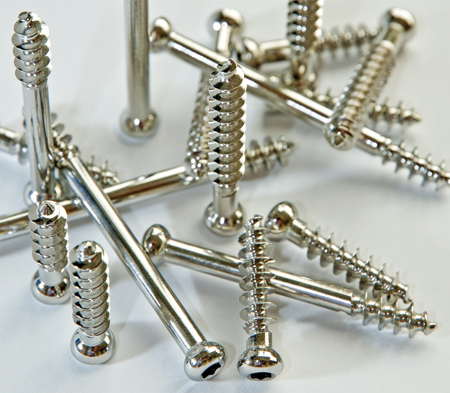
There are 900 million medical screws produced yearly and the numbers continue to rise.

A typical Torx or hexalobular socket
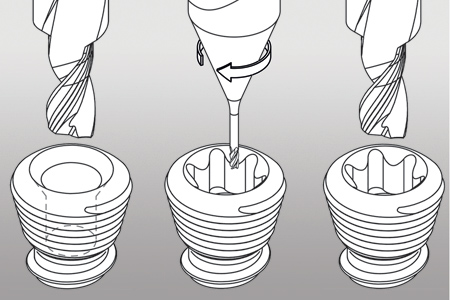
Pre-drilling/chamfering/milling with helical interpolation or side milling/deburring is what Mikron Tool recommends for efficient machining of hexalobular sockets.
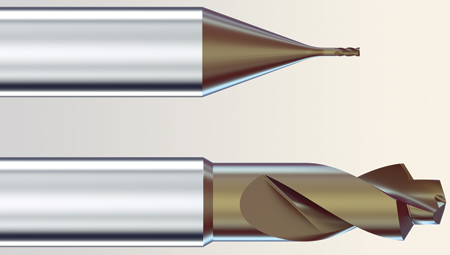
Two cutting tools are necessary for the complete machining of hexalobular sockets.
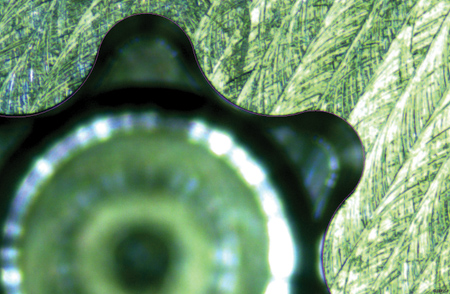
"Very tight tolerances must be kept to guarantee profile accuracy and wall squareness of the hexalobular socket, from the first to the last screw produced," said a company spokesperson.
"A drill, a milling cutter and an ultimate machining strategy with perfectly tuned parameters-these are needed when machining medical screws made from titanium or stainless steels," said a Mikron Corp. Monroe spokesperson. "Mikron Tool has developed a turn-key solution that simultaneously does the machining of hex lobular bone screws (better known as Torx) 50% faster while also providing a high degree of profile precision and achieving nearly burr-free results."
"There are 900 million medical screws produced yearly and the numbers continue to rise," continued the spokesperson. "Each second that can be gained in the process counts. Most of these screws are produced on lathes. The thread is machined on the main spindle and the hexalobular Torx socket is machined on the sub-spindle. That particular operation is usually slower and defines the cycle time, and provides an opportunity to improve efficiency."
Mikron Tool offers with the HEXALOBE-Program a turn-key solution. "The solution is not only based on the cutting tools-it also delivers a package with the best machining strategy and the right parameters," said the spokesperson. "This is because during development, it became clear that good results could only be obtained when all factors fall in place correctly."
Titanium or Stainless Steels?
"The two materials from which today 90% of all medical screws are made are titanium and stainless steels," said the spokesperson. "They are each quite different when it comes to their behavior during the chip removal process. During development it became clear that the tools as well as the suitable strategy needed a differentiation. Especially with titanium-with its high elasticity, stronger cutting force was required. This, in turn, produced higher stress on the cutting edges. This already meant, right from the beginning of development, that a different carbide was called for."
For the machining process, both materials have to be differentiated. While with titanium helical interpolation and also side milling are possible, Mikron Tool only recommends side milling when working with stainless steels even though this particular process is a bit more time consuming.
The Strategy
A well-defined strategy was just as important as the cutting tools when development was initiated. This is because when choosing the tools, it must be clear how these are being applied.
Right from the beginning different approaches were considered. Especially efficient was one that could utilize a minimum of different tools, e.g., step drilling (milling the hexalobe) and subsequent deburring.
Other strategies like predrilling of the six exterior diameters and the center followed by milling and deburring were a challenge, especially when working with titanium. It turned out to be a demanding task for the micro drills.
The milling process, which in the chosen strategy was the most time-consuming operation, can be done with helical interpolation (with max. pitch 0.8xd) or with side milling (with stepover max. 0.5xd).
Each procedure has its pros and cons: with helical interpolation there will be a slight lateral load at the milling cutter (Fx), since there is also a simultaneous vertical stress (Fz).
A higher stress on the cutting edge corners has to be reckoned with and, because of this, they were geometrically reinforced. Generally, this produces a faster and more fluid operation. With side milling (or wall milling) the total depth is reached in several steps, since only two axes are used for each step. The step-over stays the same for the entire operation even though the radial stress on the cutter is more elevated.
Reduce Operations
The four operations-pre-hole drilling, chamfering, milling and deburring-need to be completed in three operations with two tools. "First, a step drill creates the center bore and a chamfer of 120°, with excellent surface quality of Ra 0.2 µm, Rz 0.8 µm," said the spokesperson. "After milling the final shape, this tool will be used once again in the last operation to achieve a nearly burr-free surface and enhanced surface quality."
The milling cutter with three or four flutes-depending on the diameter-is available in two standard lengths, so that depending on the screw type, different Torx shapes can be machined. "Its high stiffness allows machining with high feeds and massive stepover, while still guaranteeing the necessary hexalobular profile accuracy," said the spokesperson. "The surface quality is given by the special geometry, which also provides the ability to work with high stepover so the operation can be completed with few steps."
Focus on Quality
"Besides efficient machining, which means short cycle time and long tool life, the development of the new tools also concentrated on achieving top quality," said the spokesperson. "Very tight tolerances must be kept to guarantee profile accuracy and wall squareness of the hexalobular socket, from the first to the last screw produced. Surface quality and burr condition were also important considerations that were achieved."
"First experiences with the new CrazyDrill and CrazyMill Hexalobe tools on a lathe 32/8 from DMG MORI have shown that cycle time compared to other on the market available tools could be reduced by 50% to 60% while at the same time with a fast feed (0.03 mm/rev. per flute) and high surface quality (Ra = 0.2um) can be reached," concluded the spokesperson.
For more information contact:
Mikron Corp. Monroe
200 Main Street
Monroe, CT 06468
203-261-3100
mmo@mikron.com
www.mikron.com