
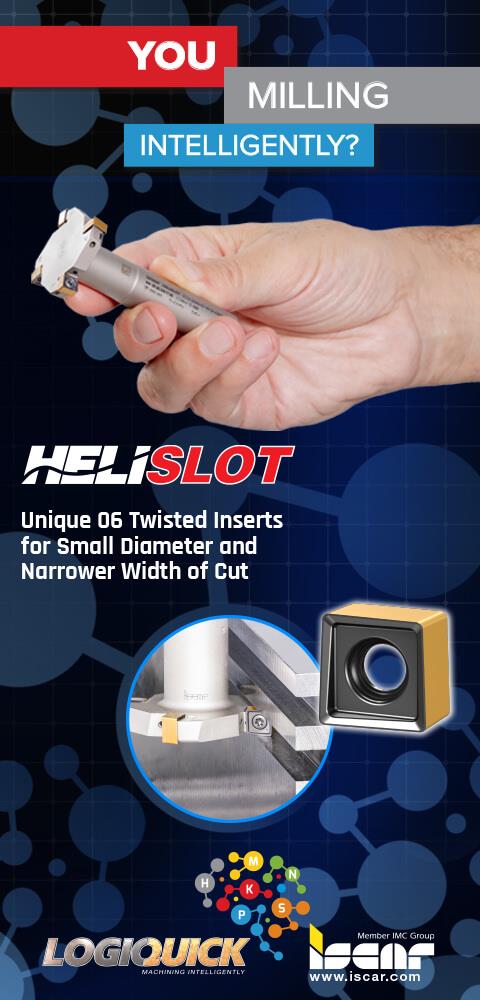
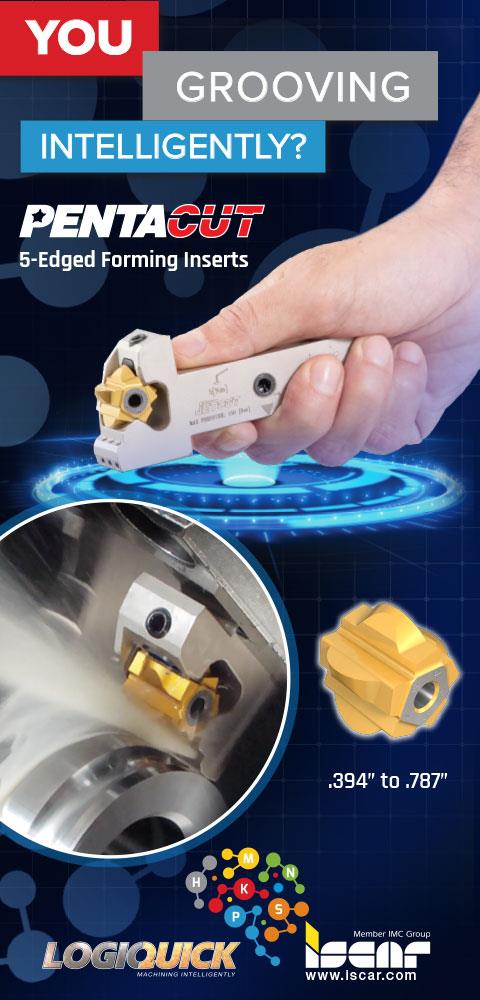
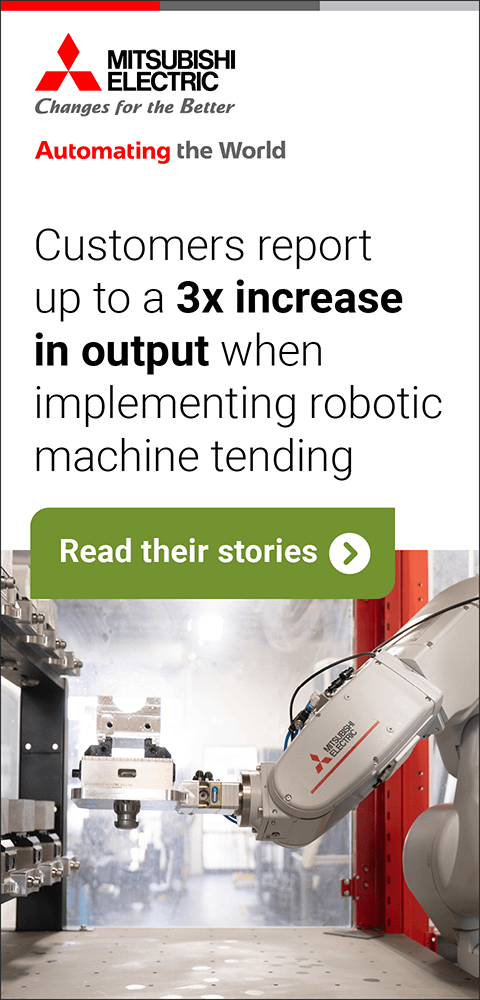
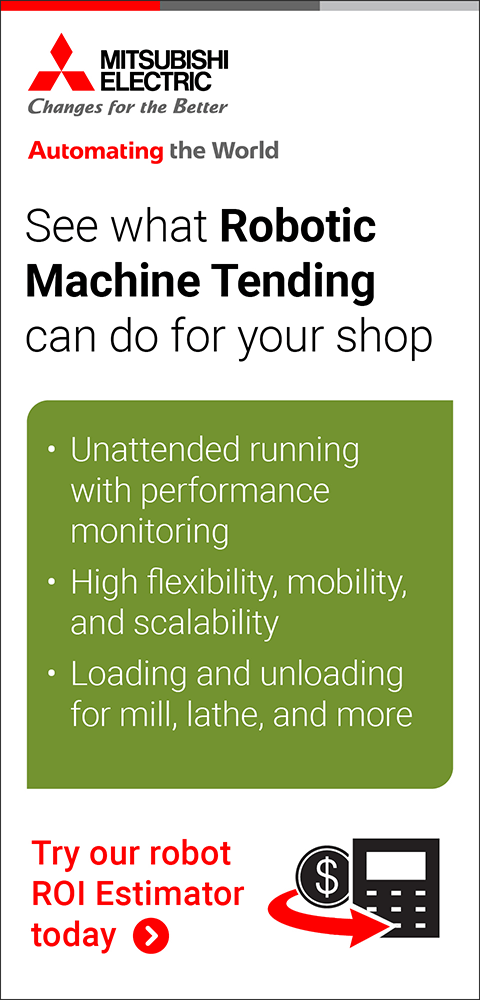
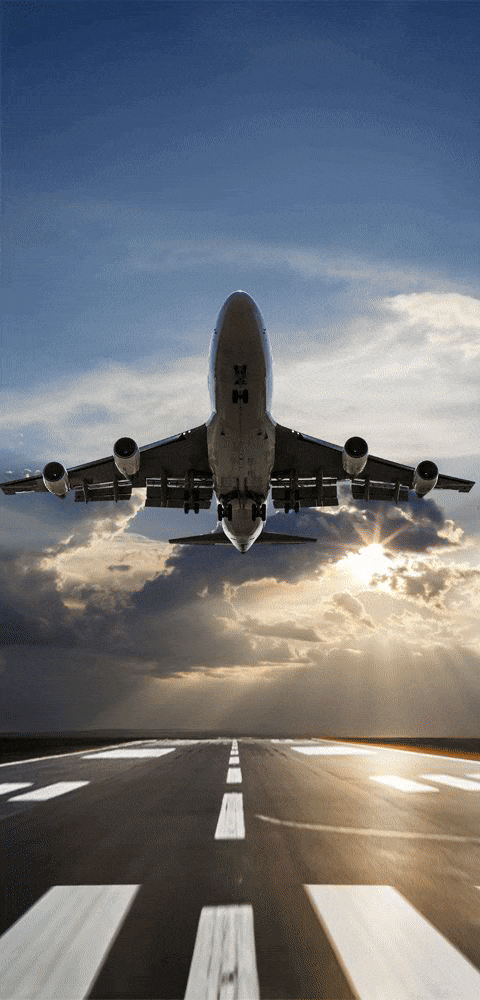
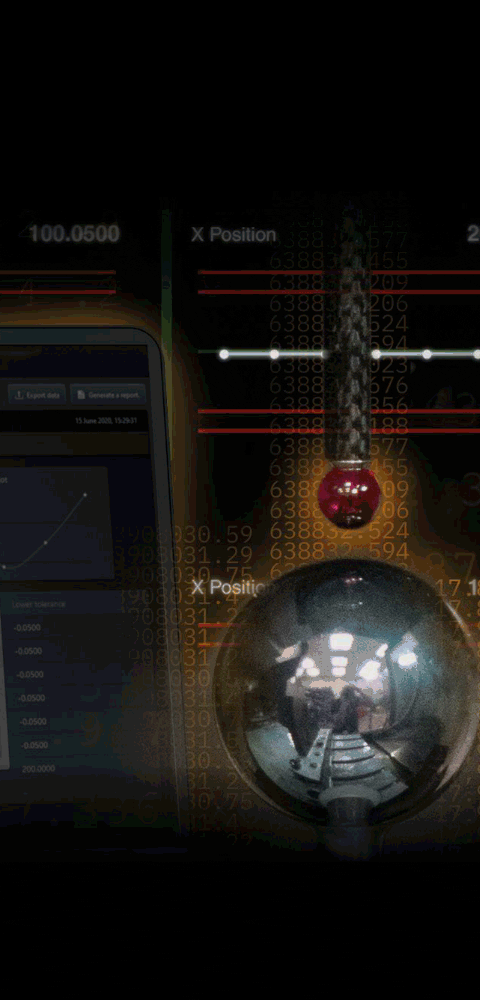
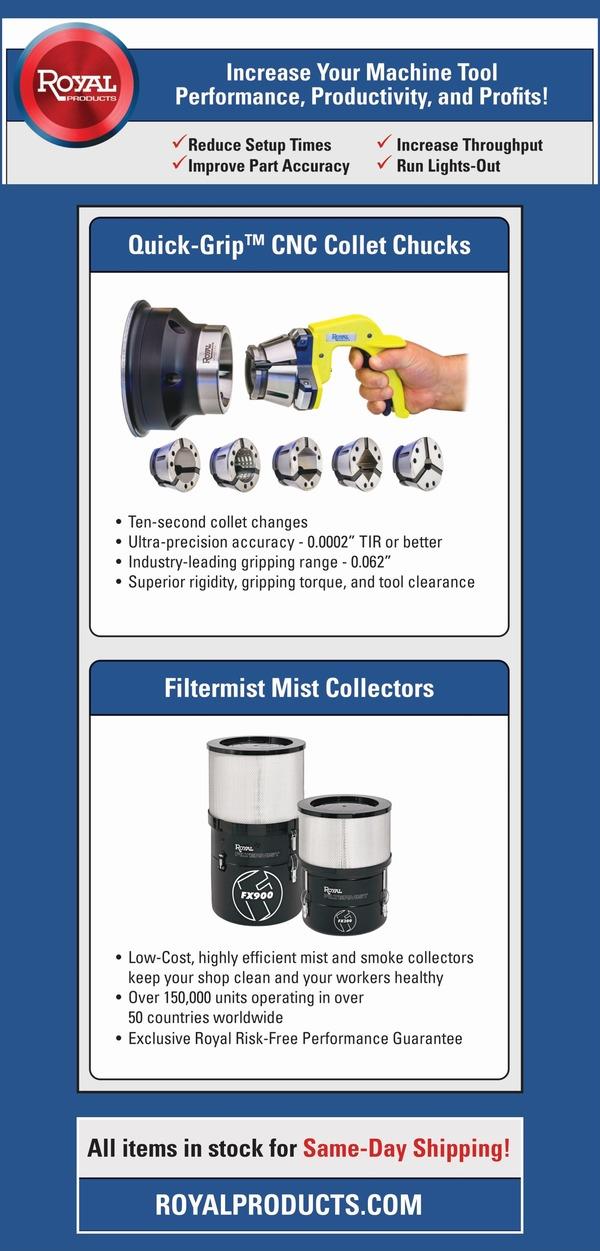
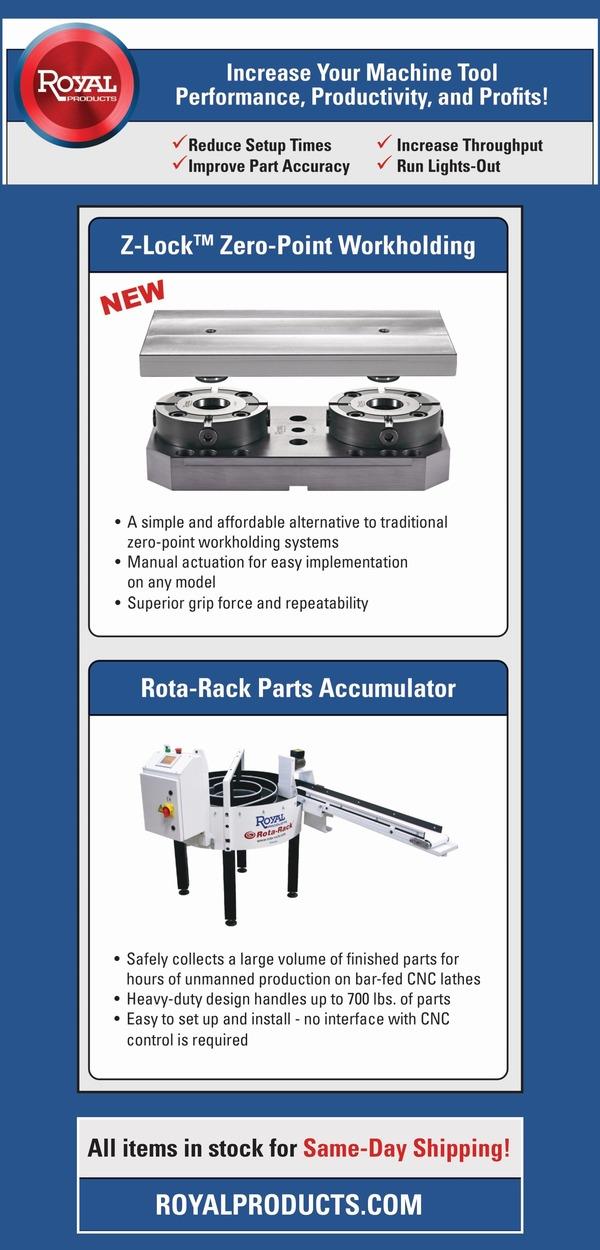

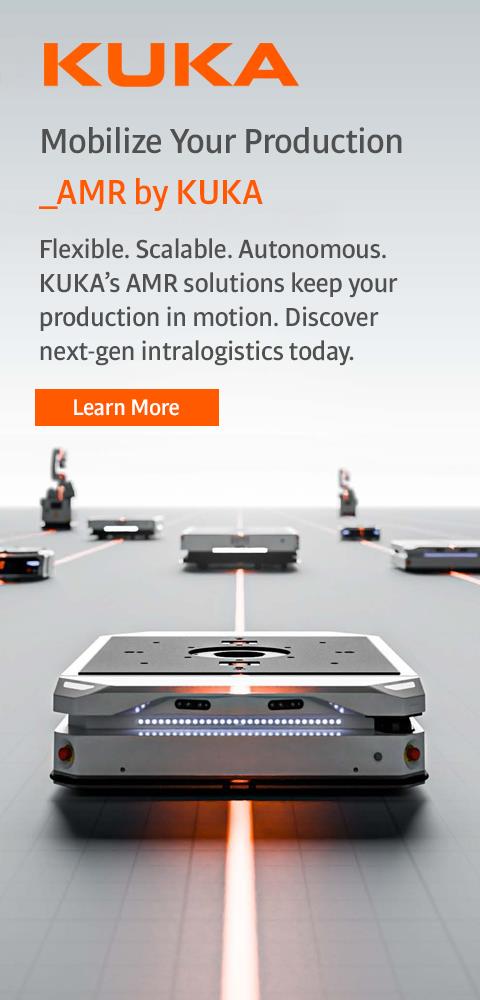
Multitasking: 3-D Machining and Vertical Turning
January 1, 2016
Burkhardt+Weber has expanded its model range of the multitasking MCT series with the MCT 1250. A variety of adaptable chip cutting tasks with rotating tools, like milling, drilling, boring, grinding, CNC facing, 3-D milling and more are combined with rigid vertical turning for large part sizes. The high-speed torque table with up to 1,400 x 1,600 mm (55.1" x 63.0") pallet size will accommodate parts with work volumes within 2,800 mm swing and 2,500 mm part heights. "Precise machining results are secured with controlled cooling of the table torque motor that ensures table frame stability and precise machining," said a company spokesperson. The table design delivers turning speeds up to 350 RPM and uses a contact-free rotary sealing system to avoid wear from friction. An automatic balance control system addresses load distribution with high turning speeds.
The main milling spindle, with 41 kW (55 HP) and 1,400 Nm (1,032 ft.-lbs.) low end torque, uses an HV swivel design for machining with rotating tools, which includes 3-D milling and CNC turning for steel, cast iron and other tough to cut alloys. The two-step geared spindle unit is cooled by four individual cooling circuits for continuous operation at maximum speed. The spindle can automatically orient from horizontal to vertical work position in less than 2 sec. while running at 8,000 RPM. A master-slave axis drive system is built for precision performance in contouring and clamped mode. A hydraulic brake system supplies 6,500 Nm (4,800 ft.-lbs.) of holding torque.
For high capacity or precision CNC turning an arrangement of four symmetrically arranged clamping cylinders, located 250 mm (9.84") apart from each other securely, lock the turning-tool adapter in place. The arrangement transfers shock loads from turning direct into the machine frame and thus safeguards the spindle bearings, achieving high capacity and precision full featured turning results. The turn toolholder and the turn tools are automatically loaded from the rack-type tool magazine. Tool capacity for stationary tuning tools or rotating tools of up to 1,200 mm length and 165 lbs. of weight provide flexibility for rigid tool layouts. A multi-station tool load station features ergonomic, safe tool loading during machine operation.
For more information contact:
BURKHARDT+WEBER LLC
Machines and Methods
Theodor Sprenger
1845 Airport Exchange Blvd
Erlanger, KY 41018
859-308-6625
Theodor.Sprenger@burkhardt-weber.com
info@burkhardt-weber.com
www.burkhardt-weber.com
< back