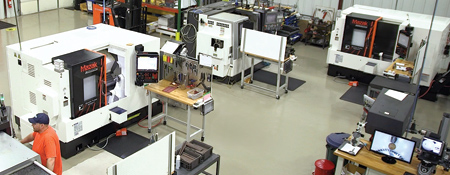
Forest City Gear's 8,500 sq. ft. facility includes new Mazak Quick Turn Turning Centers with multitasking capability so both turning and milling can be done in one set-up for shorter lead times and greater accuracy.
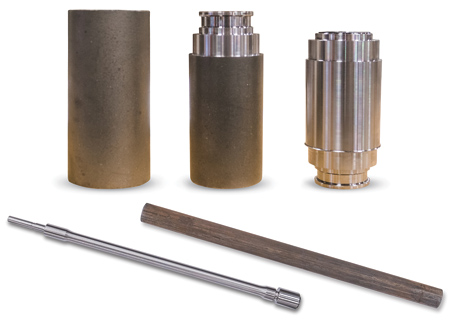
With the help of Mazak Quick Turn technology, Forest City Gear can now produce its own blanks for gears ranging from 1/8" to 8" in diameter and shafts up to 16" long in lot sizes from one to 1,000.
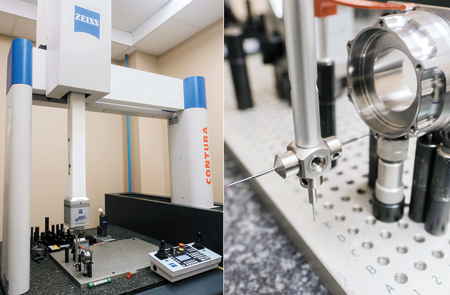
Forest City Gear has its own dedicated Zeiss Contura CMM, putting inspection in close proximity to the shop floor to reduce queue time.
"Forest City Gear is widely regarded as one the best job shops in the world for the production of high precision fine- and medium-pitch cylindrical gears," said a company spokesperson. "The gears flowing through its facility on any given day can be for anything from aircraft to automation, medical instruments to military vehicles, and dozens of other applications. The only common denominator? Everyone wants it yesterday."
With demand and quality standards at their highest level in the company's 65-year history, improving delivery time is of paramount importance. That is why the company recently made the decision to eliminate the most serious bottleneck in its "make complete" value stream by bringing critical gear blanking operations in-house. The goal? Cut turnaround time on gear blanks from as long as 12 weeks to as little as a week or two.
"Whether for a space exploration vehicle or an application closer to home, our customers have delivery requirements that are increasingly hard to meet when gear blanking is outsourced to the turning houses," explained Forest City Gear Turning and Milling Supervisor Mike Miller. "The process can take weeks and stretch out even further when blanks are rejected. Bringing the work in-house is paying dividends every day, and lead times are a fraction of what they were just a few months ago."
Taking the Wait Out of High-Quality Gear Blanks
Today Forest City Gear operates a new state-of-the-art 8,500 sq. ft. facility, in close proximity to its main plant in Roscoe, IL, that is dedicated almost entirely to the precision turning, milling and inspection operations needed to produce its gear blanks.
At first glance, the typical blanking operation for a gear or shaft seems simple enough: start with bar stock or forging, rough and finish turn the part to remove excess material, perform the necessary milling and drilling operations-right up to where the gear teeth are cut in subsequent operations downstream. It is a process that is easily manageable in a gear production environment running the same commodity parts day after day. But at Forest City Gear, blanks are needed daily for dozens of different customer orders, with sizes ranging from 1/8" to 8" in diameter and shafts up to 16" long-all in lot sizes as small as one or as many as 1,000.
"We responded to this challenge the way we always do at Forest City Gear: invest in the best, most productive equipment for the job," said Forest City Gear Director of Operations Jared Lyford. "Case in point: our four new Mazak Quick Turn Turning Centers. They give us a multitasking capability, so both the critical turning and milling operations can be done on a single machine in one set-up for shorter lead times and greater accuracy."
Quick Turning, Multitasking with Mazak
"The Quick Turn 200MY seems tailor-made for the aggressive throughput and flexibility requirements of the Forest City Gear blanking operation," said the spokesperson. "The machines offer the power, torque and flexibility required to process parts across a wide range of part diameters and shaft lengths. In addition to powerful main turning and milling spindles and CNC tailstock, the machines are configured with an additional Y-axis milling spindle to create multiple tool positions, as well as a second turning spindle. This gives the machines the ability to produce particularly complex parts complete in a single set-up, saving time and helping to hold the tight tolerances required of the typical gear blank."
"Additionally, a VDI-type 12-position drum turret ensures that chip-to-chip time when changing rotary tools is extremely fast," continued the spokesperson. "As a result, each of the Mazaks do the work of multiple machines, helping Forest City Gear add greatly to its existing turning and milling capacity while reducing floor space, machine and tooling costs, and freeing up manpower for other tasks."
Higher Quality, Less Queue Time
"Given the quality demands of the industries Forest City Gear serves, including aerospace and medical, it is not surprising that the company has perhaps the best equipped quality control lab in its industry," said the spokesperson. CMM inspection is a requirement for most of the finished gear blanks before they flow out of the new facility to the main plant. But transporting the blanks to the lab, where they would wait in the inspection queue with finished gears produced in the main plant, would take precious time.
The solution? Bring the lab to the new facility. The company purchased a new Zeiss Accura CMM for the main quality lab, which freed up an existing Zeiss Contura CMM for dedicated use in the blanking facility.
Beyond Blanks
With the new operation running two 10-hour shifts and the Mazaks humming along nicely, the company now has its sights set on expanding the blanking facility with additional Mazak technology-this time adding 5-axis machining capability for the complete production of non-gear products such as gear housings and small planetary carriers.
Since 1955, family-owned Forest City Gear has been developing, manufacturing and inspecting high quality gears for use in applications that include medical devices, motorcycles, airplanes, automation and even the Mars Curiosity Rover.
For more information contact:
Forest City Gear
11715 Main Street
Roscoe, IL 61073
815-623-2168
info@forestcitygear.com
www.forestcitygear.com
Mazak Corporation
P.O. Box 970
Florence, KY 41022-0970
859-342-1700
www.mazakusa.com
Carl Zeiss Industrial Metrology, LLC
6250 Sycamore Lane N
Maple Grove, MN 55369
763-744-2400 / 800-327-9735
info.metrology.us@zeiss.com
www.zeiss.com