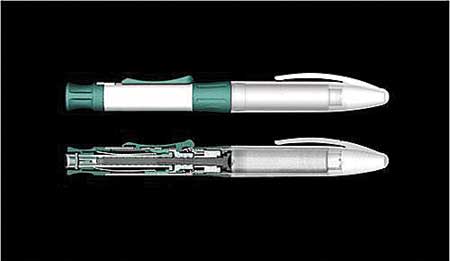
Computed tomography (CT scan) medical component X-ray
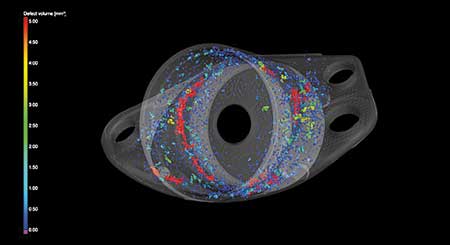
Computed tomography (CT scan) void analysis
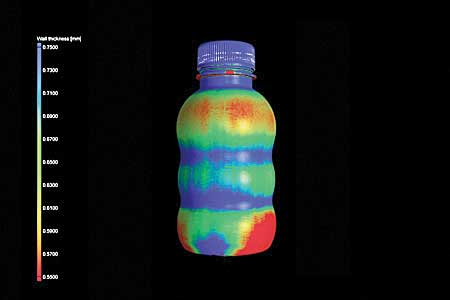
Computed tomography (CT scan) wall thickness analysis
A very important stage in the manufacturing and production cycle of a part is designing and verifying a prototype. Very often in the medical, automotive or aerospace industry, we see very expensive and valuable parts being cut open to locate internal failures or to retrieve internal measurements. This certainly proves to be an issue, as such parts are left destroyed and can no longer be functional after the testing process. However, the introduction of a nondestructive testing method that can inspect parts internally and accurately in 3D has brought a turn in the industry.
Industrial CT scanning is a nondestructive testing method that can accurately inspect parts internally and externally in 3D. This non-contact, X-ray technology allows an object to be scanned in free state form, leaving the part available for use after testing. Traditionally, computed tomography (CT) is primarily used to scan the human body to retrieve internal bodily data. The adaptation of the industrial use has been quite remarkable, as this method proves to be useful and effective for scanning objects. Although the scanning process is quite complex, specialized labs such as JG&A Metrology Center can make it simple.
A CT machine consists of three main parts:
- Rotary table
- X-ray source
- Detector panel.
To begin, an object or part is placed on the rotary table. As it spins 360°, the X-ray source shoots through the part, toward the detector panel, which captures several thousand 2D X-ray images. These images are then re-constructed into a 3D model using software. Without damaging or cutting open the part, the viewer can retrieve internal measurements or locate internal defects. The inspection can be taken further by applying different types of analysis to the resulting scan.
Industrial CT scanning provides the user with many routes in terms of accessibility of different types of data. Apart from scanning for simple fit and function purposes, one can also acquire a CAD model from scratch through the CT process for reverse engineering solutions, or compare a CAD model of the part with the scanned results to ensure the credibility of the part is not compromised. Further, the technology can be used to locate, measure and view internal porosity/voids and inclusions with very high accuracy. A user can also scan and compare multiple identical parts for a comparison analysis or retrieve general dimensions and tolerances. This technology can even be used to measure wall thickness for parts or scan to inspect fibers. The options presented with using CT systems are truly overwhelming, as almost any type of material can be scanned.
The advantages presented in this nondestructive testing method are clear. CT scanning can reduce potential operational costs by minimizing time allocated toward pre-production design and production. This method of inspection aims to enhance product quality and provides a high level of accuracy that would be difficult to assume with any other nondestructive testing method. Most importantly, it is a fast and easy internal inspection method that leaves the part intact.
JG&A Metrology Center is a specialized lab focused on providing 3D internal part inspection services using industrial computed tomography (CT) equipment.
Authored by JG&A Metrology Center
For more information contact:
JG&A Metrology Center
269 Walker Street
Unit #133
Detroit, MI 48207
855-962-5300 / 313-996-5840
sales@jgarantmc.com
www.jgarantmc.com