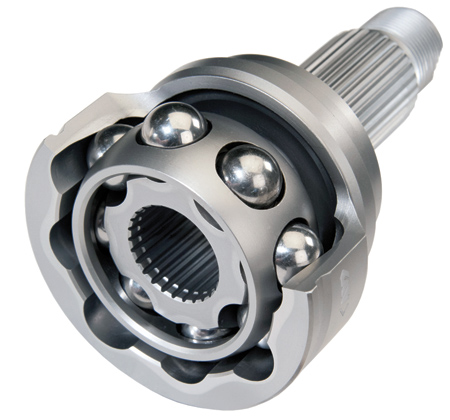
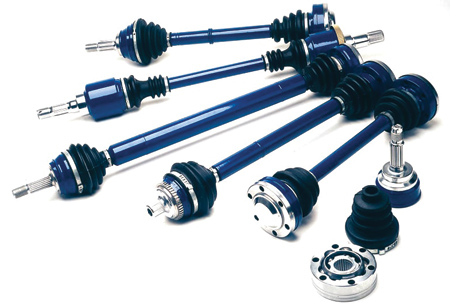
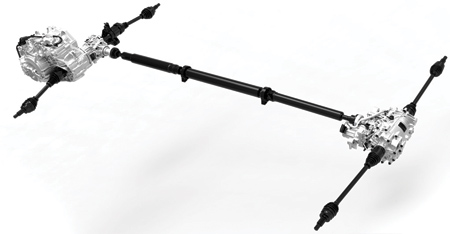
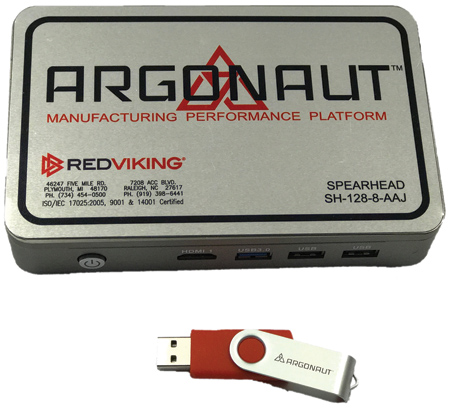
Argonaut edge of network device, used to capture and forward PLC data to a cloud or on premise server.
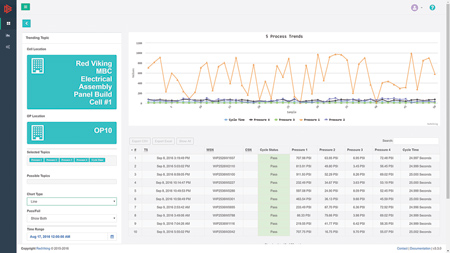
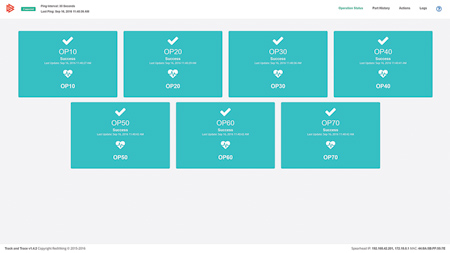
GKN Driveline is a manufacturer of automotive driveline products and, at its Sanford, NC, facility, produces an array of drive shafts and other products for automotive OEMs. "By adopting a platform approach to its manufacturing software, it has been able to gradually integrate traceability for multiple dissimilar systems and stage itself effectively for future growth," said a RedViking spokesperson.
Vertical Integration Creates Traceability Challenges
The GKN facility in Sanford is vertically integrated. It operates an in-house forge and machining center as well as performing assembly operations. Paths and processes vary by product, for example, potentially sharing common welding and hardening operations, then branching off to different assembly cells. It is a complex production process and creating an integrated traceability program was a challenge.
As IT Business Analyst Geoffrey Bennett, explains, "We were seeking an end-to-end traceability strategy and, in the course of our investigation, discovered the Argonaut system from RedViking (Plymouth, MI). "Argonaut," according to director for the program at RedViking Greg Giles, "is a highly flexible, scalable and cloud-based manufacturing performance platform that allows the user to easily scale from one operation to many."
Bennett's background includes the pre-production approval process to ensure delivery of quality products to internal and external GKN customers. He understands the importance of knowing exactly which processes impact which products throughout production.
"We seek to reach a place where we can hear the heartbeat of the production at all facilities and be able to take remedial action in an instant, aided by such systems as Argonaut," said Bennett.
Multiple Unique Quality Systems Needed to Come Together
Before introducing Argonaut, GKN used multiple tracking systems that varied by location, from internally created software applications to check sheets on paper. In each process, the drivetrain assembly was tracked with a go/no go determination made at strategically positioned test stations throughout the facility. Nothing would be pallet loaded for shipment to the customer until the product was inspected, checked for conformity with all performance specs and validated by an operator. Because multiple dissimilar systems were in place, this process differed from cell to cell and plant to plant, making it difficult to train operators and compare metrics across the organization.
Part Tracking and Test Data Create Quality Record
With Argonaut, assemblies are identified in each operation using bar code or RFID scanning equipment. Quality checking operations are performed at each step, ensuring that faulty parts are quickly identified and stopped before additional cost can be incurred.
Every cell validates the correct assembly of the drive shaft components, with various tests performed inline, gauging dimension, leak, seal integrity and other parameters. Each machine controller is connected to Argonaut, so if a part fails at any step in the cell, a quality alert is logged. If the specific machine test is showing an error, that fact is immediately evident, allowing proper corrective action to be taken.
The System Simply Will Not Allow Bad Parts
At the completion of each assembly, operators scan the part to a shipping container and the part's traceability record is again checked to ensure that all operations have been successfully completed before the part can be loaded to the skid. As GKN Manufacturing Engineer Gary Peterson comments, "We use a scan-to-skid process here. Each operator is able to see the value of the local scanning and how it connects to the overall production tracking."
Team Leader at GKN for this production cell, James Wiggins, describes the new system in this manner, "Each machine has its own data traces and the system, simply stated, will not let us make a bad part. There are a total of 80 checks on each part during production."
Bennett notes an additional benefit, "This functionality gives us an enormous advantage in every aspect of our production tracking and customer validation protocol, but it also affords us the core capability to estimate jobs more accurately."
Machine Data Integration is Critical
Implementation was a coordinated effort between GKN, RedViking and other suppliers. As Bennett notes, "Greg Giles (RedViking Program Director for Argonaut/MES) was instrumental in getting us all the data we required." Giles observed that there was great cooperation between his team, the GKN staff and the primary machine cell builder, Mecanizado. "Consideration must be given to tooling changes, PLC communication capabilities and, most critically, the complex handshaking involved with machine control," said Giles.
Bennett said, "Functionally, RedViking took all the GKN specs and builder data for the machine to create a `smart packing sheet' for all ops. All data is collected and tracked in a similar fashion to a conventional SPC system, but since the system is cloud-hosted, data is instantly accessible from remote locations and remedial action can be initiated instantaneously.
Store-and-Forward Ensures Data are Always Available
At GKN, Argonaut Track & Trace utilizes store-and-forward technology at each production cell, ensuring that production can continue to operate without losing data in the event of an interruption to data transfer. Speaking frankly on the possible scenarios with any new software implementation, Bennett said, "If the internet or our company intranet should go down, we can quickly return to a precise point in the process, owing to the Argonaut ability to instantly recreate all conditions."
Data is saved to cloud-hosted servers through a secure SSL encrypted and token-based authorization chain. The security of the system, as Giles explained, is extremely tight, with operators and line managers having precise but limited access to the data.
Cycle Time and Machine Fault Tracking
Beyond process and part validation, Argonaut collects cycle time and machine fault codes with each cycle. While the complete OEE application has not been launched on these cells, this data allows GKN to query for a subset of OEE information and can be gathered for cells throughout the facility. Since errors are infrequent, being able to query a large set of data across many product families helps identify parameters at fault. GKN is using its big data to identify and analyze rare events that would have been difficult to analyze in the past.
GKN started with an initial implementation of two cells in mid-2016. By year-end, it expected to launch Argonaut on an additional seven cells and continue with ten more cells in 2017. As Bennett observed, "This is one of the keys to the Argonaut value proposition for us. We were able to build gradually, from a core group of data points through complete connection of an entire work cell, with all production and machine performance values being tracked. Greg and his team took us through the steps in the implementation with great precision and attention to detail."
"Bar to Car" Production Monitoring
Long-term, the goal is to implement the Argonaut system plant-wide in Sanford, as well as other production facilities in the GKN family. Word is getting out about GKN's success at Sanford. As Bennett commented, "The other IT people are quickly learning what we are doing here and they want it, too."
"Because we operate our own forge department, we are developing a `bar to car' pilot concept. In conjunction with our Roxboro (NC) facility, we are targeting the implementation of Argonaut, so the system will be monitoring and maintaining the production of practically everything we make to drive vehicles from the transmission to the wheel."
For more information contact:
Geoffrey Bennett Jr.
IT Business Analyst
GKN Driveline
4901 Womack Road
Sanford, NC 27330
919-708-4500
www.gkn.com
Greg Giles
Director, MES/Argonaut
REDVIKING
46247 Five Mile Road
Plymouth, MI 48170
734-454-0500
www.redviking.com