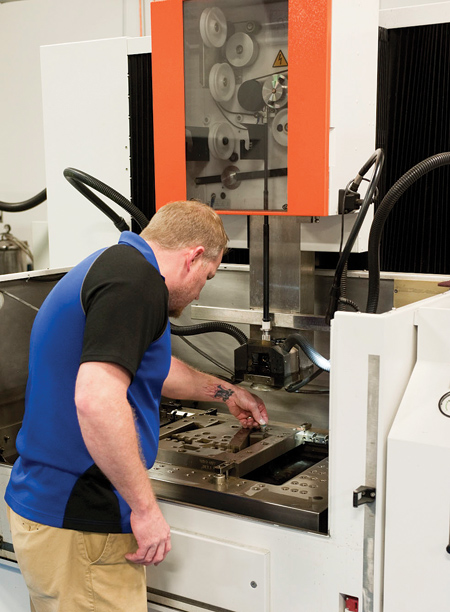
(inset): To produce parts, EDM Technologies relies heavily on its lineup of AgieCharmilles EDMs, including the Robofil FI 440 ccS wire EDM.
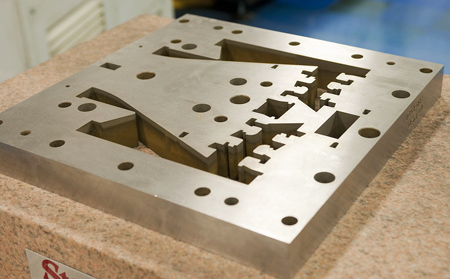
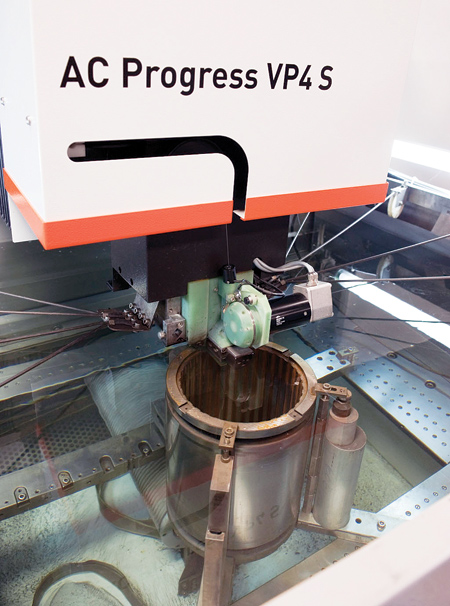
The AC Progress VP4 S is the biggest wire EDM machine at EDM Technologies. It handles parts measuring up to 51.181" x 39.370" and as tall as 20.078".
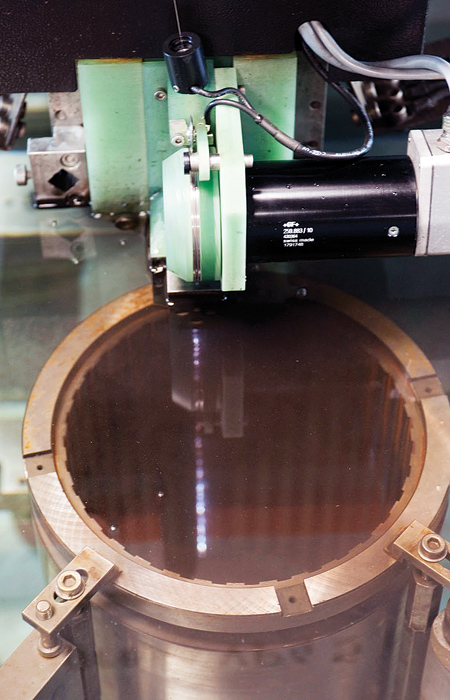
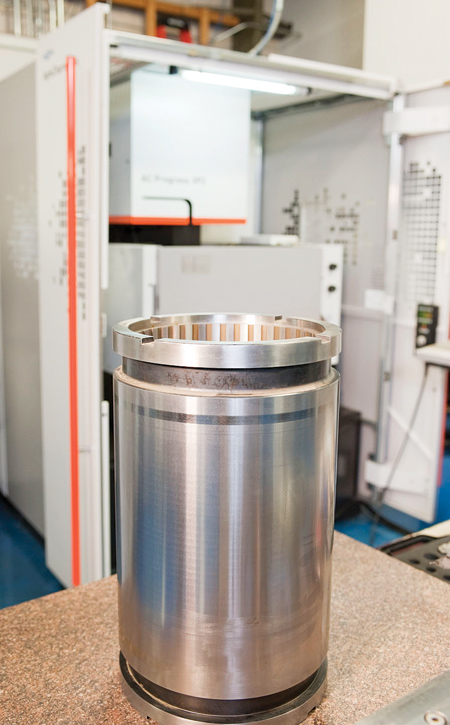
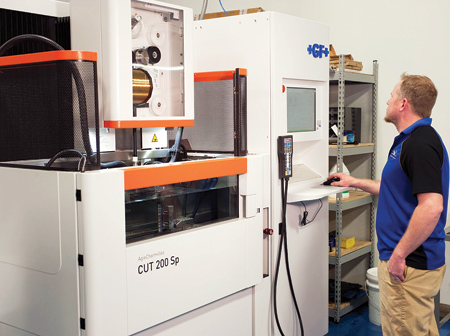
(inset): The AgieCharmilles CUT 200 Sp (Speed Edition) provides enhanced precision, fast spark-to-spark wire threading, high energy efficiency and high productivity when cutting parts of variable heights. Advanced CC (clean cut) Generator technology eliminates recast, or white, layers on parts.
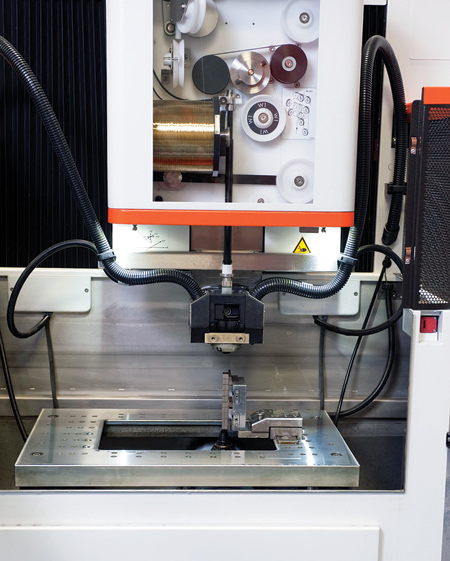
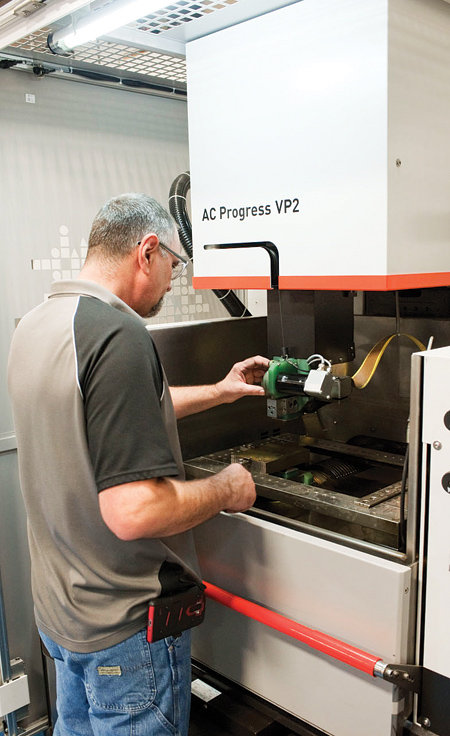
The two AC Progress wire EDMs at EDM Technologies, including the AC Progress VP2, have special wire drive systems that allow the shop to use two different wires in a single part contour.
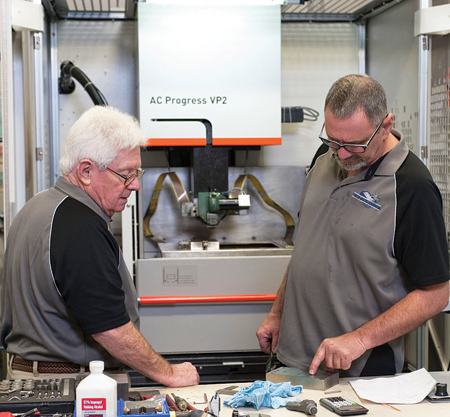
(l-r) According to John Cater Sr., President and Founder of EDM Technologies, and his son John Cater Jr., Vice President, technology advancements on the AgieCharmilles EDMs have been key to continuous improvement in the shop's EDM operations from one generation of machines to the next.

EDM Technologies does a lot of build to print work and specializes in challenging jobs, usually those involving very small or very tall parts with extremely high precision tolerance requirements. Part range in size from 0.020" x 0.020" and 0.005" thick to 3' x 4', over 20" in height and weighing as much as 6,600 lbs. Part materials range from steels and aluminum to copper tungsten.
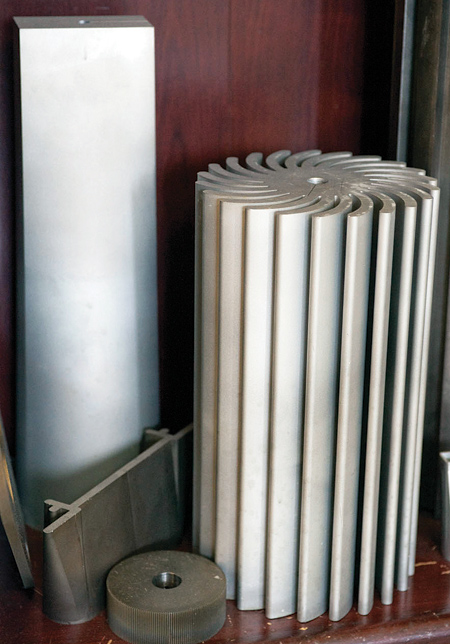
"EDM Technologies Inc. keeps customers coming back by providing four key services that often prove a challenge for its competitors: price, quality, delivery and, most importantly, zero rejects," said a company spokesperson. "To consistently achieve all four, the shop must always stay ahead of the curve in terms of the latest in electrical discharge machine (EDM) technology."
According to John Cater Sr., President and Founder of EDM Technologies, and his son John Cater Jr., Vice President, many shops claim that it is impossible to provide customers with all four of these services.
"Our California customers are often baffled by how quickly we can turn around jobs," said John Jr. "They continue to give us more work, and we consistently deliver it all on time, with zero rejects and at prices considerably less than our competitors - even those located on the West Coast close to the customers. We are able to do this because we have some of the most experienced and talented people running, what we believe, is the industry's best EDM equipment on the market today."
The EDM Technologies shop floor is a virtual showroom of AgieCharmilles EDMs from GF Machining Solutions. With 17 EDM machines, the shop's wide range of EDMs represents a progression of that technology from about 1988 up until the present and how the shop has kept pace with it over the years.
While the majority of machines are wire type, the shop does have two sinker EDMs and a small hole machine, all AgieCharmilles. Of the entire EDM machine lineup, the most recent models include a CUT 200 Sp (Speed Edition), two AC Progress VP machines and a DRILL 20.
The AC Progress VP machines have unique wire drive systems that allow EDM Technologies to use two wires in a single part contour. The shop's AC Progress VP4 is its biggest machine and handles parts measuring up to 51.181" x 39.370" and as tall as 20.078".
"The CUT 200 Sp EDM provides fast spark-to-spark wire threading, high energy efficiency and, most significantly, unmatched productivity when cutting parts of variable heights," said the spokesperson. "It also offers flexibility through its ability to reliably hold micron tolerances." The shop's DRILL 20 is a high-speed, high-precision vertical drill that complements wire EDM systems in the drilling of start holes.
According to John Jr., what classifies a particular EDM as "the best" is a machine's level of capability when it comes to overall precision, angle and taper generation, surface finishes, reduction of non-cut time and reliability for lights-out operation. For his shop, a machine must excel at all of these.
"Most individuals involved with EDM in one way or another doubt there will be huge jumps in overall machine burn speeds, but rather gradual increases, if that," said John Jr. "However, EDMs will continue to get better and generate even tighter tolerance parts along with mirror-like surface finishes, and do so with far less required skim cuts. For us, the advancements of EDM generator technology on our AgieCharmilles machines have given us just such continuous improvement in our EDM operations from one generation of machines to the next."
In addition to higher precision and better surface finishes, advanced CC (clean cut) Generator technology, such as that of the CUT 200 Sp, also eliminates recast, or white, layers on parts generated from the EDM process. This "clean cut capability," in the words of John Jr., is mandatory for the shop to win any aerospace work.
"Aerospace customers want parts with zero recast layers because those layers can reduce a part's original base hardness," explained John Jr. "This is why many OEMs in the industry have long shied away from the EDM process. Fortunately for us, our AgieCharmilles EDMs cut cleanly, and we continue to bid on and win work that would have been impossible because of the EDM stigma in the aerospace industry."
As a result, aerospace is one of the EDM Technologies' main market segments. The shop's other markets include motorsports, electronics and medical.
While the fast cutting capabilities of the AgieCharmilles EDMs contribute to increased productivity, their short burn-to-burn times are what really boost output for EDM Technologies. The machines provide overall speed and reliability for non-cut operations, such as wire changeovers and rethreading, as well as the remote connectivity (on the newer EDM models) the shop needs to confidently run lights-out and unattended.
"On our two AC Progress VP machines, we switch from one wire to another faster than we ever did in the past," said John Jr. "In fact, the wire changeover time of our newer machines is practically nil as compared with our older equipment, which still change over relatively quickly."
He added that wire changeover speed is very important because the shop often rough cuts parts with larger diameter wire, then runs finish passes with smaller diameter wire for accuracy and surface finish. Changeovers can also be from one type of wire to another, such as a basic brass wire to rough cut and then a coated one for the finish passes.
Along with fast wire changeovers, the AgieCharmilles EDMs perform wire threading quickly and precisely. The shop's older machines take a minute or two to cut the wire, move to a new position and rethread the wire. The newer EDMs, on the other hand, do it in seconds, and John Jr. said that such a reduction in wire threading time translates into major savings when processing parts having thousands of individual openings, each of which needs EDM.
According to John Sr., the key to really maximizing production output, especially for an EDM shop, is lights-out unattended operation. "We must run machines overnight and during the weekends if we want to compete," said John Sr. "Because of our ability to run lights-out, we gain a whole additional shift worth of production for each machine, turning a five-day week into a seven-day week in terms of output."
To further boost the reliability of its lights-out operations, EDM Technologies has cameras on all of its machines and monitors them remotely via smart phone. On top of that, the newer machines give the shop the ability to actually log into the machine's controls via smart phones to monitor operational status and make adjustments if needed.
In addition to remote connectivity, AgieCharmilles programing technology allows EDM Technologies to customize how it runs parts, which is especially beneficial for unattended operations. For instance, the shop can program a machine to rough cut all the required openings of a part instead of first rough cutting and then finish cutting each one. Such programming capability eliminates any issues with slugs and allows machines to keep working nonstop overnight. In the morning, the shop simply cuts the slugs free and does all of the finish passes.
EDM Technologies does a lot of build to print work and specializes in challenging jobs - usually those involving very small or very tall parts with high precision tolerance requirements. Parts range in size from those handled with tweezers to others that weigh thousands of pounds.
One of the smallest parts the shop EDMs measures only 0.020" x 0.020" and is 0.005" thick. Bigger parts can measure 3' x 4', stand over 20" in height and weigh as much as 6,600 lbs. Part materials range from steels and aluminum to copper tungsten.
Job lot sizes range from one part to those requiring tens of thousands per month on a regular basis. On average, jobs typically involve between five and 20 parts with a lot of repeat work from regular customers, some of which the shop has had for as long as 30 years.
One month, the shop might ship only a couple of jobs that involve large lot sizes. In other months, that amount could be 30 or more jobs, and in still other months, hundreds of jobs will ship. Typical job turnaround times vary from hours - with some customers waiting in person at the shop - to a couple weeks.
All of the shop's operators can program, set up and run their own jobs. Everyone is fully trained and completely self-sufficient. This is a must because a lot of the shop's parts require special fixturing, much of which it custom builds. It is this proprietary tooling that allows the shop to EDM parts so small they are barely visible with the naked eye.
"We spend additional time and money to develop such custom fixtures, but in the long run, they provide much more in terms of output and increased overall profit margins," said John Jr. "We may spend 10 hours on a fixture, but if it saves us an hour per day in set-up time for the life of a machine, that is huge."
Burn times at EDM Technologies can vary from seconds to as long as 300 hours of in-the-cut time (that particular part required wire EDM of 7,000 individual die openings).
EDM Technologies' history with GF Machining Solutions started 40 years ago with John Sr. and a Charmilles Andrews EF 330 wire EDM. Since then, the shop has owned nothing but AgieCharmilles machines. "The reason for that is the company's service, which has been second to none," said John Sr.
During its entire history, EDM Technologies has experienced steady business growth year to year, which it attributes to increased work from existing customers as well as work from new ones.
"We constantly keep our eyes open for what is next in the EDM technology world. If there is a machine that can improve upon our existing processes, we will obviously jump on board," said John Jr. "Regardless of what the future holds in terms of part types, we will incorporate any EDM technology that allows us to not only increase production, but most importantly continue to provide customers with even higher quality parts at the lowest possible prices and delivered in the shortest amount of time possible. It is a safe bet that the technology will most likely come from GF Machining Solutions."
For more information contact:
EDM Technologies, Inc.
325 Bell Park Drive
Woodstock, GA 30188
866-924-6602 / 770-924-8328
info@edmtechnologies.net
www.edmtechnologies.net
GF Machining Solutions
560 Bond St.
Lincolnshire, IL 60069-4224
800-CTC-1EDM / 847-913-5300
www.gfms.com/us