
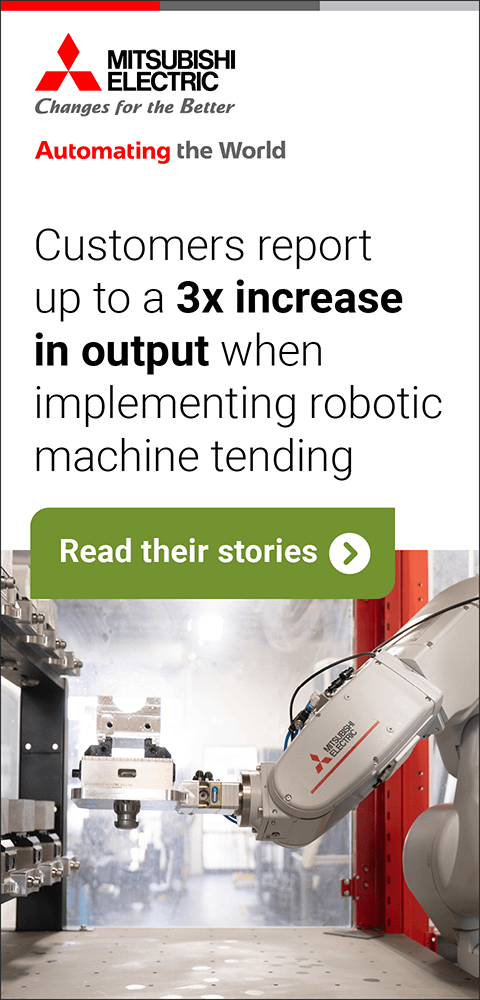
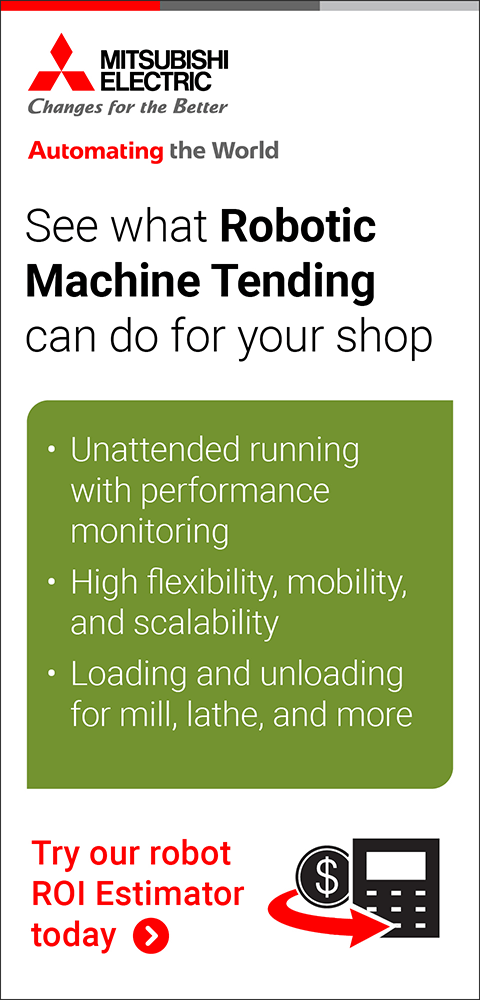
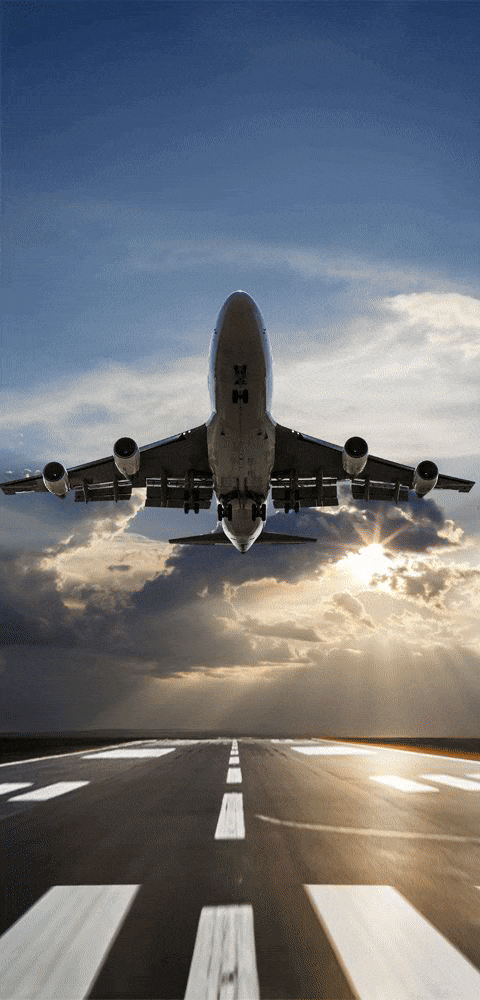
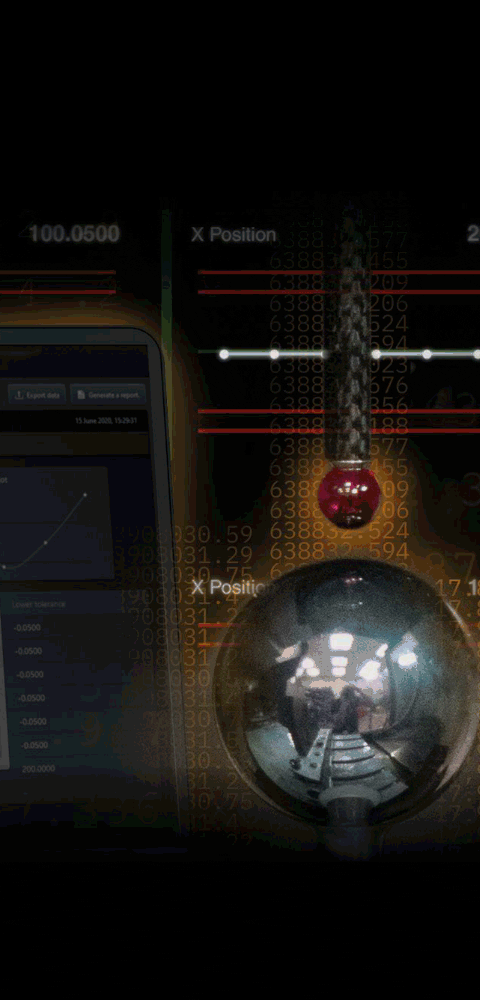
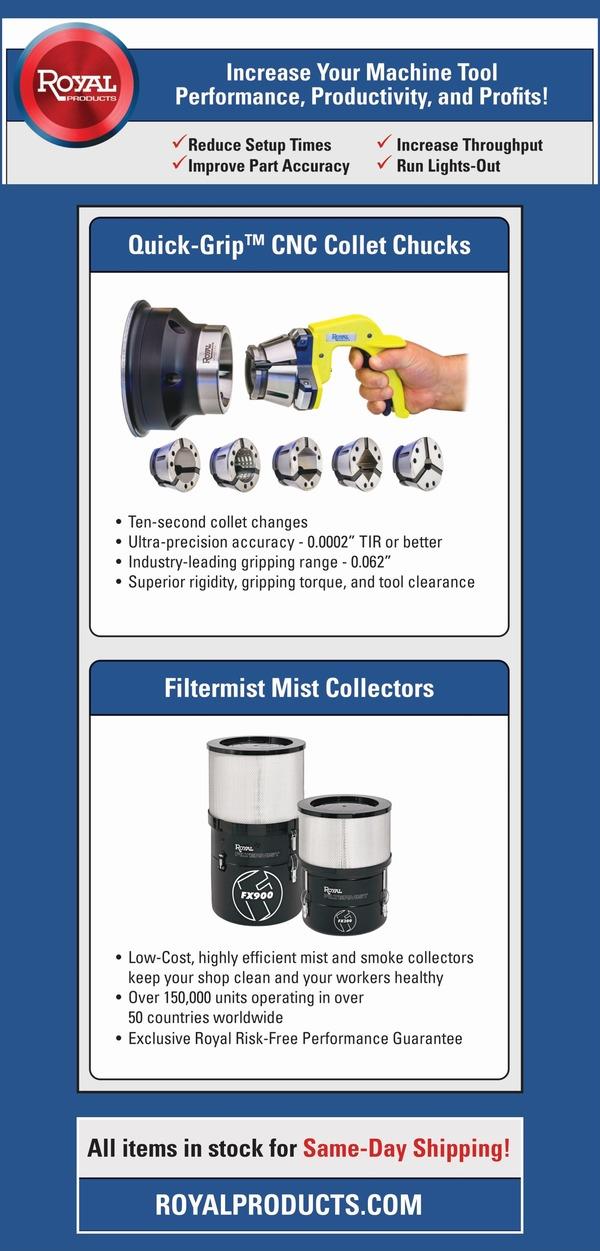
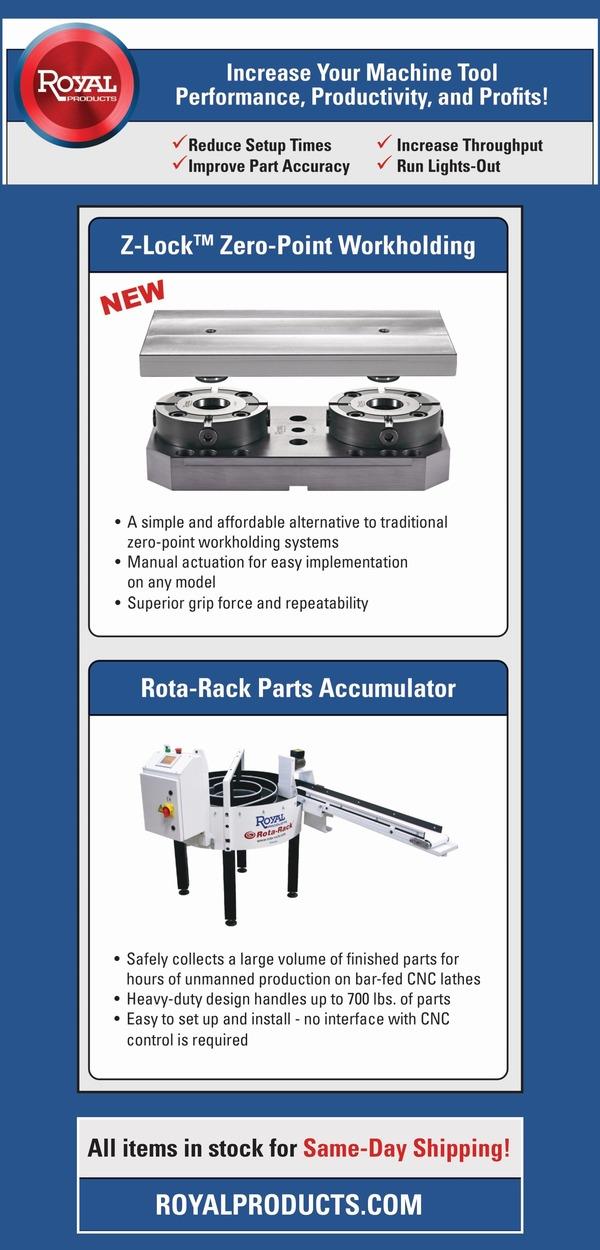

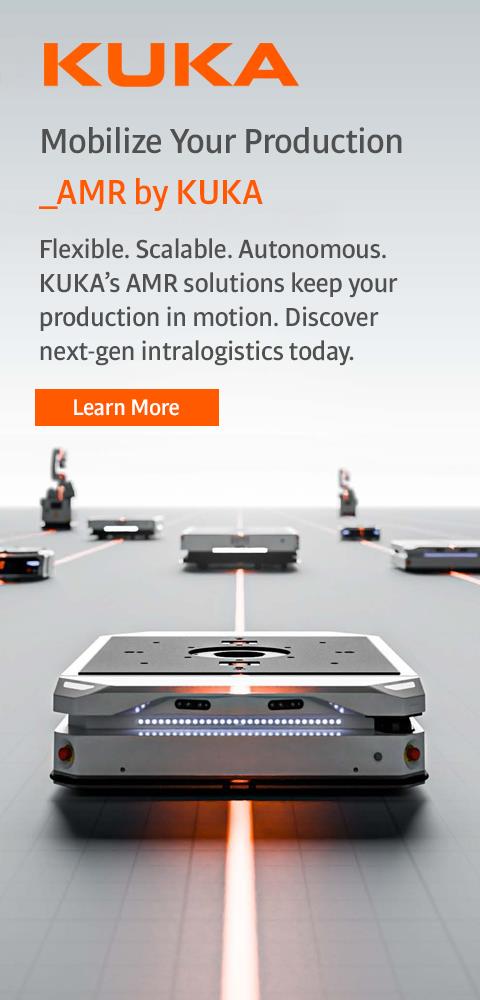
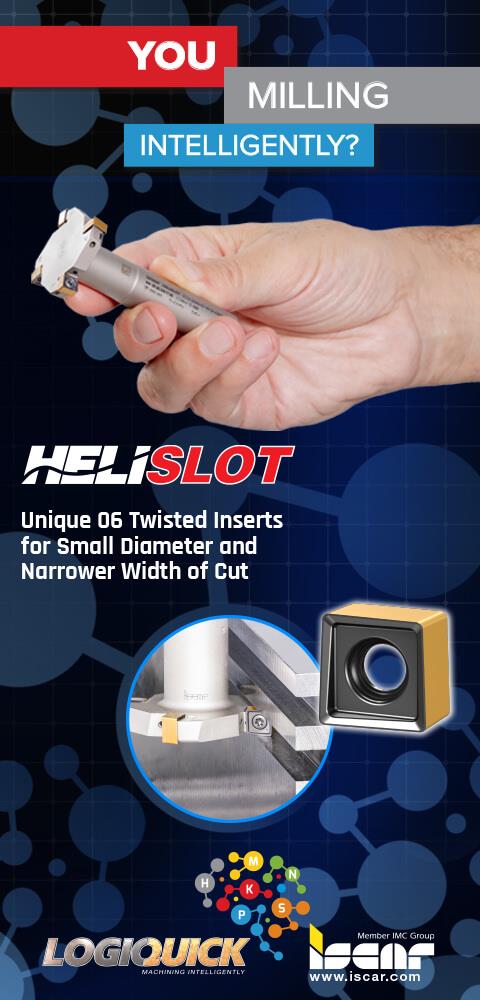
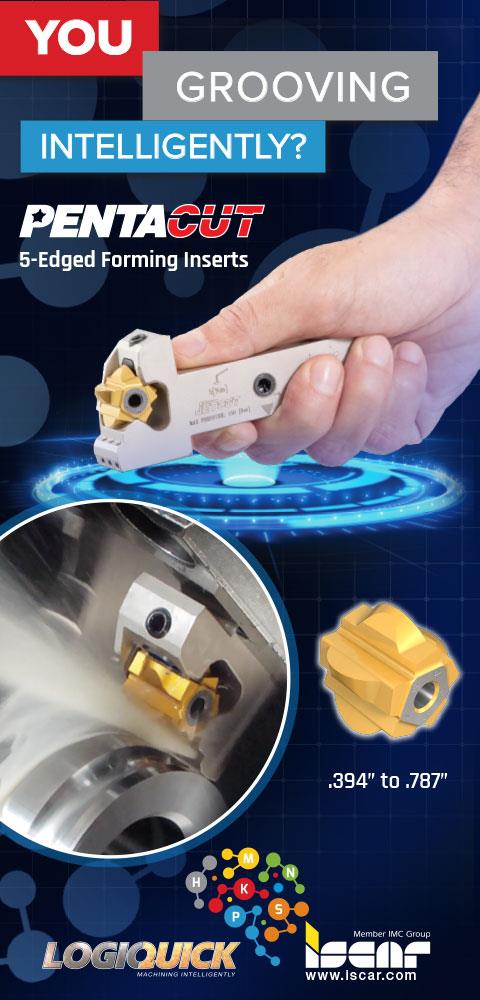
Couplings Designed for Encoder Applications
January 1, 2016
Control-Flex couplings from Zero-Max are designed for encoder applications. Where speed and positioning feedback in a system is critical, Control-Flex couplings are designed to minimize a system's reaction forces for more precise and repeatable operation and longer life.
Designed with a parallel linkage-style flexible disc, Control-Flex provides radial flexibility to reduce reaction forces such as side loads on shaft bearings and seals that can be caused by shaft misalignment. The Control-Flex disc is built to allow parallel, angular and axial shaft misalignments while maintaining constant transmission of torque and angular velocity.
Designed with aluminum clamp-style, zero backlash hubs, the Control-Flex provides a low weight/low inertia solution. Electrically insulating flex discs prevent electrical current passing between the system shafts through the coupling. These discs are made of a special compound selected for its flexible durability and dielectric qualities.
Precision designed, Control-Flex couplings consist of two hubs (to be attached to the system shafts) and a center flex member. This flexible member is affixed to the hubs through quality pins that are designed to make separating easy if required. Two versions of the coupling are available: a single-flex disc version for standard torque capacity, and a two-flex disc version for increased torque capacity and torsional stiffness.
Control-Flex also offers electrical isolation and low reaction loads. Control Flex couplings are designed for use in packaging, medical devices, machine tool, conveying and automated assembly systems that utilize encoder feedback devices.
For more information contact:
Zero-Max, Inc.
13200 Sixth Avenue North
Plymouth, MN 55441-5509
800-533-1731 / 763-546-4300
sales@zero-max.com
www.zero-max.com
< back