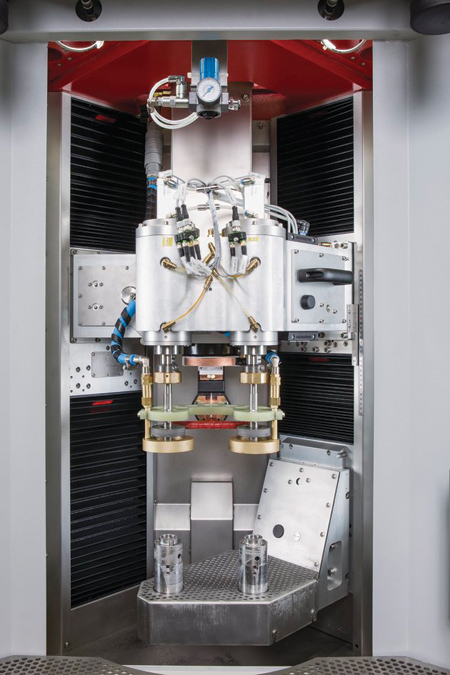
The multiple clamping columns make it possible to harden six (relatively small) parts while simultaneously loading six more parts.
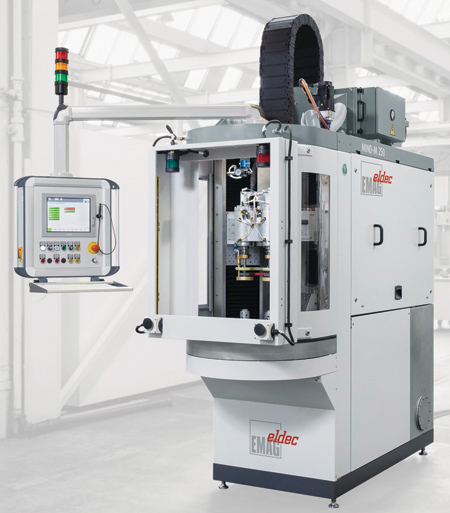
MIND-M plus induction hardening machine from eldec. In contrast to the MIND-M, the cooling system is located outside the machine. The total footprint required remains very small.
The automotive industry is facing radical changes, including increasing global competition and rapid technological development, which are drastically transforming the demands placed on OEMs and suppliers. Reduction in production costs and increased flexibility to effectively respond to changing component requirements are necessary to remain competitive in the market.
Hardening is essential to ensure the stability and quality of many components required in the automotive industry. "The traditional technique of case hardening, however, tends to be inflexible and energy intensive because it involves grouping the components together and heating them for hours in a furnace," said an EMAG spokesperson. "Induction hardening, due to its improved flexibility, is continuing to grow in popularity comparatively. It offers precisely timed cycles, extreme precision and (unlike case hardening) comprehensive integration into the production flow. Eldec is a company specializing in induction hardening including its new modular hardening machine MIND-M plus. Its compact technology, high generator output and low capital outlay all contribute to a reduction in cost per unit."
The hardening process is a crucial factor in ensuring that automotive parts can withstand the stresses they are subjected to in the transmission, chassis or engine while maintaining the parts dimensional accuracy. "The induction technology from eldec is suited to meet these challenges: the process is completed in seconds with high precision and minimal expansion in the workpiece," said the spokesperson.
The eldec MIND-M models, with the generator and cooling system included, have a footprint of just 2.3 by 0.8 meters (7.5" x 2.6"). All the components are located within the housing. A practical, modular building block system allows each machine to be put together from modules chosen according to the workpiece dimensions, desired hardening finish and all other production requirements.
The machines can be supplied with a dual spindle drive if requested by the customer. This brings a considerable reduction in processing times, since multiple parts can be machined in parallel. "Nonetheless, we were running up against certain practical limitations when applying this strategy with our MIND-M models," said Andreas Endmann, Head of Technology Sales for Hardening Systems at eldec in Dornstetten. "You also need greater generator power for the induction hardening of large parts. And if you are trying to machine two large parts in parallel on a dual spindle machine, its output has to increase even more. But the maximum power output on our earlier MIND-M models was only 37 kW in the high frequency range and 100 kW in the medium frequency range. That is not always enough for parallel machining of large parts."
eldec has now closed the gap in its range of possible applications with its new MIND-M plus induction hardening machine. It is available in two sizes, one for workpieces up to 250 mm (9.8") in length and one for workpieces up to 1,000 mm (39.4") in length. The "plus" in the name refers to the increase in power up to 150 kW (high frequency range) or 300 kW (medium frequency range). Models are also being offered for the first time with dual frequency generators (DFG) and simultaneous dual frequency generators (SDF). They allow even more accurate surface hardening on especially complex shapes and contours, and perfect adjustment of the heat penetration depth.
MIND-M plus, in combination with new drive and clamping solutions, provides its users with increases in productivity. Take for example the indexing table with two workpiece holders: two parts can be loaded onto it, with a narrow separation between them. This allows one half of the table to be loaded or unloaded by a robot while a part is being hardened on the other side of the table. If a machine has a dual spindle, then two of these indexing tables can be used, with the result that parallel machining and loading of two parts is always possible.
"The same technology can also be used on the MIND-M, of course. But the more powerful MIND-M plus now makes it possible to fully machine large parts in this way, with shorter cycle times. That is exactly what we were aiming for," Endmann said. The use of the multiple clamping column has a similar effect. Six clamping fixtures for smaller workpieces are located on each of the two opposing sides of the column. In operation, it works much like the indexing table: while a robot inserts six workpieces on one side of the clamping column, another six are hardened and quenched on the other side at the same time.
For more information contact:
Kirk Stewart
Sales Director
EMAG L.L.C.
38800 Grand River Ave.
Farmington Hills, MI 48335
248-966-4703
kstewart@emag.com
www.emag.com
SOUTHWEST
TX, OK, LA
Ric Lorilla
Regional Sales Manager
EMAG L.L.C.
248-595-1530
rlorilla@emag.com
AR
Steve Cox
Regional Sales Manager
EMAG L.L.C.
248-752-2298
scox@emag.com
SOUTHEAST
VA, NC, SC, E. FL, E. GA
Dave Fitzgerald
Regional Sales Manager
EMAG L.L.C.
248-595-1117
dfitzgerald@emag.com
MS, TN, AL, W. GA, W. FL
Steve Cox
Regional Sales Manager
EMAG L.L.C.
248-752-2298
scox@emag.com
NORTHEAST
WV
Dave Fitzgerald
Regional Sales Manager
EMAG L.L.C.
248-595-1117
dfitzgerald@emag.com
ME, NH, NY, PA, MA, RI, CT, NJ, DE, MD, VT
Troy Martz
Regional Sales Manager
EMAG L.L.C.
248-938-2430
tmartz@emag.com
MIDWEST
S. IN, OH, KY
Mark Comeaux
Regional Sales Manager
EMAG L.L.C.
248-938-2097
mcomeaux@emag.com
ND, SD, NE, KS, MN, IA, MO
Bill Konetski
Regional Sales Manager
EMAG L.L.C.
612-804-0857
bkonetski@emag.com
IL, N. IN
Tod Petrik
Regional Sales Manager
EMAG L.L.C.
248-470-2646
tpetrik@emag.com
WI, Chicago
Joe Thompson
Regional Sales Manager
EMAG L.L.C.
248-880-0233
jthompson@emag.com
MI
Mark Ashworth
Key Account Manager
EMAG L.L.C.
248-826-4242
mashworth@emag.com
WEST (none, use HQ)