously unachievable. For example, cutting from above and below is possible. Depending on the machining area and workpiece size, this freedom can be an important factor in production."
FreeTurn Inserts with More than Two Variable Features
"In the future of HDT, the static turning tools of the past will be replaced by dynamic tools," said the spokesperson. "One such dynamic tooling solution is FreeTurn by CERATIZIT. The defining characteristic of FreeTurn tooling is its simple structure. The toolholder, together with its slim shank and axial concept that optimizes the direction of the cutting forces into the spindle, form a stable unit. At the cutting end, there is a multi-sided insert, which is simply screwed in place. The principle is quite simple: the patented FreeTurn insert can consist of several cutting edges with different properties. This allows for different angle points, corner radii or chip breakers-even different coatings and cutting materials are conceivable. The tool can therefore be adapted to the machining requirements, offering the further advantage of replacing several tools on a job. This, in turn, leads to significant savings in tool change times, tool magazine loadouts and tool costs overall. The result is making components with highly complex contours without limitation, using only one FreeTurn tool. This flexibility ensures complex component holding can be quickly and effectively adapted to the new machining situation."
Saving Tools and Machining Time
In one recent application at Spanish wheel manufacturer ROTOR, an indexable insert with two different cutting edges was used to manufacture an aluminum wheel hub. One cutting edge is used for roughing (1,500 RPM, ap = 2 mm, f = 0.4 mm/rev) and one for finishing (2,000 RPM, ap < 1 mm, f = 0.25 mm/rev). When using HDT, the approach angle can be changed during machining, making it possible to machine all contours in just one set-up, even undercuts that would not be possible with a standard approach angle of 90°. The tool is also able to cut in both directions, saving time-consuming rapid moves and increasing efficiency. In comparison to the turning process normally used by ROTOR for wheel hubs, this machining process used four fewer tools and reduced the machining time by 30%.
FreeTurn Solution Range
From the beginning of the HDT process, CERATIZIT has relied on an open source model, supplying all interested parties with the relevant information to allow them to help develop their HDT turning process.
Meanwhile, the tool manufacturer devoted its attention to its core business, developing a standard range of FreeTurn tools. Four indexable insert geometries were initially launched. This range included indexable inserts for machining steel/stainless steel (2x roughing and 1x finishing, 3x roughing, symmetrical) and for aluminum (3 cutting edges, symmetrical). This initial range covers a number of applications. The holders are available with a variety of overhang lengths for each size and are available for the HSK-T and PSC machine interfaces. CERATIZIT is making this insert package available to interested parties on a test program basis.
For more information contact:
CERATIZIT USA, Inc.
11355 Stephens Road
Warren, MI 48089-1833
800-783-2280 / 586-759-2280
FreeTurn@ceratizit.com
www.ceratizit.com/hdt